How do you simultaneously modernize several power plants that all have unique characteristics, are highly regulated, produce mountains of data that’s typically drawn from multiple distinctive analog plant systems and not uniformly organized, and operate on razor-thin margins?
In short, you combine technological advancements with human cooperation, executed by a really smart team with a passion for improvement.
That’s the essence of the Advanced Remote Monitoring (ARM) project undertaken by the Utilities Service Alliance, Inc. (USA) and Idaho National Laboratory, under the Department of Energy’s U.S. Industry Opportunities for Advanced Nuclear Technology Development program. DOE is investing more than $9 million in the effort, while USA will contribute more than $4 million over three years.
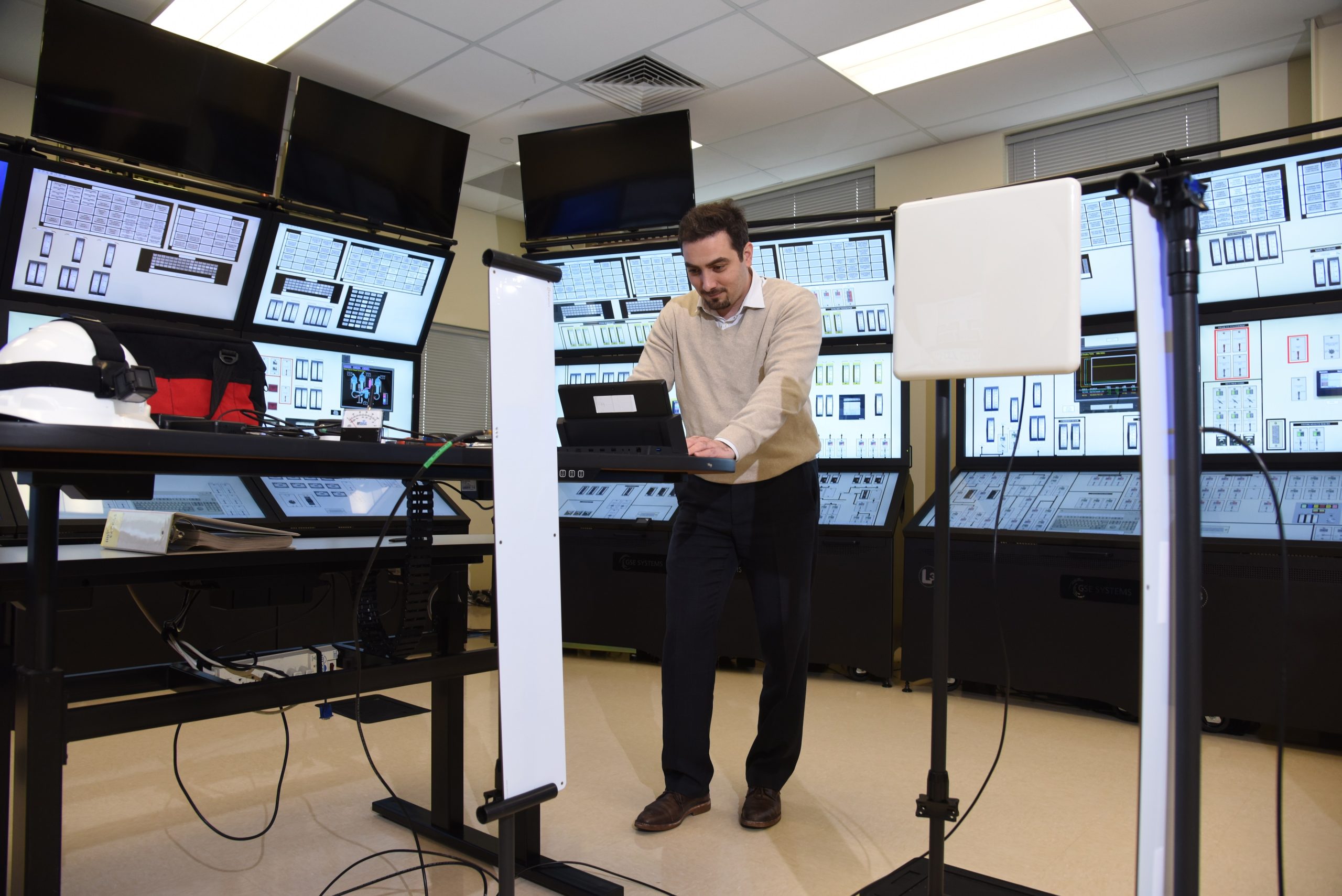
“Huge amounts of data exist in a nuclear power plant,” explained Ahmad Al Rashdan, Light Water Reactor Sustainability (LWRS) Program senior research and development scientist at INL. “You can use it to automate manual activities. It can improve performance. It can also allow operators to predict plant issues or equipment failure way ahead of time. You can plan for failures and use this knowledge to optimize plant work activities and reduce operating cost.”
The nation’s current nuclear power reactor fleet was built on processes and technologies from several years ago, said Clint Carter, who ran Luminant’s groundbreaking Power Optimization Center and is now a loaned executive to USA in charge of Fleet Modernization. “Meanwhile, contemporary technologies are providing opportunities to automate data collection, analytics and reporting, and help us automate our traditional business processes in a way to improve their efficiencies – all while preserving nuclear safety.”
John Christensen, USA’s president and CEO, credits Luminant and Carter for laying the groundwork. “They’re as experienced with applying this type of technology as any nuclear operator in the world, and they’ve worked a lot of the bugs out,” he said. In particular, Luminant used this general approach to problem-solving at its generating plants over the last 15 years, including its one nuclear station, Comanche Peak in Texas. “We’re primarily single-unit operators – we aren’t part of a large nuclear fleet,” Christensen said of USA, a nonprofit membership organization based in Kansas.
One of USA’s strengths is examining a complicated challenge and developing a systematic approach to tackling it. “We started by selecting pilot programs from the industry Efficiency Bulletin document list, selecting items identified as easy, medium, and hard to implement,” he said. Under Carter’s direction, USA has assembled a 10-person team from across its membership to work with scientists and professionals at INL for three years focusing on four stations, along with Luminant’s Power Optimization Center:
- Talen Energy’s Susquehanna Station, Pennsylvania
- Xcel Energy’s Monticello Plant and Prairie Island Plant, Minnesota
- Energy Northwest’s Columbia Station, Washington
- Luminant’s Comanche Peak Nuclear Power Plant, Texas
While those stations will be the first to reap the benefits – and to go through the process of working the bugs out – Christensen stressed the learnings will be deployed across USA’s membership. INL will analyze and develop the technologies to collect and analyze plant data and share the experience and outcome of the effort with the nation’s nuclear power fleet.
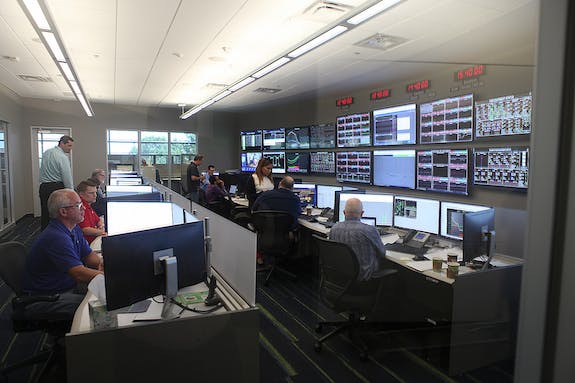
Examples of factors being examined abound, with one being thermal performance. “Nuclear power plant operators know they’re losing energy or revenue because of thermal losses. This loss can be tracked and reduced,” Al Rashdan said. Another area of focus is the process of facility workers doing their rounds. “The operator has to walk around, visually monitor plant activities or equipment and instruments (much of it analog instruments), and report back,” he said. “It’s a significant amount of time.”
Also in the equation is finding an array of sound, safe ways to cut costs and thus ensure the nuclear generators are competitive – and continue running. Of course, automation can be accompanied by staff reductions, and the USA-INL team is keenly attuned to having the ARM project be part of a smooth transition as large numbers of employees in this sector near retirement.
“It’s far better for people to retire through normal means than for a plant to shut down and everyone loses their jobs all at once,” Christensen said.
And a good way to do that “is to look at all the data they already have in their plants, optimize their operations using this data, and perhaps save millions of dollars a year,” Al Rashdan noted.
“I am firmly convinced that nuclear power can compete head-to-head with any other electric generating source through the application of advanced technologies,” said Carter. “We owe it to our nation and to future generations to preserve this most phenomenal source of safe, clean and reliable energy.”
Read more about DOE’s Light Water Reactor Sustainability Program: https://lwrs.inl.gov/SitePages/Home.aspx