Superheroes squeeze a lump of coal and turn it into a sparkling diamond – in comic books, anyway. There is some scientific validity to this fictional feat. Coal and diamonds are both composed of carbon. The two materials differ in their microscopic arrangement of atoms, and that leads to quite a difference in appearance, conductivity, hardness and other properties.
As this shows, the microstructure of carbon-based materials is important. Optimizing carbon microstructure could benefit applications in energy storage, sensors and next generation nuclear material systems.
Now a group of researchers at Idaho National Laboratory (INL) have conducted a study that could lead to improved methods to fine-tune the carbon microstructure. The scientists reported on their work in a June 2020 Materials Today Chemistry paper.
Creating crystalline structure
Kunal Mondal, an INL materials science researcher, conducted the group’s experiments, which involved subjecting tiny carbon films and fibers to temperatures as high as 3000o C (5400o F). That heat caused the microstructure in the films and fibers to become less disordered (or amorphous) and more diamondlike (or crystalline).
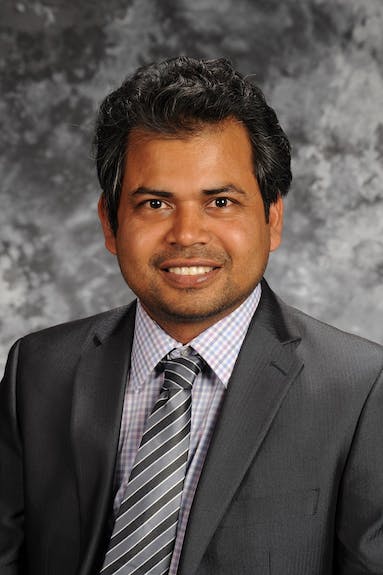
“When carbon structure gets more crystalline, it makes many things possible. First, conductivity of the carbon increases. That means you can get a lot of good applications out of it,” said Mondal, the paper’s lead author. Some of these applications include batteries and sensors, he added.
A goal of the research was to see how the final microstructure varied depending on the temperature and the starting material.
For the initial material, the researchers spun out miniature carbon fibers and coated substrates with thin carbon films. They heat treated these polymer precursors at temperatures ranging from 1000 to 3000o C. They then examined the results with transmission electron microscopes and other instruments, determining the degree of conversion from a loosely organized polymer to a more structured, crystalline arrangement.
Shortcuts in microstructure roadmap
Heat treatments are used worldwide to create carbon composite materials with the desired microstructure, which varies by application. The precursors that researchers selected are also widely used. Yet commercial production with these precursors and manufacturing methods can be an intricate process that requires a series of precise heat treatments and other actions.
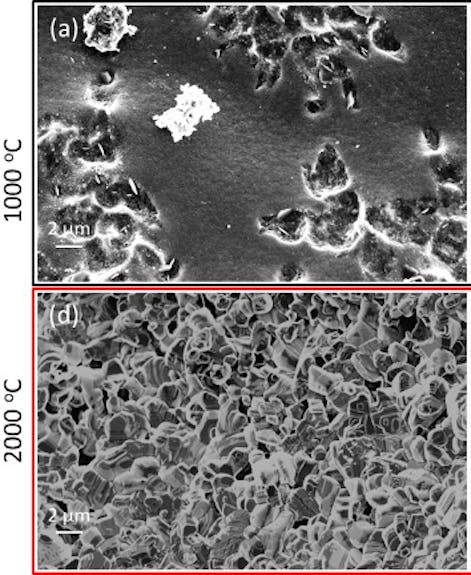
The final recipe for a product may be reached by trial and error, which can sometimes be extensive. The INL research aims, among other things, to provide a road map with shortcuts to speed up this search.
So, in addition to experimental work, the INL group also did simulations that modeled how the fibers and films would evolve during heat treatment. Gorakh Pawar, another co-author of the paper and an INL staff scientist in the Department of Material Science and Engineering, handled these simulations. The computer models predicted outcomes that were similar to the experimental results. The work was funded through INL’s Laboratory Directed Research and Development program.
The INL study provides clues that can be used to help design precursors and processes that will yield preferred nanostructures, Pawar said. For instance, starting with a film resulted in higher electron mobility than what resulted when starting from fibers, which could be a consequence of the many boundaries in a fiber and their impact on the free movement of electrons. So, for a sensor or another application where conductivity is important, starting with a film might lead to a device that is more sensitive, is faster or uses less power.
In exploring all the possible combinations of processing steps, researchers at national labs, in industry and elsewhere need to be cost-effective in their investigations and outcomes. Simulations like those done by the INL group can help minimize the time, effort and expense of zeroing in on the right process and starting material.
“You cannot run an experiment forever. You need some guidance to optimize your experimental protocol,” Pawar said.
Charging batteries faster
As for possible applications of the group’s research, he noted that getting the microstructure right is critical in, for example, a lithium-ion battery.
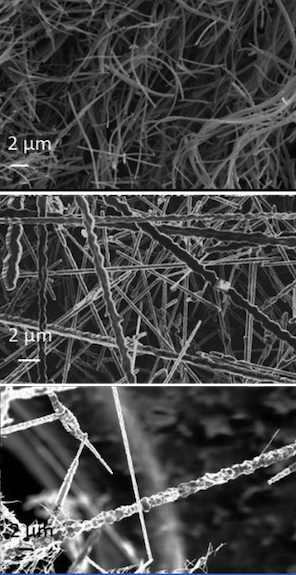
These batteries have an electrode made of graphite, a form of carbon. In operating the battery, the lithium ions are stored between layers in the graphite, which means the amount of void and defects in the material is important. With graphite of the proper structure, that movement of ions can be rapid, a requirement for extreme fast charging. Yet the graphite materials cannot be so porous that it renders the electrode useless.
Such charging might allow electric vehicles to get the equivalent of a full tank of gasoline within minutes instead of hours. That capability would make operating these emission-free cars and trucks similar to what people are used to with current gas-powered vehicles. This means the INL research project could prove beneficial in figuring out how to achieve that type of performance, a capability consumers seek.
“That’s our future goal in energy storage: how we can optimize this graphite structure,” Pawar said.
To help accomplish that, the researchers continue to expand their understanding of carbon microstructures and how they can be produced. In the end, this work may help create an electric vehicle battery that can reach full charge quickly – or, to put it in superhero terms, faster than a speeding bullet.