Today’s high-tech devices usually contain components made of rare earth elements (REEs), a class of metallic elements including neodymium and dysprosium.
Despite this demand, and despite the fact that REEs are relatively common in the earth’s crust, REEs are difficult to obtain, and the U.S. currently does not produce a domestic supply. This scarcity of domestic REEs leaves manufacturers of everything from cellphones and computers to wind turbines and telescope lenses vulnerable to supply disruptions.
Now, researchers at Idaho National Laboratory (INL) have developed an economical way to recycle REEs using a bacterium called Gluconobacter oxydans.
Gluconobacter recovers these elements by producing organic acids such as gluconic acid that dissolve the REEs from the surrounding material and pulls them into solution in a process called “bioleaching.”
The REEs can then be precipitated from the solution and used again.
Researchers with INL’s biological and chemical processing department participated in an analysis of the expenses that would be associated with the construction and operation of a commercial-scale bioleaching plant. The analysis looked at recovering REEs from fluidized catalytic cracking catalyst, a type of material used to refine petroleum.
The findings appear in the January edition of the journal ACS Sustainable Chemistry and Engineering.
“We showed that this bioleaching process is economically feasible, and we found several routes to make the economics even better,” said Vicki Thompson, a distinguished staff engineer at INL. “It works really well when you have low amounts of rare earths. We can get value out of stuff that everybody else is giving up on.”
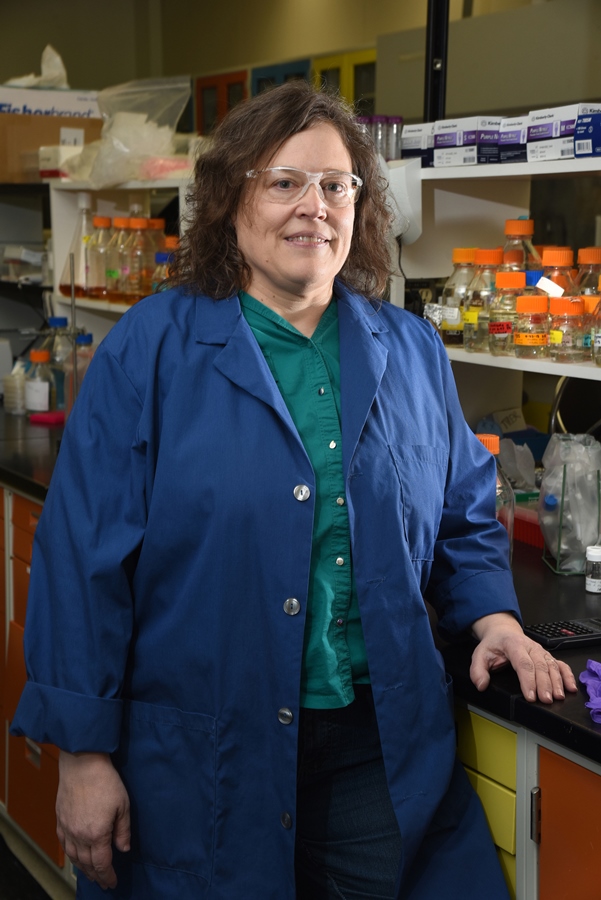
Thompson and co-author David Reed, an INL research scientist, collaborated on the bioleaching project with researchers from Lawrence Livermore National Laboratory and Purdue University.
Through the economic analysis, Thompson and Reed found that the glucose used to feed the microbes was the biggest expense associated with the process, accounting for 44 percent of the total cost. The researchers are continuing to explore other options to provide that sugar, including low cost sources such as corn stover, sugar beets or potato wastes.
A lab-scale bioreactor system designed to approximate a commercial-sized system was between 20 and 50 percent efficient.
The researchers also simulated heap leaching – where the material is placed on a liner and the chemical is added via a drip system – to mimic the type of process that would most likely occur in an industrial setting. The heap leaching process produced similar results to mixing in a bioreactor system.
Further refining the bioleaching process could improve that efficiency, resulting in greater profits, Thompson said.
Other ways to improve the economics of a hypothetical bioleaching plant are to process a material with a higher percentage of REEs, or to process a material that contains a higher value REE, said Reed.
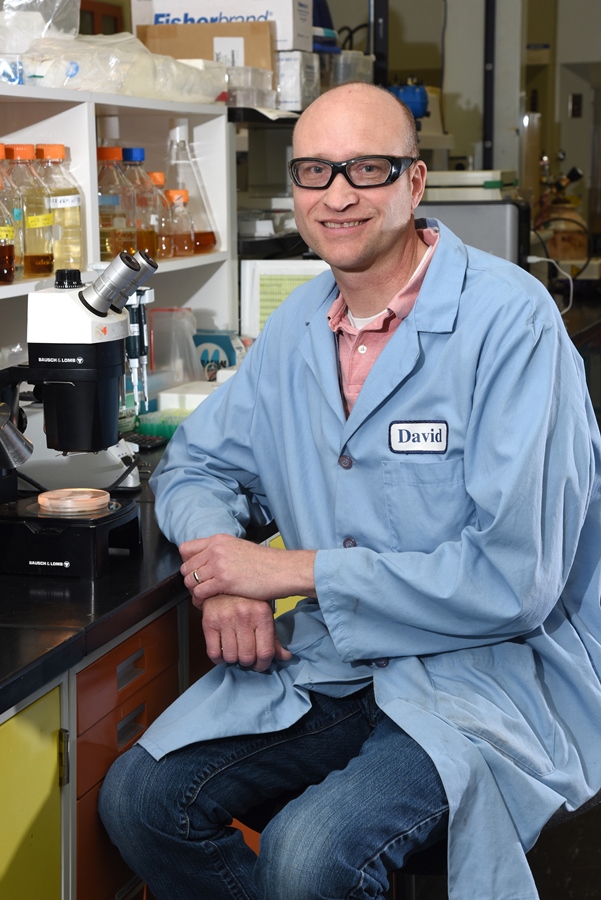
“In the cracking catalyst that we used for our analysis, 1.5 percent of the material was a rare earth element,” he said. “It could be as high as five percent. You would triple your profits because your costs don’t change, you just get more of it.”
Further, prices of different REEs vary from $2 per kilogram to $400 per kilogram. “That’s a 200-fold variation of price,” Reed said. “It just depends on the material you are looking at.”
In addition to refining the bioleaching process and finding a new source of sugar to feed the bacteria, the researchers plan to analyze the economics of different source materials including lamp phosphors, computer magnets, mine tailings and phosphogypsum – a byproduct of turning phosphate ore into fertilizer using sulfuric acid.
As part of their recent findings, Reed and Thompson also analyzed the environmental impacts of the bioleaching technique. Electricity and the glucose used to feed the bacteria had the most potential for environmental impacts.
Overall, bioleaching results in fewer environmental impacts than conventional techniques used to recover REEs, which typically involve high heat, high pressure and harsh chemicals. Bioleaching is also more economical than most conventional techniques, the analysis showed.
The research was funded through the Critical Materials Institute, a Department of Energy Energy Innovation Hub that facilitates collaborations among several national laboratories, universities and industry partners.
Read more from CMI about this project here.