Graphite — a form of carbon found in pencil “lead” — plays an important role in next-generation nuclear technology. For instance, in high-temperature gas-cooled reactors, graphite encapsulates and encloses the fuel. Consequently, it moderates the nuclear reaction and is a structural element, ensuring reactor safety if cooling is lost.
So, as part of licensing, reactor vendors must show that the grade of graphite they’re using can take the heat — and the rest of the environment in a nuclear plant. Proving that could now be easier, thanks to a model developed at Idaho National Laboratory.
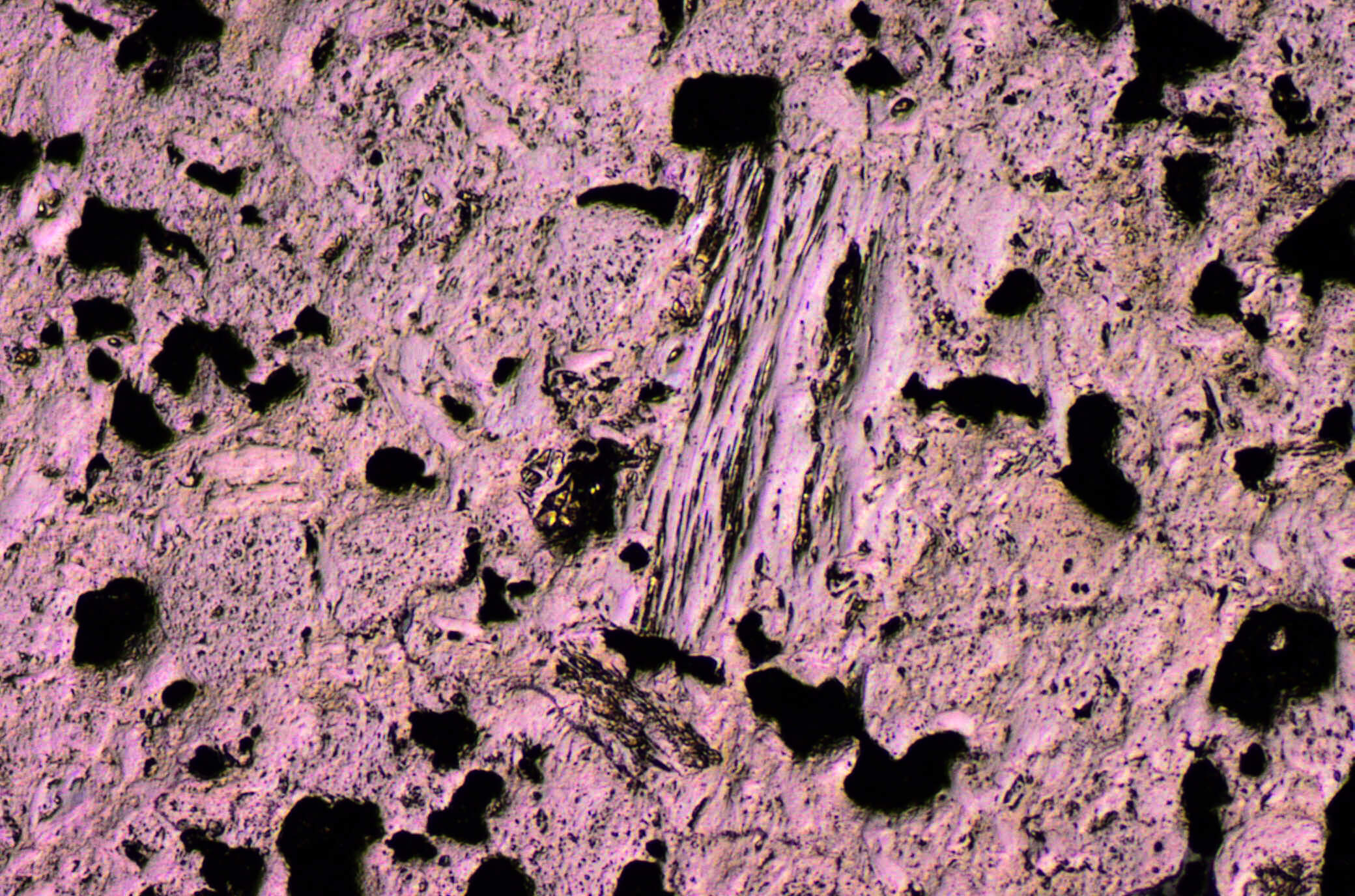
“We simply take experimental measurements of a particular grade’s microstructure, with diffusion measurements [being] one of the major experimental inputs,” said Joshua Kane, an INL research scientist who created the model with INL colleague Hai Huang. “We are then able to blindly predict the grade’s oxidation rate and depth of corrosion damage with incredible accuracy.”
A paper on this research appeared in the journal Carbon. The journal reports on significant new findings related to carbon formation, structure, properties, behaviors and technological applications.
Going with the grain
Graphite consists of sheets of carbon atoms in a honeycomb lattice, with these forming particles that may be visible only with a microscope. These microscopic features, or microstructure, cause grades of graphite to behave differently in a reactor.
“Graphite and other carbon materials are fairly unique in that the properties and performance of one ‘grade’ are in many cases incredibly different from another,” Kane said.
Graphite for nuclear applications comes in fine and medium grain grades, which refers to the characteristic size of the particles. Fine grades usually have grains smaller than about 0.125 mm, or a little larger than the diameter of a human hair. Such graphite tends to be high density, with little open space between grains.
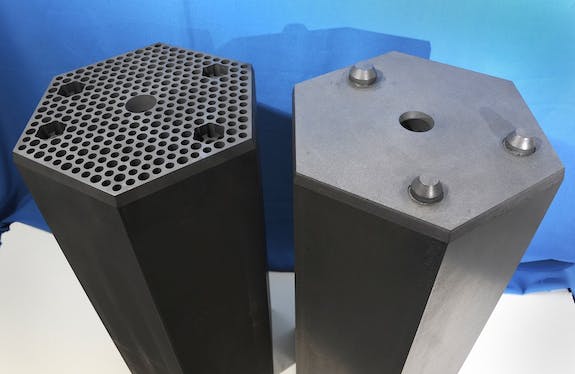
Medium grain graphite, in contrast, is made up of particles that can be up to about 1.6 mm. The density of this type of graphite tends to be lower and the spacing between grains larger than for fine grain grades.
Vendors typically pick a graphite grade based on its mechanical strength or its fit with the reactor type, according to Kane.
However, there is another important microstructure-related parameter: oxidation mass loss. When exposed to air and heat, graphite turns into a gas and vanishes. The rate at which this happens is important, as is the nature of the damage. It can be confined to the surface or it may go deep within the graphite. The rate of loss and its depth depend upon the temperature and the porosity of the graphite, which is determined by microstructure and manufacturing methods.
A better model
Testing to ensure graphite integrity despite such mass loss is time-consuming and expensive. So, the INL team devised a model that predicts oxidation effects. The scientists made simplifying assumptions about reactivity at the atomic scale and combined that with measurements on how oxygen diffuses through the graphite. They then used a computer to simulate the mass loss and compared curves of the model’s calculated outcome to experimental reality for different grades of graphite.
“I figured we would be within 10 to 20 percent,” Kane said, adding that this level of accuracy would be good for engineering calculations.
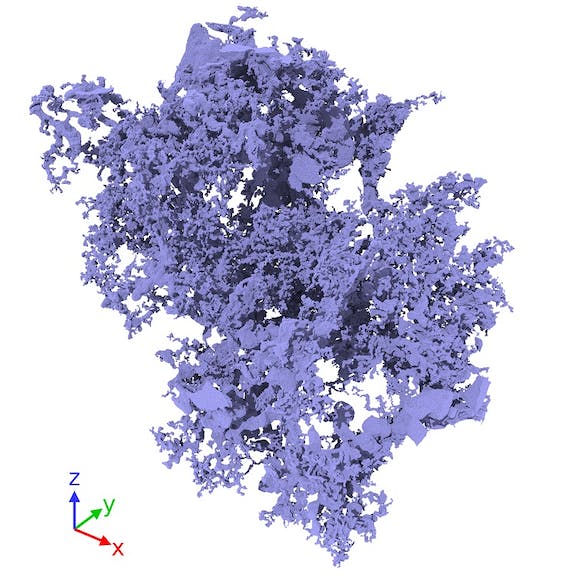
But when he looked at the various sets of curves, he was pleasantly surprised. “Our model actually performs so well that I have a hard time picking out which one is the actual model, and which one is the experimental results,” he said.
The model runs quickly, Kane noted, with a coarse simulation taking only minutes to calculate the overall mass loss rate. A fine mesh simulation might be needed, though, to obtain an accurate picture of interior damage, and that could take a day to complete. However, that is a much shorter time than running the experiments themselves.
There also is another benefit to the model. Graphite testing is typically done without taking irradiation into account. In a reactor, though, there will be radiation – which will lead to displacement of atoms over time as nuclear byproducts pass through and interact with the graphite. After many years, this could cause a microstructure change. The INL approach could predict the effects of any altered microstructure.
Simulations accounting for the impact of this, if they happen, will be done in the future. Right now, the model can still pay important dividends.
“It’s going to make qualification easier. It’s going to limit the number of experiments that vendors have to do,” Kane said in summing up the impact of this new tool.