A collaborative effort between startup Starfire Energy and scientists at Idaho National Laboratory (INL) may lead to a new way to store energy from the wind, sun, or elsewhere. If the basic research and development underway pans out, there could be thousands of modular systems that convert carbon-free power sustainably into ammonia, or NH3.
If that happens, it’ll be, in part, because of the Department of Energy’s Advanced Manufacturing Office and the American Institute of Chemical Engineers’ RAPID Manufacturing Institute. They run programs that bring industry and national labs together, and the Starfire/INL cooperation is one result.
For the work with ammonia, INL’s contribution is a tool and technique to analyze chemical reactions more thoroughly and accurately than possible before. “It’s basically a unique instrument that provides us with this microkinetic data,” said Rebecca Fushimi, senior research scientist. “The microkinetic data really says how and why one material is different than another.”
Called the Temporal Analysis of Products, or TAP, reactor system, the instrument reveals what happens when chemicals and compounds interact, such as when a catalyst makes a reaction happen faster or easier. Among other things, INL has used the TAP system to analyze how ammonia decomposes.
A tool that leads to greater insight into how something comes apart can also be used to improve understanding about how to put it together. That second part, the production of ammonia, is of interest to Starfire Energy of Aurora, Colorado. The company’s goal is to make sustainable energy a reality. And the vehicle of choice to accomplish this? Ammonia.
“Our target is to use the ammonia as a fuel for energy storage and transportation and similar things,” said Joe Beach, president.
Ammonia has several advantages, he added. Chief among them is higher energy density, 1.8 times that of liquid hydrogen and ninefold that of lithium-ion batteries. Ammonia is also easier to store, as well as being cheaper to transport, than liquid hydrogen. One reason for these pluses is that ammonia is a liquid at a higher temperature and a lower pressure than hydrogen, which means storage tanks can be lighter and less bulky.
What is needed for sustainable production of this fuel is a way to make it without carbon emissions. Today, ammonia is produced with fossil fuels, which means two tons of carbon dioxide emitted for every ton of ammonia generated.
Starfire’s solution makes ammonia from water, which supplies the hydrogen, and air, which provides the nitrogen. Using a catalyst-driven process, the company’s reactors operate at a lower temperature than is the industry standard. They can follow the variable output from solar plants or wind farms, an approach that means the ammonia can be made using carbon-free power when it is most cost-effective.
Importantly, Starfire’s systems can be modular, Beach said. This lowers their cost and makes it easier to scale up the size of an installation as demand grows. Getting bigger would just mean adding modules. It also helps Starfire because the company will, it’s hoped, be making thousands of identical modules. That mass production will lead to a steady decline in the cost of module manufacturing, which, in turn, will help the product reach an even larger market.
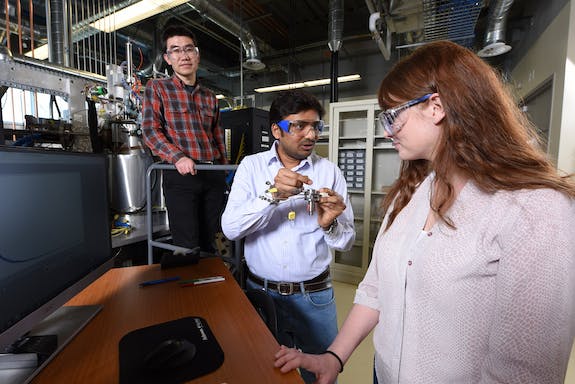
At least, that’s Starfire’s plan. The foundation for it all, though, is the ammonia production process, and at the heart of that is a catalyst-aided chemical reaction. So, Starfire is working with Fushimi’s group at INL to better understand how the catalyst works. The investigation, which has just started, could also possibly provide clues to Starfire about how the catalyst could be made more efficient, less costly, able to work at a lower pressure or temperature, or otherwise better.
Even a small boost to catalyst performance could be important for the economics of the entire project. This would be particularly true as production ramps up.
“It could be a big deal at a larger scale,” Beach said of any improvement.
The collaboration between Starfire and INL is precompetitive, basic research and development. Tweaking and enhancement of the catalyst will be done solely by Starfire.
As for how the company and national laboratory got together, that happened after Beach attended an online TAP reactor overview that INL’s Fushimi presented to educate RAPID and its members about INL capabilities. Fushimi and Beach also participated in a technology showcase panel discussion at a RAPID member meeting in spring 2019.
“It sounded like something that could be interesting and useful for us,” Beach recalled.
Subsequent meetings led to the collaborative effort, under the Technical Assistance Program. Every year, INL’s Technical Assistance Program offers up to 40 hours of expertise each to about a dozen small businesses that overlap the lab’s mission areas. The assistance is available only when comparable expertise cannot be found in the region. Coincidentally, the program has the same acronym, TAP, as the system being used to conduct the basic science.
For the INL team, which had proven the analysis tool worked using a simple chemical process, the prospect of using the technique on a complex reaction with a catalyst was intriguing. “It’s exciting to apply these methods to real materials,” Fushimi said.
Pinpointing why one material differs from another in a chemical reaction could be very important information, she said. “It should be able to accelerate the development process.”