In July 2022, amidst a mechanical hum and complicated array of equipment filled with technicolor liquids, newly hired chemical engineering intern Rachel Umpleby learned, hands-on, about solvent extraction at one of Idaho National Laboratory’s (INL) many pilot programs. What’s more, she was learning from experienced aqueous separations and radiochemistry scientists, whose industry connections put them at the forefront of a strategic partnership with the United States’ only rare earth element mine.
Rare earth elements are essential to modern life, making up critical components in vehicles, cell phones and clean energy technologies. A foreign supplier has long dominated the production of rare earth elements, accounting for nearly 70% of the world’s rare earth mining and 80% of its rare earth processing in 2022. MP Materials, a California-based rare-earth materials company, aims to restore a domestic rare earth element market.
A comeback story in progress
MP Materials owns and operates the Mountain Pass mining and processing site just north of the Mojave National Preserve in California. Production there began in 1952, with the world’s highest quality deposits. From the 1960s to the 1990s, the mine was the primary global source of rare earth elements. Other countries ascended to the top of the rare earth supply chain shortly after, causing prior Mountain Pass owner Molycorp Minerals to halt operation indefinitely. When MP Materials acquired the Mountain Pass mine in 2017, it restarted operation immediately.
MP Materials’ separation of rare earth elements uses a technique known as solvent extraction. Using specialized equipment, chemical engineers use two unmixable solutions to separate a desired material. The process is like mixing oil and vinegar, which will eventually separate. In the nuclear industry, chemists separate the recyclable components of spent nuclear fuel with this same method. Due to the industrial scale of the mixer-settler equipment at Mountain Pass, the testing and validation of new extractants was not feasible. Think of mixing and settling enough material to fill a swimming pool. This is where INL stepped in to help. Using its flexible system of easily customizable, laboratory-scale equipment, the lab partnered with MP Materials to optimize a novel solvent extraction process.
“It was exciting for us to apply our work directly to an industrial challenge,” said Ramedy Flores, a chemical engineer at INL and principal investigator on the project. “We do a lot of fundamental research, expanding what we know about solvent extraction. But this time, we got to use what we already know to meet an immediate need and reduce U.S. reliance on foreign rare earth element supply. I’m so proud to work with such an amazing and talented group of individuals with a shared vision.”
INL’s historical involvement
The collaboration was 13 years in the making, originating when Molycorp Minerals contacted INL’s Aqueous Separations and Radiochemistry Department to perform a series of small-scale rare earth separations. That’s when INL Senior Technical Advisor on Fuel Cycle Science and Technology Kevin Lyon met the Mountain Pass mining and processing team.
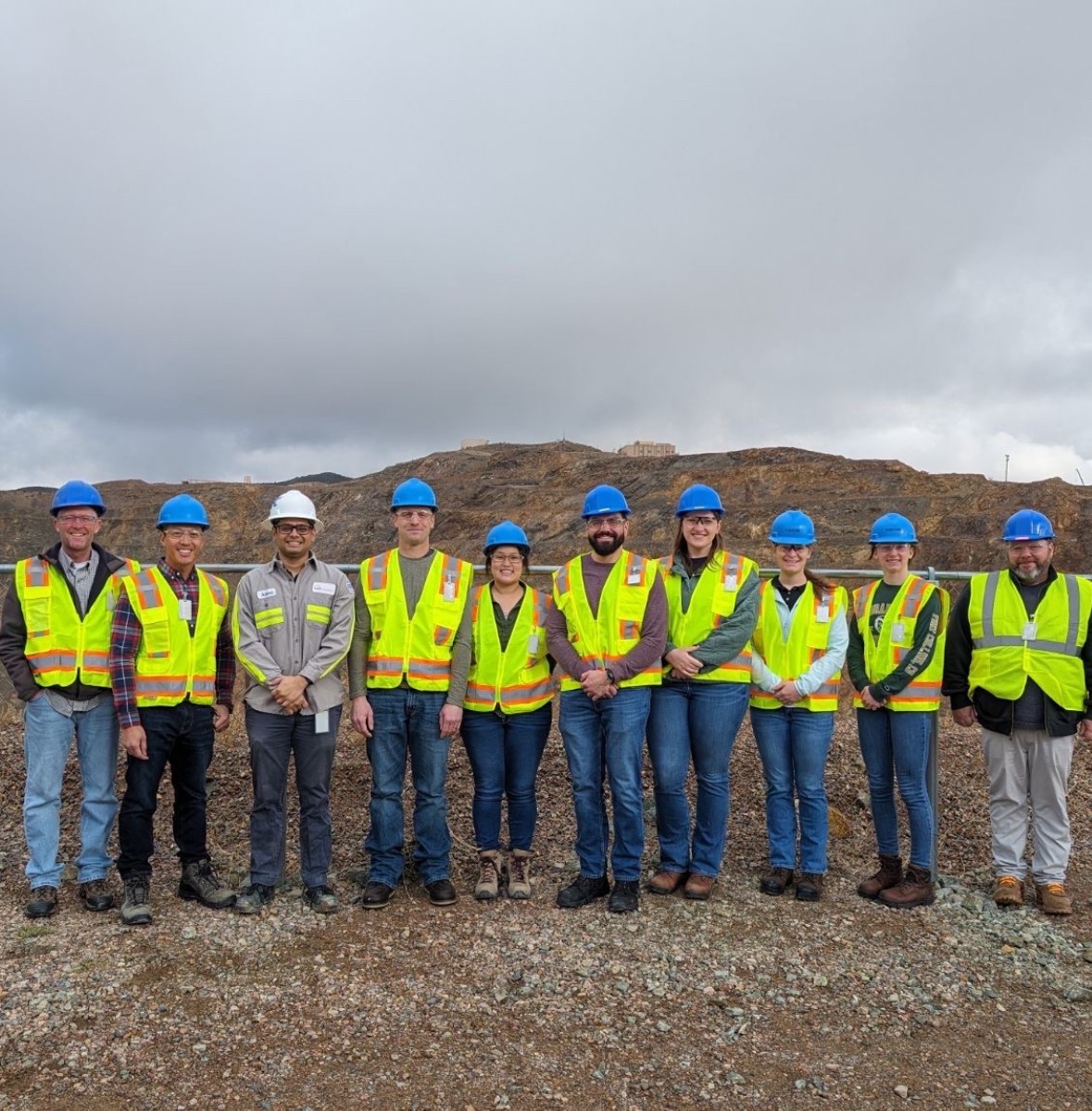
“For the better part of a decade, we’ve been in touch with them through (the Department of Energy’s) Critical Materials Innovation Hub, an Energy Innovation Hub that brings together multiple disciplines focused on similar issues,” said Lyon. “They would provide technical input and feedback on the science we were doing, providing industry perspective on developing new extractants and processes.”
The relationship between INL and the Mountain Pass team has endured since that first collaboration in 2011. “In 2022, we formed a strategic partnership project agreement to assist them with flowsheet testing, and it just took off from there,” said Lyon.
A unique early-career opportunity
Two years prior and over 1,800 miles away, Umpleby sat in an undergraduate chemistry class at Purdue University. “That was my first exposure to nuclear energy, and I thought it was really cool,” said Umpleby. “Then, when I attended a large career fair at Purdue, INL was there, and they told me about the SULI program.”
SULI, or the Summer Undergraduate Laboratory Internships program, offers STEM majors an opportunity to work directly with Department of Energy national laboratory teams. Through this program, Umpleby completed a radiation chemistry internship at INL in 2021 then returned for a chemical engineering internship in 2022 during the MP Materials collaboration.
Umpleby gained access to major industry collaborators and longtime aqueous separations chemists, but she also worked with other early-career personnel, such as Addyson Barnes. Barnes is an INL chemical engineer who trained interns while learning from industry experts about rare earth elements.
“We run solvent extraction flowsheets fairly often in our group, but this one was unique in that it was the bridge between proof-of-principle and industrial application,” said Barnes. “The experience gained in that space gives perspective on why we’re doing what we do. It makes us better researchers. It was also great to mentor an intern in that environment and work on a team with such diverse levels of experience.”
Collaborative success, now and into the future
While not an unlikely collision of worlds, Umpleby, Barnes, INL and MP Materials harnessed the right resources at the right time. Earlier this year, the Department of Energy awarded MP Materials $58.5 million to advance construction of America’s first fully integrated rare earth magnet manufacturing facility. Construction began in Fort-Worth, Texas, in 2022, but this financial assistance will help MP Materials meet its goal to produce finished neodymium-iron-boron magnets found in electric vehicles and critical defense systems by late 2025.
Umpleby, now a full-time INL chemical engineer, accompanied Barnes, Flores, Lyon and the rest of INL’s Aqueous Separations and Radiochemistry team on a January visit to the MP Materials mine, where they learned how impactful their testing was. “They are implementing the processes that we validated with them in their plant expansion,” said Barnes. “That growth includes the addition of a few hundred mixer-settler units. The fact that we had influence on nationally critical manufacturing activities is really gratifying.”
The relationship between INL and MP Materials is expected to continue. Conversations about designing new flow sheets and additional solvent extractions systems have already started.
As INL’s Aqueous Separations and Radiochemistry group looks to the future, they’re excited to bring up-and-coming STEM students along by pairing them with group experts and creating a team of professionals focused on solving problems to meet immediate industry needs.
“Rachel was a great asset to our team, and our early-career engineers really stepped up in providing essential input as we were troubleshooting throughout the process,” said Flores. “Seeing the knowledge transfer between our experienced personnel and our early career folks was an inspiring sight. Now that Rachel is a full-time chemical engineer with our group, it would be great to bring on more interns like her in the future, especially as we continue applying separations chemistry to industry solutions.”