We know the beginning: dead sea life on the bottom of the ocean. And we know the end: petroleum, the result of heat and intense pressure acting on that organic matter over eons. But exactly how you get from start to finish is still a mystery. Solving that riddle could improve many industries.
“It could be biomass conversion,” said Gorakh Pawar, a research scientist at Idaho National Laboratory. There could be, for instance, enhanced production of ethanol or another renewable fuel from organic feedstocks.
“If you understand these polymeric materials, then you can efficiently design these production processes,” Pawar added. His work in this area was featured on a recent cover of JOM, the flagship journal of The Minerals, Metals & Materials Society.
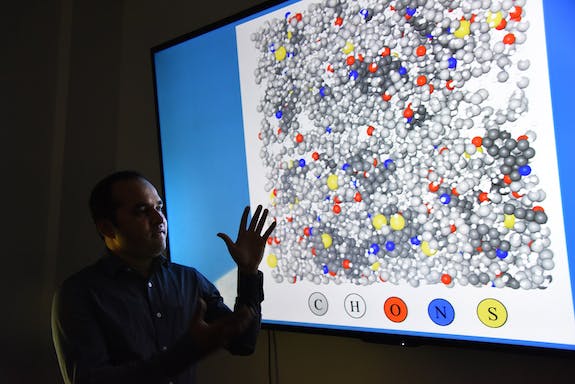
Pawar is developing models that allow highly accurate simulations of the evolution of so-called geopolymers. Like all polymers, they are composed of small units, or monomers. These basic units can link together in a variety of ways, and different arrangements can result in polymers with very different properties.
Polymeric materials are the backbone of many industries. Rechargeable batteries, for example, depend upon polymers to safely function and perform as desired, and so, too, do fuel cells. Polymers are found in filters and are an essential aspect of biofuel manufacturing and hydrocarbon extraction.
The last class of materials is geopolymers. What starts as animal and plant life is transformed by pressure and heat over millions of years. Along the way, it becomes a waxy material known as kerogen, which is found in oil shales around the world. With more heat, pressure and time, kerogen then evolves into liquid and gaseous hydrocarbons.
This is a complex process with many different possible paths. As a result, petroleum and kerogen in one place differ from that in another.
Among other things, Pawar’s research aims to reveal the reasons behind these differences. “We are developing these advanced models so you can get some initial insight,” he said.
One challenge with geopolymers is that researchers have only a final product as a validation point for the model. They don’t have starting conditions or all the details of the transformation. So, they must make assumptions about the starting point and intervening conditions, with the model then suggesting how the geopolymer changed over time.
Another challenge is that a highly accurate model requires extensive computer resources. The computer does many calculations repeatedly, simulating how what started as organic matter converts into a hydrocarbon. Doing this with high fidelity demands that these calculations be made at many points in time and space. That can be computationally intensive. So, researchers may do an initial assessment at a lesser accuracy, using these results to select likely starting points and intervening environments from among many possibilities. They will then repeat the simulation, using a finer mesh of points in space and smaller steps in time to achieve greater accuracy.
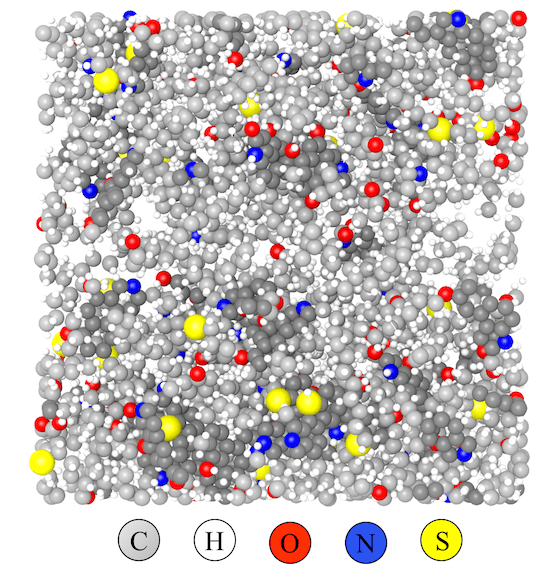
Following this general approach, Pawar has had some success, with the models enabling characterization of geopolymers. The simulations have also provided insights into the geological processes.
This information could prove useful because it offers insight into the amount of heat and pressure to apply to kerogen to create valuable hydrocarbons. This essentially would be completing the work begun by nature – but at a much faster clip and in a much more controlled way. Having this capability could expand possible sources for fuels, greases and other products.
Beyond that, better polymer models could be beneficial to the manufacture of rechargeable batteries, fuel cells, membranes to filter water and other liquids, biofuels, and other products used in a variety of industries. When making a polymer, manufacturers can change the properties of the final product, but it may not be clear what is best among a range of outcomes.
For example, turning saltwater into freshwater can be done by forcing it through a polymeric membrane that is constructed so that only water gets through, and unwanted components, like salt, do not. It may be easier and less expensive to make one polymer compared with another. However, the first could require more energy than the second to force water through, increasing operational cost. So, it may be better in the long run to produce the second or even a totally different polymer.
Picking the best formulation among many possible ones involves satisfying a range of constraints. An accurate model can help a polymeric product achieve an ideal balance of properties, which is important.
“You need to make sure the polymer falls within cost, safety and performance parameters,” he said. “Everything should fall within specific limits.”