In October 2020, the Department of Energy announced FuelCell Energy of Danbury, Connecticut, and Idaho National Laboratory would receive $12.5 million for a project integrating hydrogen production and nuclear power. As a result of these related projects, widespread deployment of clean hydrogen production could be many steps closer to reality. The looming rollout of such technology could benefit strategic industries and the environment.
Hydrogen will play a vital role to help decarbonize the steel, agriculture, petroleum refining industries, and eventually synthetic fossil-free hydrocarbon production. It can serve as a clean fuel for combustion devices, fuel cells, utility-scale power generation, and vehicles ranging from warehouse forklifts to heavy duty trucks. The U.S. makes about 10 million metric tons of hydrogen annually. The world produces about six times that — most of it using a process known as steam reforming from natural gas.
With steam reforming, every ton of hydrogen produced generates at least 5.5 tons of the greenhouse gas carbon dioxide, aka CO2. According to the Environmental Protection Agency, the average car emits about 4.6 metric tons of carbon dioxide a year. So, current U.S. hydrogen production is about the same in terms of climate altering CO2 emissions as having more than 10 million cars on the road.
What is clean hydrogen?
Those emissions can be reduced to almost nothing, though, by using electrolysis, which makes hydrogen out of water and electricity. If electrolysis is performed with a carbon-free power source like a nuclear plant, large quantities of what is called clean hydrogen can be made without emitting any CO2 at all. It would be as if the CO2 emissions of tens of millions of cars vanished.
“We want to produce clean hydrogen,” said Richard Boardman, INL lead for integrated energy systems technology development, in discussing the FuelCell Energy and INL project, funded by DOE’s Nuclear Energy and Hydrogen and Fuel Cell Technologies offices. “We also want to preserve the nuclear industry.”
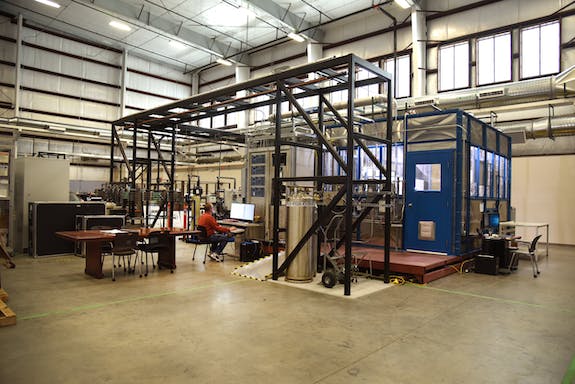
The two goals are related. Thanks to technology advances and taxpayer subsidies, solar and wind are increasingly two of the cheapest sources of electricity. There are times, though, when the sun doesn’t shine, and the wind doesn’t blow. So, there must be baseline sources — power plants that produce a steady stream of electricity.
Nuclear power plants can do that without emitting carbon dioxide. Typically, they run most efficiently and cost-effectively when generating a constant amount of power.
Enter clean hydrogen. That industrially and environmentally important commodity can be made using the electricity and heat that nuclear plants produce. Clean hydrogen generation will happen when the price of electricity is low, especially when there is excess renewable energy production. When the grid is challenged by high demand — or when renewable capacity is down due to gray skies or still air — the nuclear plants can provide more power to the grid by diverting electricity away from clean hydrogen production.
Today most commercially produced hydrogen comes from steam methane reforming, a process that uses steam to break apart the methane molecules in natural gas. This method creates at least 5.5 tons and as many as 9.0 tons of CO2 for every ton of hydrogen produced, with variation due to how much carbon dioxide is released from producing the heat and power needed by the process. Steam reforming is popular because it is often the least costly way to make hydrogen.
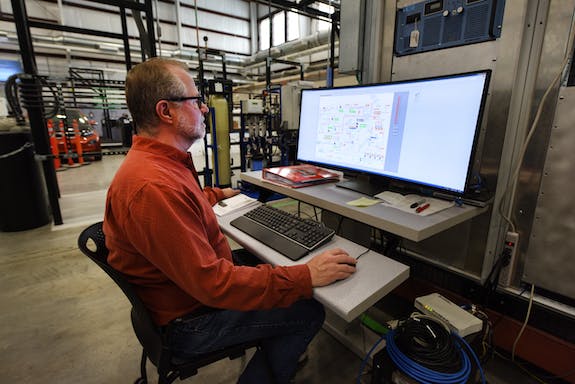
The electrolysis approach generates clean hydrogen by splitting apart water molecules (H2O). The energy for the process can come from a nuclear plant or another carbon-free source. In addition to electricity, nuclear plants can supply high-temperature steam. Heat and electricity are two ingredients needed for high-temperature electrolysis, which can be an especially efficient way to get hydrogen out of water.
To be adopted on a wide scale, however, the cost of high-temperature electrolysis must be competitive with that of steam methane reforming and free of technical risk. The new FuelCell Energy and INL demonstration project aims to address both hurdles. FuelCell Energy will design and manufacture a ready-to-go modular solid oxide electrolysis cell that produces hydrogen. INL will test the module and confirm it works as it should.
“We are working with FuelCell Energy to reduce the technical risk,” Boardman noted of INL’s objective check of the technology’s performance.
Getting ready to ramp up
As for the cost, solid oxide electrolysis cells generate hydrogen in a much more energy-efficient way than other technologies. “These solid oxide cells support electrolysis at a much higher efficiency than low-temperature electrolysis cells,” said Tony Leo, FuelCell Energy’s chief technology officer.
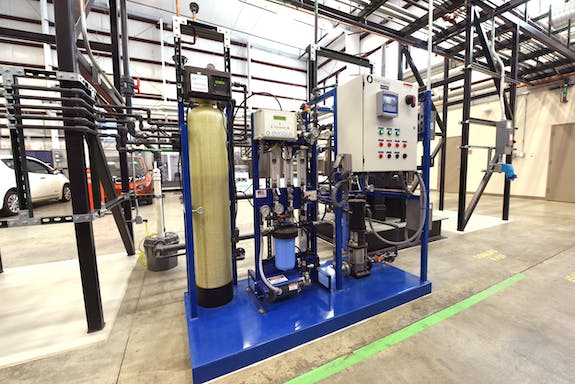
“Low-temperature electrolysis produces hydrogen with 60 to 70% electrical efficiency. This solid oxide electrolysis has an electrical efficiency as high as 92 percent,” he said. Getting more hydrogen out for every kilowatt in lowers the cost of the hydrogen that is produced.
The FuelCell Energy system will be sized to consume 250 kilowatts of electricity. Its modular design will make it possible to generate more hydrogen by simply installing more units. Nuclear plant operators can decide how many modules they want at first, then add modules as desired. Leo noted that large scale use at nuclear plants will require larger modules than the demonstration system, which is a good size for smaller commercial or industrial applications.
During testing at INL, the FuelCell Energy electrolysis module will undergo a real-world emulation of grid dynamics, thermal energy transport from a nuclear reactor, and a nuclear reactor control simulator.
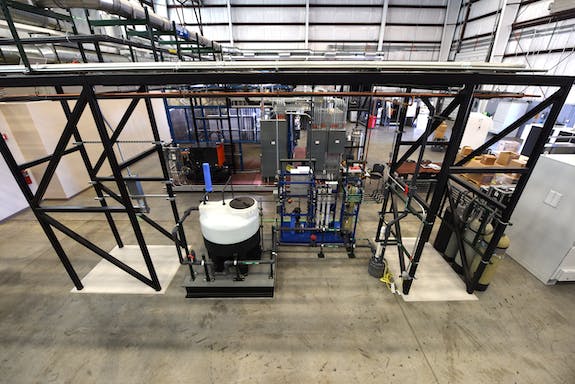
This project, INL’s Boardman said, builds upon earlier investigations done using computer modeling of solid oxide cell electrolysis. These simulations indicated that the approach was technically feasible and could have a substantial economic and CO2 reduction payoff.
There also could be market growth with the advent of cost competitive clean hydrogen. For instance, in addition to current industrial applications, hydrogen can be used as a carbon-free fuel in cars, trucks and other vehicles.
With the success of the FuelCell Energy/INL project and others planned, what has been a mere proposal to produce clean hydrogen is on the way to becoming a reality. When asked about the outcome of this project, Boardman predicted, “FuelCell Energy really should start to be able to look at commercial scale-up.”