The Advanced Test Reactor at Idaho National Laboratory is the world’s most powerful and flexible test reactor. It is designed to study the effects of intense irradiation on materials. Since the reactor began operation in 1967, ATR has provided test capabilities for the U.S. Navy’s nuclear-powered vessels and the nation’s commercial nuclear power industry. Since 2008, it has welcomed researchers from industry and academia to propose experiments to be run in its one-of-a-kind core.
The reactor’s unique serpentine core design allows for multiple experiments to run simultaneously under different conditions and power levels. Its low operating temperature and pressure exempt it from much of the wear and tear that commercial reactor vessels endure, but high neutron radiation levels cause some of its core components to get brittle.
Maintaining peak performance by replacing reactor internals
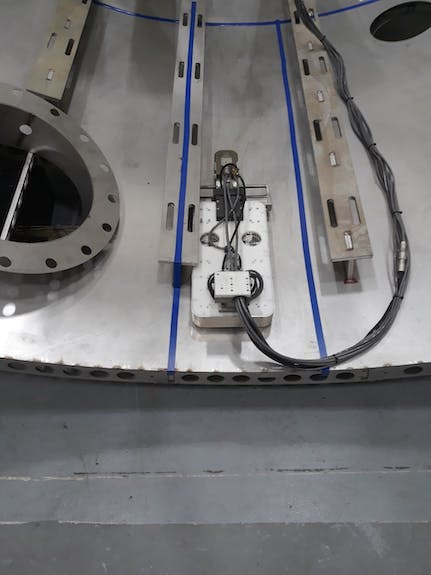
To keep the reactor’s innards in tiptop shape, the facility performs a core internals changeout (CIC) – essentially a major overhaul – every 10 to 15 years to renew the reactor’s internal core components. Think of it like a classic sports car that is immaculately maintained for more than 50 years and gets its engine rebuilt every decade or so to maintain peak performance.
The U.S. Department of Energy has committed to keeping ATR in operation through at least 2040. Evaluations will be conducted between now and then on the options for maintaining ATR operations beyond 2040 as well as options for a possible replacement for it. One thing for certain is that the demand for the testing and research capabilities it provides is expected to continue for decades, at least through 2085.
Since ATR began operation in 1967, there have been five of these major overhauls, with the next one scheduled to begin in April 2021. This one will be different, however.
Preparation is key for extended outage success
Extended changeout outages like the one planned for 2021 provide valuable opportunities for INL to do in-service inspections on major plant components and infrastructure to determine the reactor’s fitness for continued reliable operation.
Working with IIA Nuclear Services, a San Antonio-based subsidiary of Industrial Inspection & Analysis, ATR’s Vessel Inspection Team is preparing to let loose in November a device they have nicknamed the “Swimmer,” a remote-controlled inspection system designed especially for ATR.
The device’s actual name is AIRIS Mk 2, and represents a new variation for IIA Nuclear Services, which has a lot of experience examining welds inside commercial nuclear reactor vessels. “ATR is a completely different world for us,” said William Jensen, the company’s project manager.
Digital inspection of stainless steel vessel welds
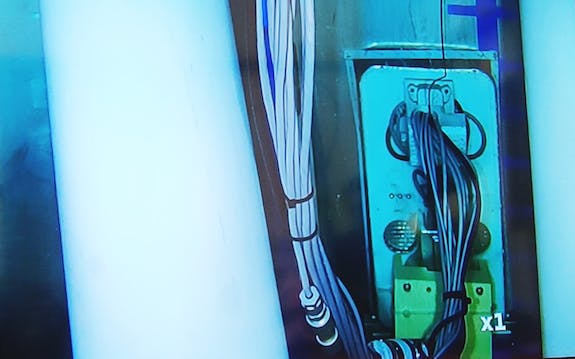
For its commercial work, IIA Nuclear Services developed the original AIRIS, a trackless underwater device 22-by-26 inches that can swim and drive along vessel surfaces under the operator’s control, and is designed to endure the extreme heat and radiation of a commercial reactor. With ATR, heat and radiation are not as much of a concern, but the components inside demanded a smaller, more nimble system. In development since mid-2018, AIRIS Mk 2 measures 24-by-10 inches and is equipped to crawl the insides of ATR’s stainless-steel reactor vessel, whose walls are much smoother than a commercial reactor’s carbon steel walls.
“ATR’s stainless-steel vessel and the uniqueness of its design require a different approach for our inspections, compared with the approach they used for the commercial fleet,” said Heath Buckland, program manager for ATR’s Strategic Thermal Irradiation Capabilities division.
The reactor vessel’s condition has been visually assessed during past outages and core internals changeouts, but not to any current code standard. The radiographs taken for original fabrication acceptance have deteriorated and can no longer be relied upon as a catalog of fabrication flaws. IIA Nuclear Services’ examination, followed by one done by Framatome during the changeout in 2021, are intended to provide an inspection baseline that can be used to compare future vessel weld examinations.
Inspecting the vessel top head
While IIA’s “Swimmer” inspection will be done underwater inside the reactor vessel, Framatome’s will take place during the 2021 overhaul, when the reactor vessel top head is removed. Battelle Energy Alliance has asked Framatome to design and fabricate a new top head stand to support the top head above the floor with sufficient access underneath for laborers and inspectors in anti-contamination clothing to safely gain access. Integral to the stand design are two circular rails that support a remote vehicle to inspect the underside of the top head welds.
“ATR’s ongoing Plant Health Program is built upon constant examination of the reactor as well as its supporting systems and infrastructure,” Buckland said. “The data gathered from these vessel inspections will provide a new baseline that will help guide future decisions on reactor and plant maintenance. ATR’s capabilities are needed by our DOE and Navy customers, and these inspections ensure we can continue to support those missions.”