Johanna Oxstrand and Katya Le Blanc did not set out to be innovators when they began working together at Idaho National Laboratory. Both women work for INL’s Human Factors group, which focuses on solving problems that arise from the interaction of people with technology. Specifically, Oxstrand and Le Blanc work on computer-based procedures, bringing advanced technology into existing nuclear power plants to improve safety and efficiency.
In 2012, they were tasked with bringing computer-based procedures to nuclear power plants. Traditionally, nuclear power plants have been governed by paper-based procedures, which are compiled in heavy documents that fieldworkers carry around as they perform their duties. The workers keep track of their tasks with a pen, circling the step they are on and striking through it when the step is completed. Any recorded values as well as calculations must be recorded by hand. They must also bring papers for other employees to acknowledge procedures are completed.
Some products that put electronic copies, e.g., PDFs, of the procedures onto tablets already existed, but this did little to change the overall experience of the fieldworkers. But Oxstrand and Le Blanc saw an opportunity for radical innovation in this process.
“We fought against the idea of incremental progress,” said Le Blanc.
Instead, the women sought to completely redesign the process for workers to carry out their procedures. They traveled frequently to power plants around the country to learn how workers used their procedures and to see what could be improved. As they worked through their prototypes, they kept up their busy travel schedule to get feedback from nuclear plant employees throughout the development process.
Oxstrand credits INL with supporting their extensive traveling to allow them to be physically present in the power plants, building relationships and trust with workers, thereby allowing them to develop their innovative technology.
For some time, Oxstrand and Le Blanc still did not see themselves as innovators. “There was a need that we were filling,” explained Le Blanc. “We did not think that we were innovating.”
Their extensive research resulted in the development of ELINA, or Electronic Instructions for Nuclear Applications. This product only presents information that is relevant to the task at hand. It also provides interactive instructions and provides a way for workers to route documents to people for approval without having to physically deliver paperwork.
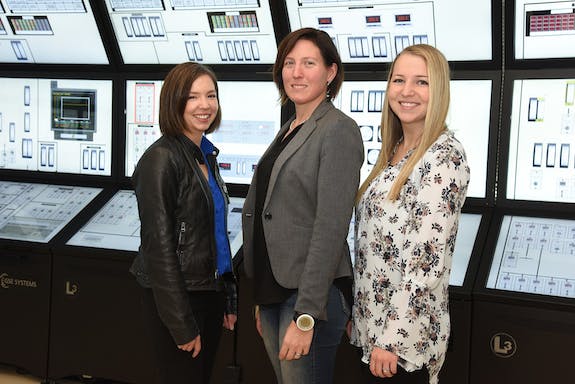
In 2017, Rachael Hill joined the ELINA team to participate in Energy I-Corps, a program sponsored by the U.S. Department of Energy aimed at assisting engineers and scientists from national labs in commercializing technologies they have developed.
Le Blanc identified the I-Corps program as “incredibly helpful” for encouraging the team to develop their technology, explain their ideas to various audiences and advertise their product to potential users.
Hill, in turn, described Oxstrand and Le Blanc as truly supportive mentors for her own success going through I-Corps. While their team does not have a formalized mentorship program, Hill finds that the informal mentorship provided by Oxstrand and Le Blanc has been vital to her experience as an INL employee. All three women credited the essential role that mentorship can have on the success of female innovators and for women in STEM generally, with Oxstrand and Le Blanc emphasizing how important it has been for them to provide that experience for Hill.
The ELINA team has received two DOE Technology Commercialization Fund (TCF) awards to mature their idea and develop it with an industry partner. They are working with an outside vendor, NextAxiom, on commercializing ELINA with a planned deployment in 2019. They are also working with Devbridge Group, a second outside vendor, to commercialize a highly dynamic work management system in 2020. The goal of both commercialization efforts is to make the ELINA technology available and accessible to the nuclear industry.
Posted Feb. 11, 2019
By Kate Meehan