The race car driver careens around the track, narrowly missing the walls along the side. They make the turn expertly and quickly and slide across the finish line, wheels squealing as they hit the brakes. Excited spectators in the audience probably don’t realize that those brakes are able to operate seamlessly around tight turns and high speeds because of silicon carbide brake rotors.
Idaho National Laboratory (INL) is playing a key role in the scientific and engineering development of such high-tech brake rotors. Applications extend far beyond race cars; the lab’s work will focus on improving tactical vehicles to enhance their survivability.
With its state-of-the-art Electric Field Assisted Sintering (EFAS) machine, the DCS-800, the lab offers a cleaner, more efficient and cost-effective manufacturing research and development option for both large companies and small businesses, like Carbon SiC Technologies Inc.
What is Carbon SiC Technologies?
Carbon SiC Technologies Inc. is a Henderson, Nevada-based two-person company funded by a Small Business Innovation Research grant through the U.S. Army.
“We had been working for about five years to develop an inexpensive composite for carbon fiber reinforced ceramic brakes for a project we’ve contracted with the Army,” said Clifford Leonard, the company’s founder, president and CEO. “We’ve been able to produce our products on smaller machines, but finding an opportunity to test the scale-up of this design was a huge challenge.”
This challenge put Carbon SiC Technologies in danger of running behind the deadline outlined in its contract. The company discovered INL’s EFAS capabilities through a mutual partner, Thermal Technologies. When INL started the DCS-800 operations, Carbon SiC Technologies became the first corporation to work with the lab on scaling up its technology, leveraging industry access to the DCS-800.
Why EFAS?
EFAS reduces the costs of creating advanced materials. Instead of using radiant heat, EFAS sends electricity through the die containing the materials, and sometimes through the material itself. In the simplest sense, the electricity generates heat to fuse together the particles of powdered metals, ceramics or a mixture of both.
Traditional ceramic brakes are commonly manufactured through reactive melt or chemical vapor infiltration. Both processes are used for making high-density composites. But rather than fusing materials together through a combination of pressure and electromagnetic heating, the technique sends a liquid or gas through the materials, where it settles into the porous parts, binding it together. A subsequent step requires high temperatures to increase the part’s density and generate the desired chemistry and structure, further complicating the process and increasing cost.
“Ceramic brakes created through melt infiltration can cost at least $1,800 a unit to replace, and sometimes much closer to $8,000 a unit,” said Leonard.
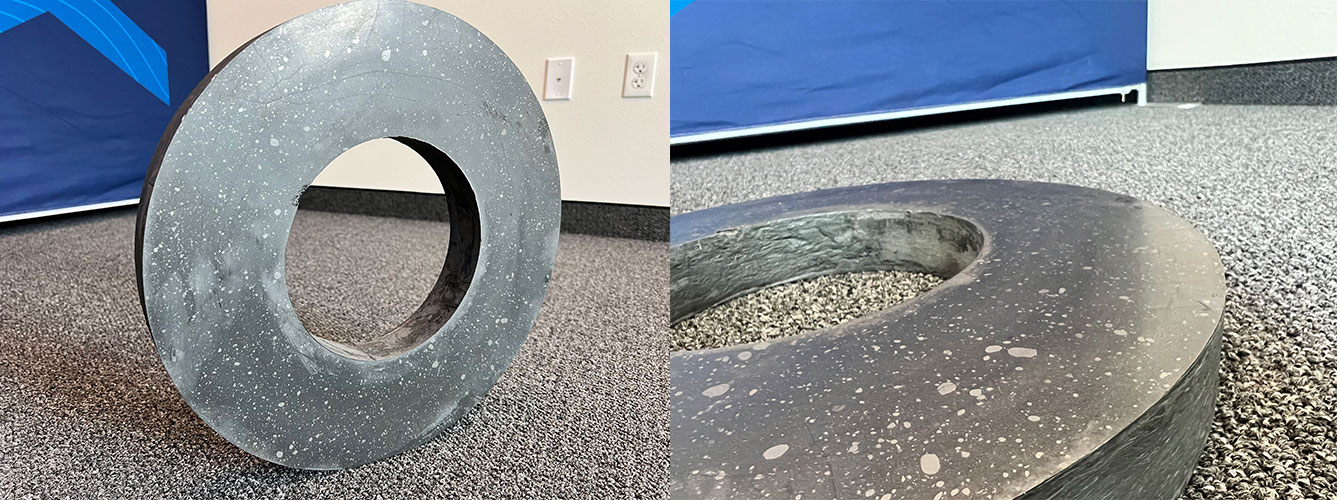
“Not only are these processes expensive but they’re also time-consuming. Polymer infiltration can take eight to 10 weeks to manufacture a new set of brake rotors,” said Jorgen Rufner, the EFAS research lead at INL. “With EFAS, we can cut the manufacturing time down to one-tenth of traditional methods, and significantly reduce cost.”
Unlike some faster, cheaper processes, EFAS does not cut any corners with quality. In fact, the brake rotors created through EFAS last up to four times as long as the typical ceramic or iron rotors.
What’s so great about high performance brake rotors?
For heavy-duty vehicles (such as transport trucks or large military equipment) or high-speed vehicles (race cars), iron rotors have been the norm for many years. But such rotors are heavy, sometimes even reaching about a quarter of the weight of the entire axle.
“When you’re rotating a heavy object or an object at high speeds, you don’t want that object to have a lot of inertia,” Rufner said. “A heavy-duty vehicle could have upwards of 600-800 pounds of brake rotor alone. Reducing that weight increases the acceleration potential and gas mileage, while decreasing the distance needed to completely stop the vehicle.” This is especially vital for military vehicles, which may need to quickly remove people and equipment from dangerous situations.
Carbon fiber reinforced silicon carbide brake rotors wear down much slower and can move heat away from the brake pad faster than iron rotors. This makes them safer in hard braking situations, where brakes can’t manage heat well. Hard braking can cause brake fluid to boil, creating “brake fade,” where the pedal is no longer able to apply pressure to the brake pad system. In extreme cases of hard braking, brakes can burn out earlier or even catch fire.
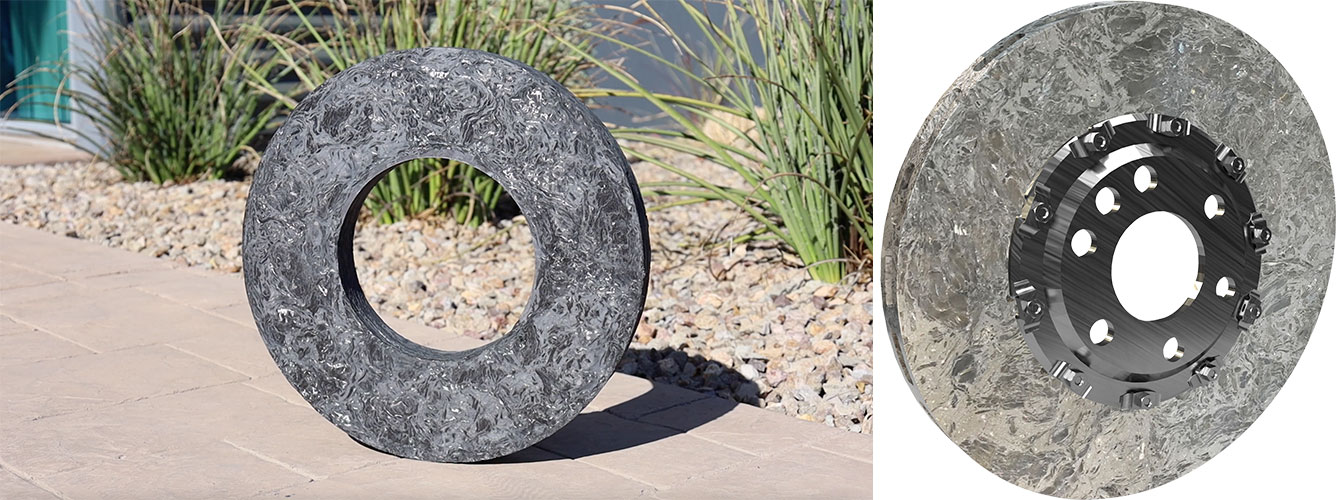
These rotors can also impact DOE’s decarbonization mission. They can be used in large internal combustion engine vehicles and for electric vehicles, which are typically much heavier than their internal combustion engine counterparts and require more robust braking solutions.
What’s next?
Carbon SiC Technologies wants to continue researching and testing its brake rotor material to address these cost barriers. EFAS has enabled these efforts. Leonard said his company could have lost its contract with the Army had they not been able to supply a scaled-up component as proof of their principle.
“We wouldn’t have been able to succeed with our contract without the support of INL and access to its DCS-800 system,” he said. “Scaling up a technology of this caliber successfully the first time seemed next to impossible. However, EFAS technology at INL made it possible.”