When it came to finding third-party validation, Hydrocore, a company seeking to build a high-temperature furnace that turns municipal waste into energy and marketable byproducts, went back to its roots.
Founded in 2010, the company holds patents to electric arc furnace technology developed in the early ’90s at Idaho National Laboratory. The furnace can effectively burn municipal waste to make electricity via a steam generator, similar to how coal- or gas-fired plants operate. Unlike traditional plants, however, the furnace can break down unsorted trash into its molecular components, which can then be made into transportation fuels or other products. By effectively recycling trash to make marketable materials, the process could reduce consumption of raw materials, which saves energy.
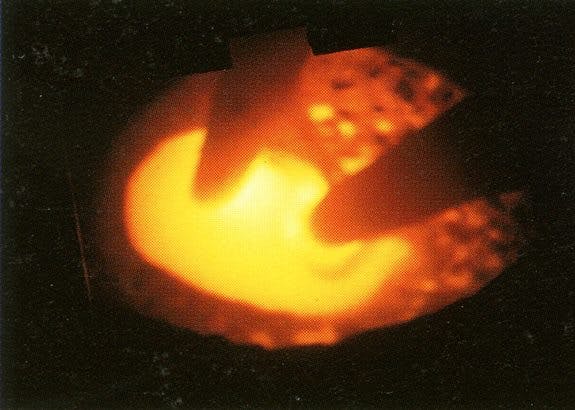
In preparation for a demonstration project in Sevier County, Tennessee, Hydrocore turned to INL and its Technical Assistance Program for scientific validation of the processes it intends to use. The TAP program exists to help small businesses by providing scientific and engineering expertise not readily available in the private sector.
“The TAP program provides up to 40 hours of technical assistance to small technology-based businesses in the areas of nuclear energy, other energy solutions or national security,” said Stephanie Cook, who leads INL’s technology-based economic development activities. “It’s always fun to see the big impact from TAP projects helping small businesses prepare their technology for market launch.”
There were more deeply rooted reasons for seeking INL expertise as well. Hydrocore’s chief technical officer, Tom Eddy, was technical leader of INL’s plasma processing team in 1988, researching and testing various methods to convert hazardous materials into a glasslike waste form. In the early ’90s he left the lab to form a company called MeltTran, which built a prototype melter in Idaho Falls and a demonstration model in South Korea.
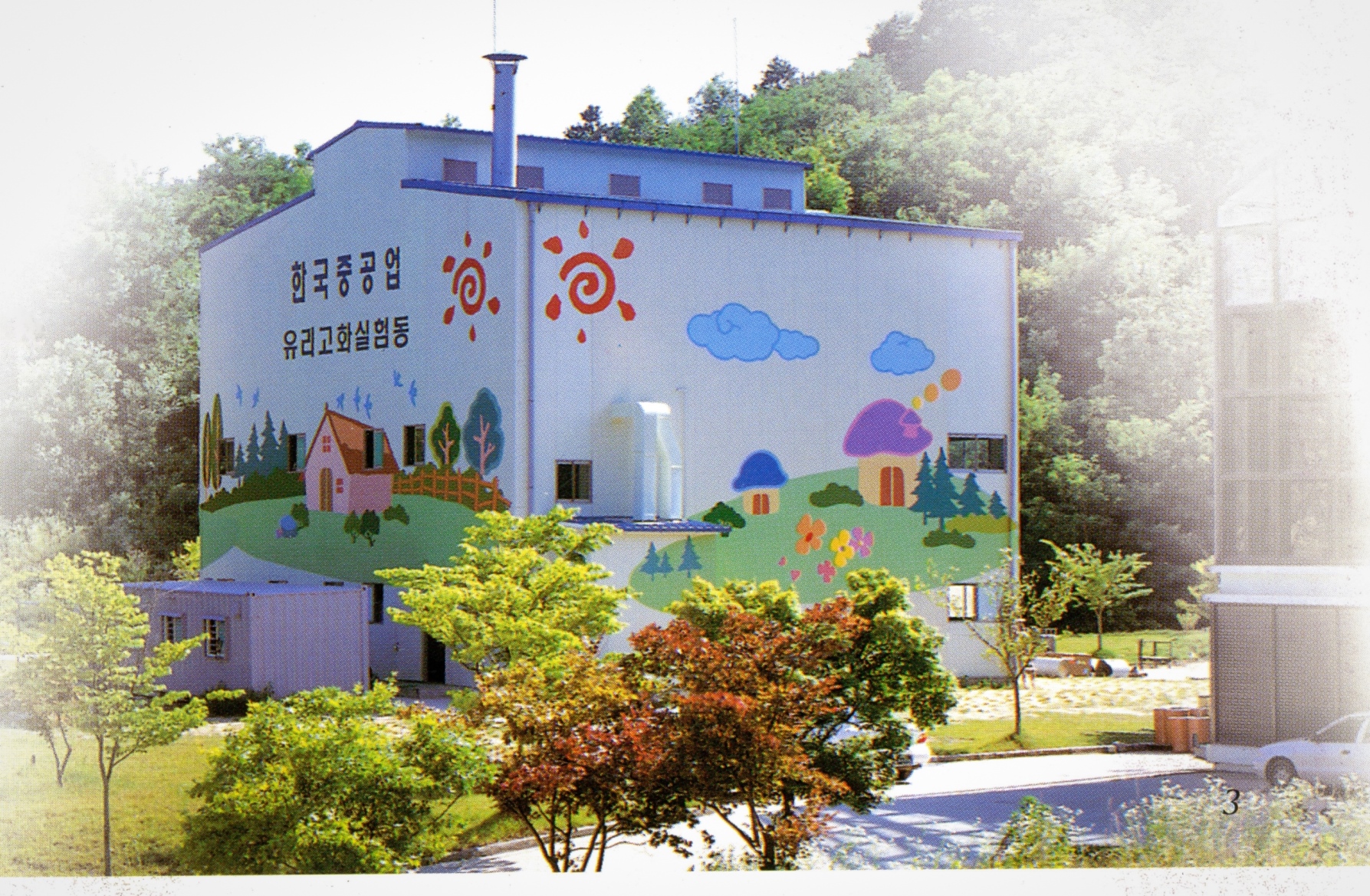
MeltTran folded after 10 years because it could not find the funding to build a full-sized plant in the United States, Eddy said. Yet the technology attracted the attention of John Mark Bardsfield, Hydrocore’s CEO, who had conducted independent research in energy technologies at University of Tennessee and Oak Ridge National Laboratory.
He and Eddy teamed up and enlisted INL to help evaluate the prospects for a U.S. demonstration.
The Misty Mountain demonstration project would use Hydrocore’s submerged electric arc furnace to heat municipal waste to temperatures approaching 1,700 degrees Celsius. Such temperatures can break the molecular bonds that hold atoms together, separating complex wastes into several classes of products. First, pure metals (mainly iron and aluminum) could be recovered. Second, a liquid that cools into a product they call “glasalt” could be used to make tiles or roadbed material. Finally, a simple synthetic gas (“syngas”) could be refined into diesel or jet fuel.
Eddy said the most important aspect of the technical assistance provided by INL is validation of the gasification process, which would use a series of chemical reactions called the Fischer-Tropsch process to refine syngas from the incinerator. In all, Hydrocore received 40 hours of technical assistance estimated to be worth near $10,000. The company wanted a review of the project and confirmation of Eddy’s calculations.
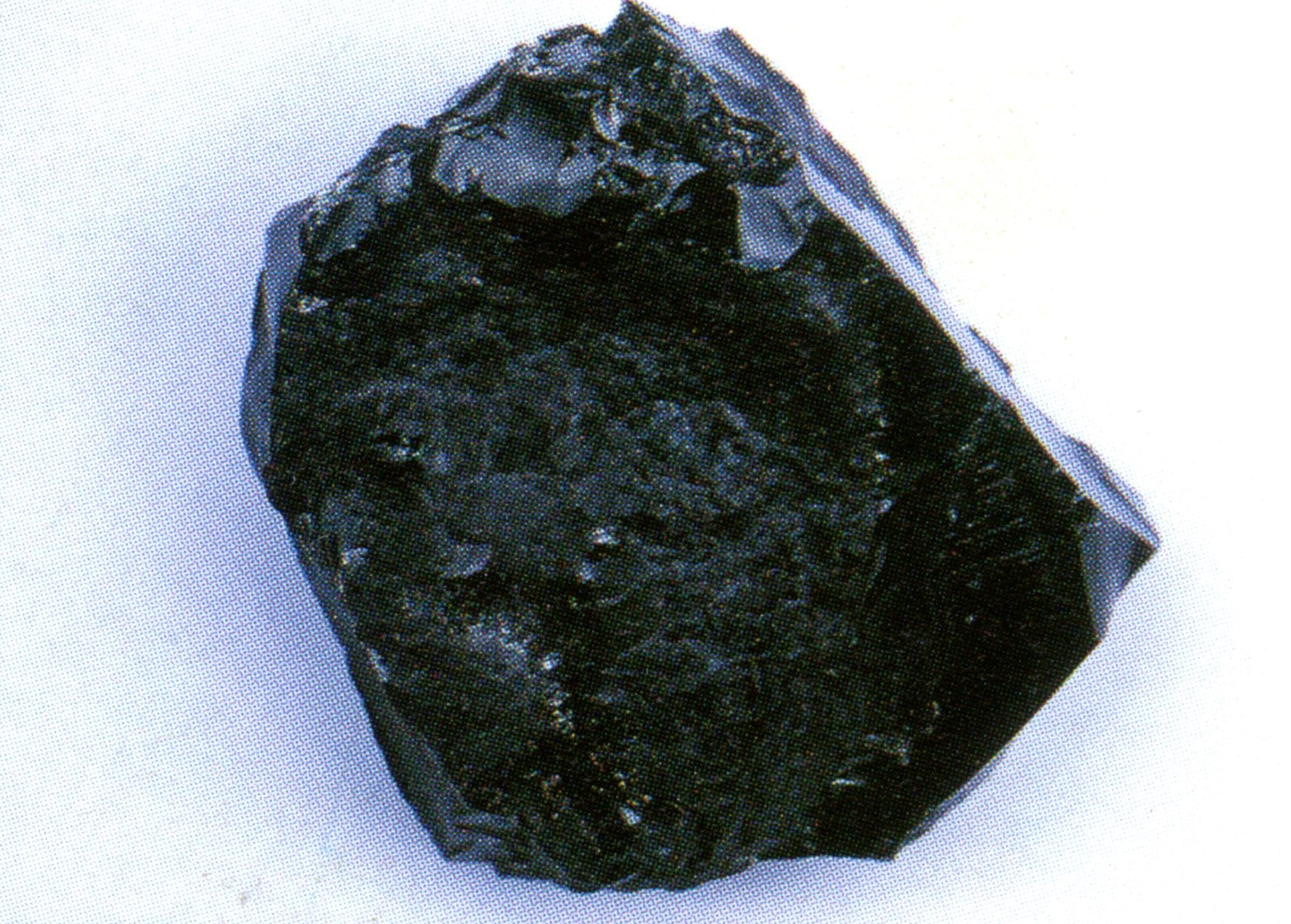
The concept also is of interest to INL because its excess heat can be used to generate electricity, said Nick Soelberg, one of the INL researchers who evaluated the project. This makes it a serious alternative to fossil fuel-fired power plants, reducing greenhouse gas emissions.
Aside from the prospect of making electricity from trash, the furnace’s ability to consume anything — toxic waste, ash and tires, sludge and wastewater, landfill waste — without any sorting is also intriguing.
The Misty Mountain project is designed to handle 500 tons of municipal waste daily, and can generate a net excess 3.8 megawatts of electricity. “There’s quite a lot of revenue in there,” Eddy said.
The proposed plant in Tennessee — estimated to cost $77 million — has all the permits ready. The challenge now is finding investors. “If we can get a small one built, we can prove the validity,” Eddy said.