Biomass Feedstock National User Facility (BFNUF) researchers and industry partners have successfully tested a technology designed to address challenges to processing biomass into a feedstock suitable for coal-fired power plants.
BFNUF researchers at Idaho National Laboratory collaborated with Advanced Torrefaction Systems, LLC (ATS) to adapt an oxidation catalyst device to a state-of-the-art torrefaction pre-processing system.
Torrefaction is a process where biomass is heated to between 200 and 350 degrees Celsius in the absence of oxygen—a process similar to roasting coffee beans. The resulting torrefied material resists absorbing water, contains more energy per unit mass, combusts better, and is easier to handle and process when compared with raw biomass.
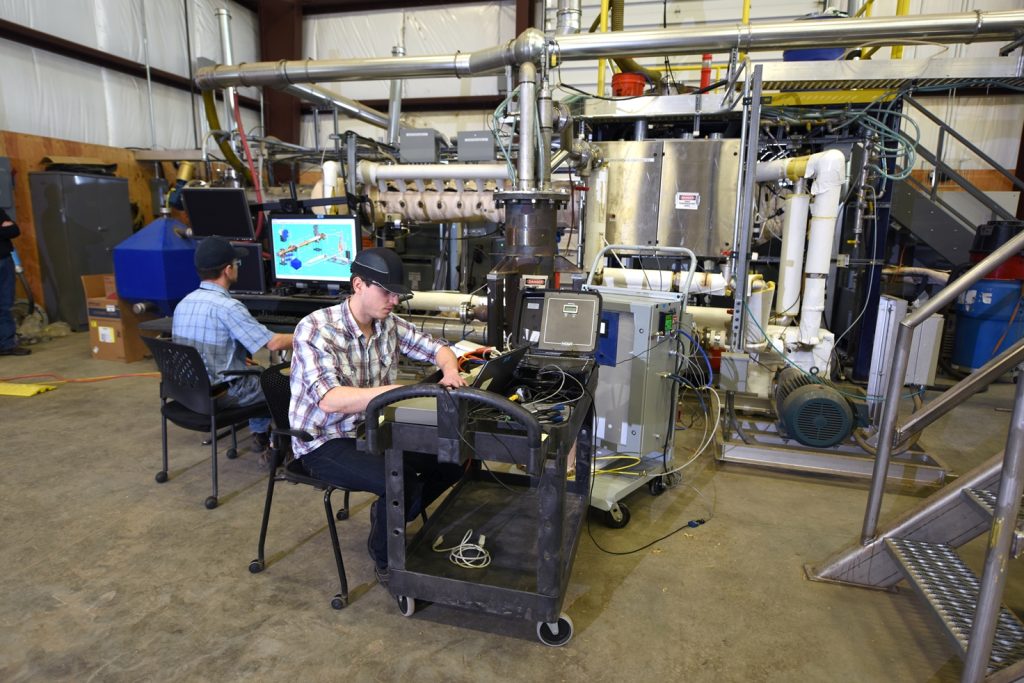
The torrefied material is similar enough to coal that it can typically replace or be co-fired with coal in coal-fired power plants. Coal plant operators can use torrefied material with minimal need for expensive equipment retrofits when compared with other options such as wood chips or white pellets. Torrefied biomass may also have applications as feedstock for gasification and other thermochemical conversion processes used to produce biofuels or chemicals.
But torrefaction has not yet lived up to its potential. Challenges—including the relatively high cost of torrefaction and potential fire and health hazards from the production of volatized gases—have largely kept the bioenergy industry from using torrefaction on a commercial scale.
Representatives of ATS say the company’s TorreCat™ Technology, which includes an oxidation catalyst similar to a catalytic converter, will help make torrefaction cleaner, safer and more cost-effective.
Catalytic converters—those oblong metal devices between the engine and the tailpipe of just about any car or truck—turn toxic automobile emissions into carbon dioxide and water. Catalytic converters are so effective that, in the United States, they’ve been required equipment on motor vehicles for more than 40 years.
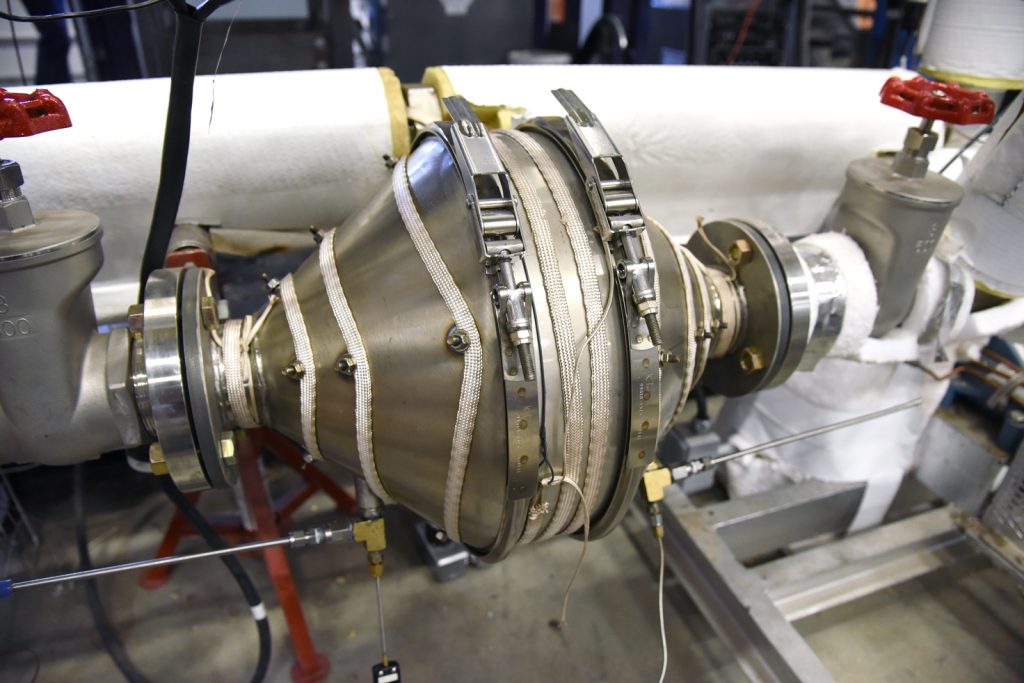
When inserted into a torrefaction system, ATS’s oxidation catalyst performs a similar function. The device combusts volatile organic chemicals produced during the torrefaction process and converts them to carbon dioxide and water. Oxidation catalysts require less oxygen and lower temperatures than combustion in a flame, making the process more efficient.
The resulting mixture of inert gases—mostly superheated steam, carbon dioxide and nitrogen gas—is then used to help heat the biomass reactor, dryers or other pre-processing equipment, cutting costs. Further, the process gas can be continuously recycled to eliminate the need for a constant supply of costly inert gas, such as nitrogen, to purge oxygen from the biomass reactor during the roasting process. Cooled inert gases can be used to reduce the torrefied biomass temperature and to provide an inert gas to avoid fire and explosion in downstream grinding and densification processes.
In February, 2016, ATS tested a version of its TorreCat™ Technology in the BFNUF torrefaction system at INL.
During two rounds of tests performed at different temperatures, toxic flue gases dropped below detection levels. Further, the inert gases from the catalyst were successfully reintroduced to the biomass reactor in a continuous loop to provide both heat and a high-volume purge gas with low oxygen content.
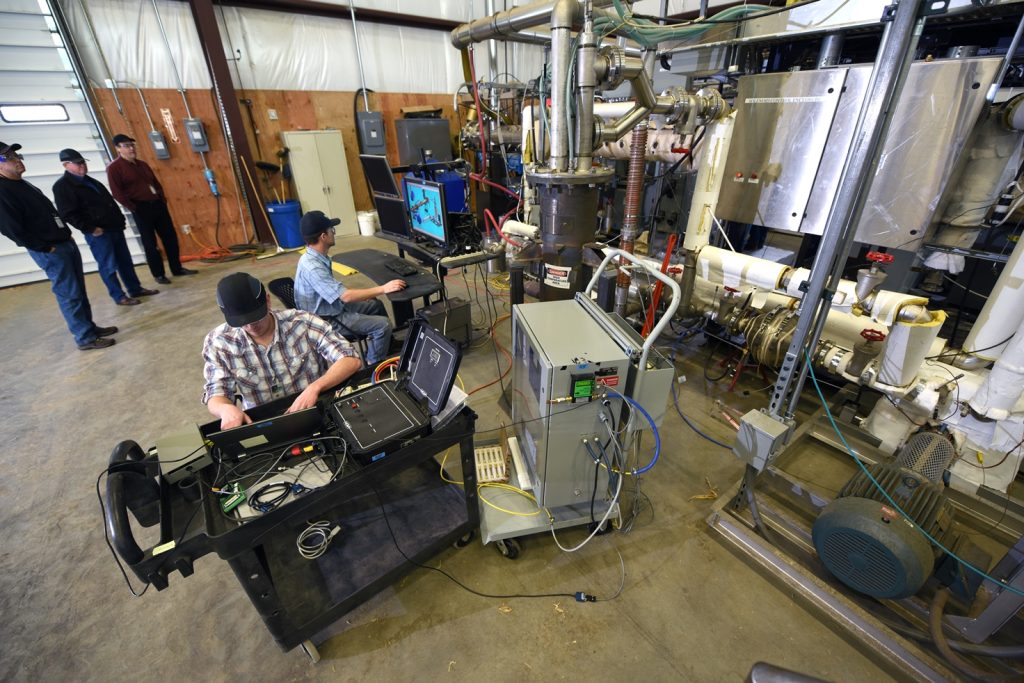
More work remains to determine the cost savings gained from incorporating oxidation catalysts in torrefaction systems, said Dr. Tyler Westover, an INL engineer who helped run the experiment. “The tests were successful,” Westover said. “Additional tests are planned to acquire the data needed to inform techno-economic analyses of the process.”
Further tests will also attempt to fine-tune the use of oxidation catalysts in INL’s torrefaction system. “The TorreCat™ Technology is expected to perform even better in commercial applications because the process control can be carefully optimized for specific feedstock materials and operating conditions to minimize the amount of oxygen exiting the oxidation catalyst,” Westover said.
When it came time for ATS to test its oxidation catalyst technology, BFNUF’s cutting-edge facilities and expert staff made INL the obvious choice, company representatives said.
“Tyler Westover, Michael Clark and other members of the INL staff took the time to clearly understand what we hoped to accomplish with the testing of our technology,” said Dan Herren, ATS president. “Their technical knowledge and experience were instrumental in achieving a successful result. We couldn’t have been more pleased.”