When it comes to generating electricity, nuclear power operators in some parts of the country today worry about ducks — or more precisely, the duck curve. The shape of the net load demand operators see looks like a duck. You can see its tail in the morning hours, a sagging belly in the afternoon, and the neck and head in the evening.
“The duck’s belly has really developed in the last five or six years,” said Idaho National Laboratory’s Bruce Hallbert.
The director of the Technical Integration Office in the Department of Energy’s Light Water Reactor Sustainability (LWRS) Program, Hallbert leads a multilaboratory team that helps the nuclear power industry develop solutions to the challenges confronting it.
In some regions of the country that are becoming predominantly solar energy-based, that’s the duck curve. In other parts of the country another dilemma has emerged. Wind energy is being added in such large amounts that net load demand challenges – similar to but sometimes even more severe and erratic than the duck curve – are developing.
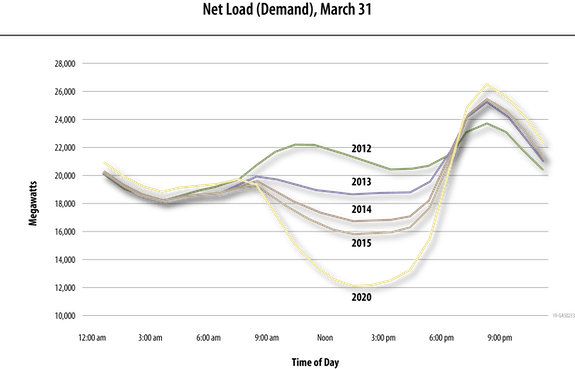
To find solutions that could help keep power reactors in business, the LWRS Program team is looking at how nuclear plants can reduce operating costs through innovation in business processes and implementation of new technology. Halbert’s group is also studying how plant operators can boost revenues by producing products in addition to electricity for the grid.
“We believe we have to come at this from both sides,” Halbert said of the two-pronged approach.
OK for 60
In the past, the LWRS Program and the industry had a different focus: longevity. Could the existing fleet of nuclear plants continue to reliably produce power for decades to come?
Some years ago, the question was of increasing importance. The U.S. Nuclear Regulatory Commission licenses commercial plants for 40 years and will permit operators to apply for a 20-year extension. Importantly, the average commission date for commercial reactors is about 1981, according to the U.S. Energy Information Administration.
Some quick math shows that the “average” plant will hit 40 in 2021. The oldest plants passed the milestone more than a decade ago and even the youngest will reach it in the 2030s.
So, starting in 2010, scientists and engineers affiliated with the LWRS Program worked with others like the Electric Power Research Institute, the U.S. Nuclear Regulatory Commission and industry to investigate key plant longevity questions: Would the components of cabling, concrete in structures, and other materials stand up to 60+ years of operation in a harsh environment? And would obsolescence of motors, controls and other components render them unusable even if there were no material failures?
A “no” to either of these questions would mean that the nuclear fleet would be forced to come up with answers or enter retirement. For the industry, then, the LWRS Program and related research efforts were critical — and, as it turned out, a success.

“We’ve been able to accomplish most of the research in these areas, especially in the materials research with our partners,” Hallbert said of the seven-year effort’s outcome. “We’ve been able to satisfactorily address most of the key uncertainties to at least know that there are no show-stopping issues.”
Thus, the industry could plan for 60-year plant operating lifetimes. But more recently, and despite confirmatory scientific information, plants started to close, with economics often cited as the reason. The shift in the situation can be understood by looking at the duck curve and understanding recent changes in electricity market conditions.
The Effect of Renewables
“It shows the penetration of renewables,” Hallbert said.
The specifics vary by grid, but a similar phenomenon occurs wherever renewable sources are strong. In the afternoon, the sun could be shining, and the wind blowing. So, if all producers are cranking out as much as they can, there is a danger of overgeneration. Since electricity can’t be effectively stored, some producers may have to be idled.
When evening comes, the sun sets, winds often calm, and the contribution of renewables falls. At about the same time, people arrive home and demand jumps. The result is a sharp rise in the need for electricity from nonrenewables. This upward surge can exceed 10,000 megawatts over the three or so hours spent moving from the bottom of the duck’s belly to the top of its head. In the case of wind, the rapid changes associated with weather fronts can lead to even more sudden power generation shifting needs.
Meeting the demand curve in these locations is only possible because there are sources that can provide power when sun and wind cannot. “The nuclear plants really help ensure the renewables can penetrate,” Halbert said.
In many ways, the appearance of the duck curve is a national success story, he noted. Renewables play an increasingly important role in electricity generation, cutting carbon emissions — and possibly the price of power.
According to a report from the International Renewable Energy Agency, by 2020 or shortly thereafter, solar and wind will generate power for as little as 3 cents per kilowatt hour. That is significantly less than 5 to 17 cents per kWh of fossil fuels. The difference is comparable to producing electricity with new natural gas power plants that exploit the historically low cost of abundant fuel produced by fracking shale formations in some regions of the United States.
However, as concerns for environmental sustainability continue to rise, power generation systems that reduce air pollutant emissions are gaining extra favor. The preference is reflected in policies that incentivize renewable energy in more parts of the country.
With this changing power production landscape, the U.S. nuclear fleet has started to move to a different mode of operation. In the past, nuclear plants were baseload suppliers, producing a steady — and typically maximum — stream of electricity. Now, the nuclear fleet is moving toward flexible operations, where the amount of electricity generated varies.
Germany, which at times gets a substantial share of its power from renewables, has operated its nuclear fleet flexibly for years. So, too, has the Columbia Generating Station, a nuclear power plant in southeastern Washington. Some plants in the Midwest have begun adjusting their total output capacity by 10 to 15 percent.
In a 2018 study published in Applied Energy, MIT researcher Jesse Jenkins and colleagues examined how a flexible approach might work in the American Southwest. They showed that throttling back on nonrenewables during the afternoon made economic and environmental sense.
Finding Solutions
The LWRS Program is helping the industry address some of its economic challenges, while INL is addressing the shift to flexibility. To minimize costs, LWRS Program experts are working with owner-operators to re-engineer business processes, research moving from analog to digital technology, and come up with ways to make labor most efficient.
For instance, nuclear plants have hundreds to thousands of valves that must be set manually to the correct position, checked by hand, and then periodically rechecked to ensure that they are at the right point. These valve checks contribute at least 10 percent to operating and maintenance costs, the bulk of expenses in a nuclear power plant. Researchers and engineers at INL came up with a way to attach a sensor to any type of valve, enabling a wireless reading of the valve position. This technology improves worker efficiency and enhances safety. It cuts human error by 90 percent, and it saves as much as a million dollars a day by shortening restarts from plant outages.
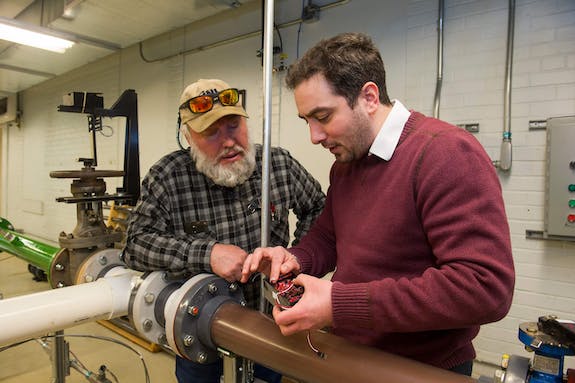
A second example is the Advanced Outage Control Center (Advanced OCC). This technology supplements the traditional approach of phone calls, face-to-face reports, and daily briefings with modern communications and information management capabilities. During a plant outage for refueling, a scheduled inspection may turn up issues that must be addressed, and the Advanced OCC provides a more efficient way to do this. A test of this technology helped shorten the time needed for repairs at an Arizona nuclear plant from 72 to 32 days, saving the operator an estimated $48 million.
A final illustration of the work done by the LWRS Program is smart document technology, which can be seen in the Electronic Instructions for Nuclear Applications (ELINA). Smart documents range from those with embedded hyperlinks to fully interactive instructions that allow workers to answer questions, record values and move on to the next step — without consulting paperwork. Along with a streamlined and electronic document review process, this technology will improve efficiency and reduce costs.
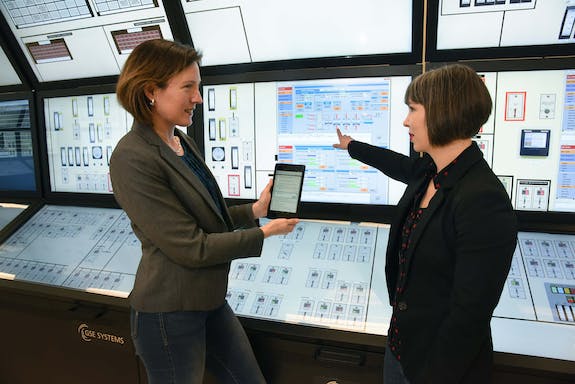
As for revenues, nuclear plants generate both electricity and heat. The latter was viewed as only good to make the former, and any excess heat was dumped into the environment. Now, industry and INL experts are considering how the heat might be used productively.
Either electricity or heat can make commodity products during those times when renewables flood the grid. For example, hydrogen used in steel production and elsewhere is typically made by cracking apart natural gas molecules. This produces hydrogen but emits all of the carbon as carbon dioxide, which is considered one of the major gases contributing to the rise in temperature of the global atmosphere.
But excess heat and electricity from a nuclear plant could be used to split water and thereby produce hydrogen, which could cut the carbon footprint of several large industrial processes that either currently use hydrogen or could use hydrogen. For example, hydrogen produced with nuclear energy could reduce the carbon emissions associated with new iron and steel production processes by more than 90 percent, Hallbert said.
Hydrogen could be immediately added to a new process that uses natural gas instead of coal or coke to reduce iron ore to briquettes that can be refined by the many electric arc furnaces built in the past 30 years in the United States.
Thus, making carbon-free hydrogen would help U.S. steel production, cut carbon emissions, and provide a revenue source. The approach would require the development of hydrogen production and storage facilities near nuclear plant sites, as well as the establishment of sales agreements and other business components. INL and other national labs are studying these variables intensely.
So, a holistic approach to beating the duck curve challenge could have far-reaching effects. What’s more, INL is playing a role in making these beneficial outcomes a reality.
“We can help nuclear power plants reduce their operating costs, what it takes to produce electricity and stay in business producing energy,” Hallbert said. “At the same time, we can increase their revenue streams, contributing to other businesses in the country that are vital to our nation’s economic competitiveness now and in the future.”
- Learn more about the LWRS program
- Learn more about the Human Systems Simulation Laboratory
- Learn more about the ELINA smart document technology