Two teams from Rigby High School competed March 29 in the first Pathways Student Challenge, sponsored by the Department of Energy’s Feedstock Conversion Interface Consortium and supported with grants from Battelle Energy Alliance.
The student teams were given a budget of $2,000 to design and build machines that could continuously grind biomass feedstocks like wood chips, cardboard and chopped-up corncobs, which are used to make biofuels, bioproducts and biopower. In a head-to-head competition, the teams and their machines were put through their paces and evaluated by a team of experts in the Energy Systems Laboratory at Idaho National Laboratory.
“The prize for the winner was $3,000, but the value of the competition went far beyond money,” said Lex Godfrey, who teaches ag fabrication at the high school and advised both teams.
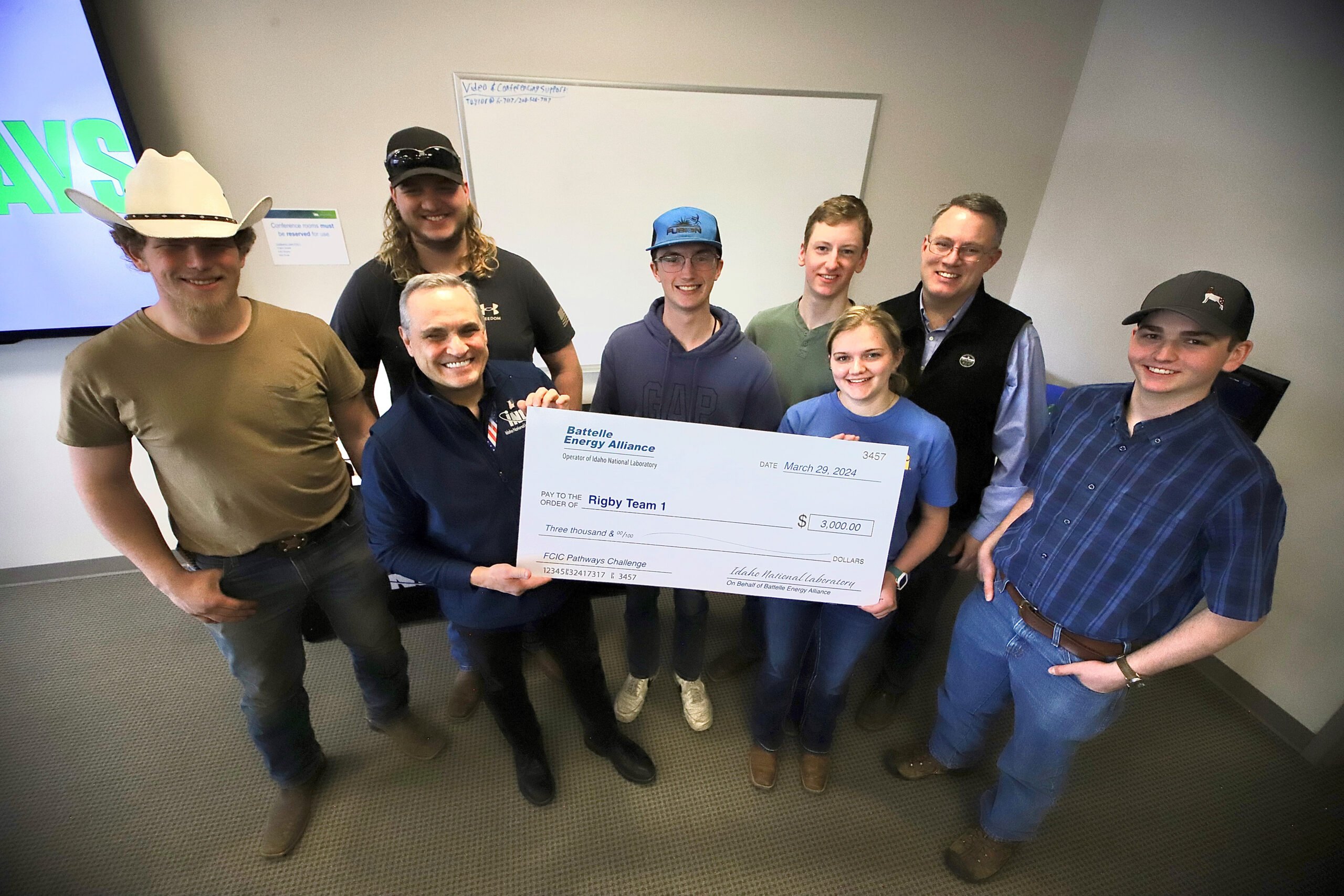
“It opened up their minds to see other opportunities and career choices,” he said. “Empowering education combined with invested stakeholders creates a return on investment that we’re going to see for a long time.”
The consortium is a collaboration of industry advisors and researchers at nine Department of Energy national laboratories who will address feedstock variability in biorefinery systems. Feedstock inconsistencies can be a big impediment to biorefineries operating continuously and profitably.
In early December 2023, INL announced it was looking for two high school student teams to build hoppers that could automatically process 2 gallons of shredded cardboard, corncobs and wood chips into material fine enough to be compressed into pellets. When Godfrey got the call and passed it along to his students, he found them eager and willing to take up the challenge.
“All of us jumped at it because we thought it would be a great experience,” said one of the participating students. “This was a big introduction to engineering.”
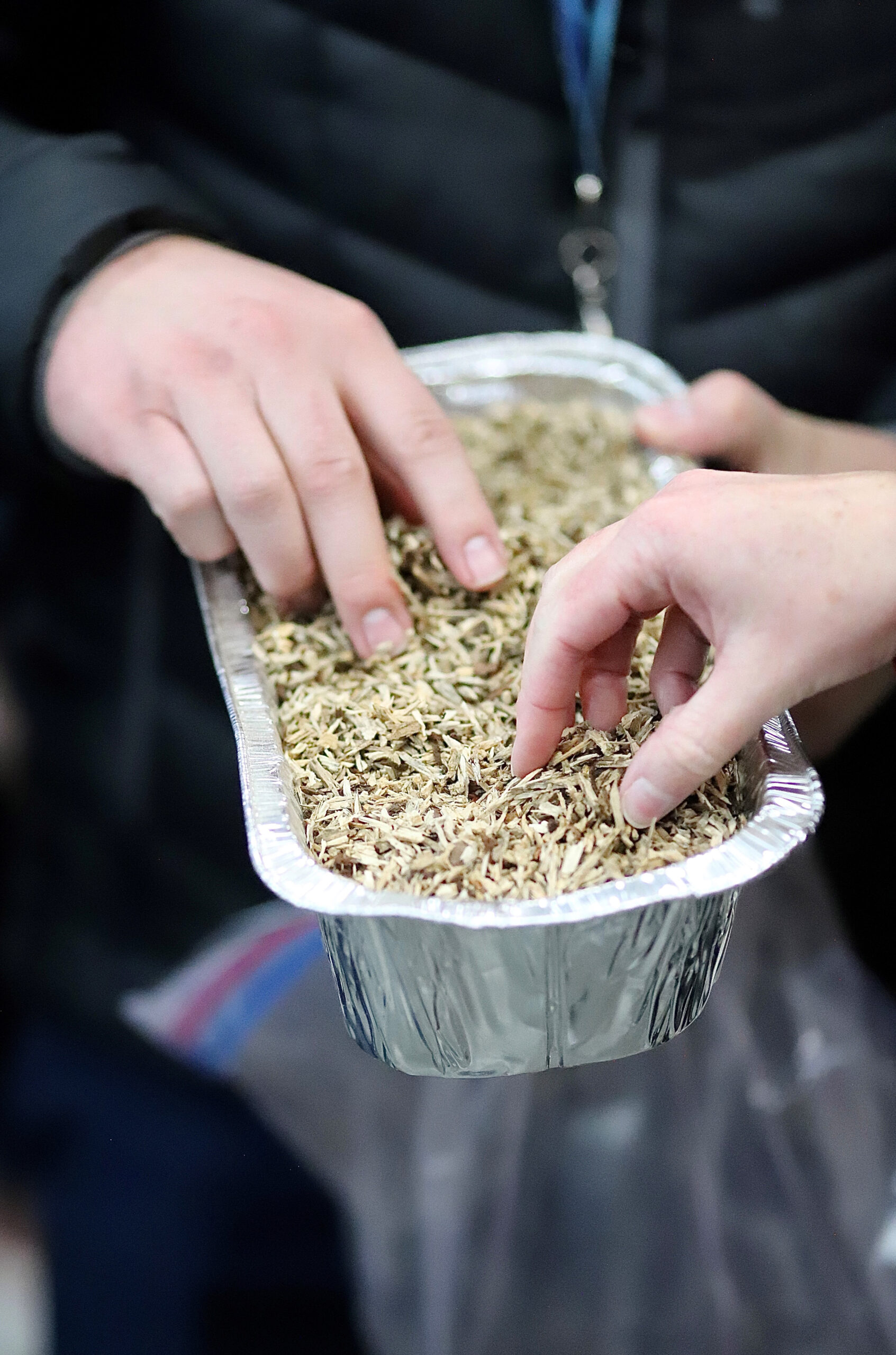
Teams could choose one of three designs:
- Vibratory feeder: A short conveyor that uses a controlled vibrating system to reorient random pieces of bulk material and guide them into a grinder.
- Vertical feeder: A system in which an oscillating motor churns the materials much like in a mixing bowl. Finely grained materials come out of the bottom, while larger materials are held and reprocessed.
- Bulk feeder: Materials are placed in the top and the hopper vibrates to shake materials down to a narrowed bottom where they are ground up.
Team 1 — Leonard Richardson, Braxton Geisler, Hayden Yearsley, Gavin Fry, Ammon Grant, Tyler Stucki and Bailee Ricks — opted for a bulk feeder that featured an open top and a sensor-activated pneumatic ram on the funnel side to prevent materials from bridging and clogging.
Team 2 — McKay Bird, Bryson Butikofer, Brody Brower, Hayden Griffeth, Tyler Barrett and Andrew Sauer — chose to build a vertical feeder that employed six high-pressure air nozzles to suspend the material and create a frictionless environment and an air regulator to manage flow.
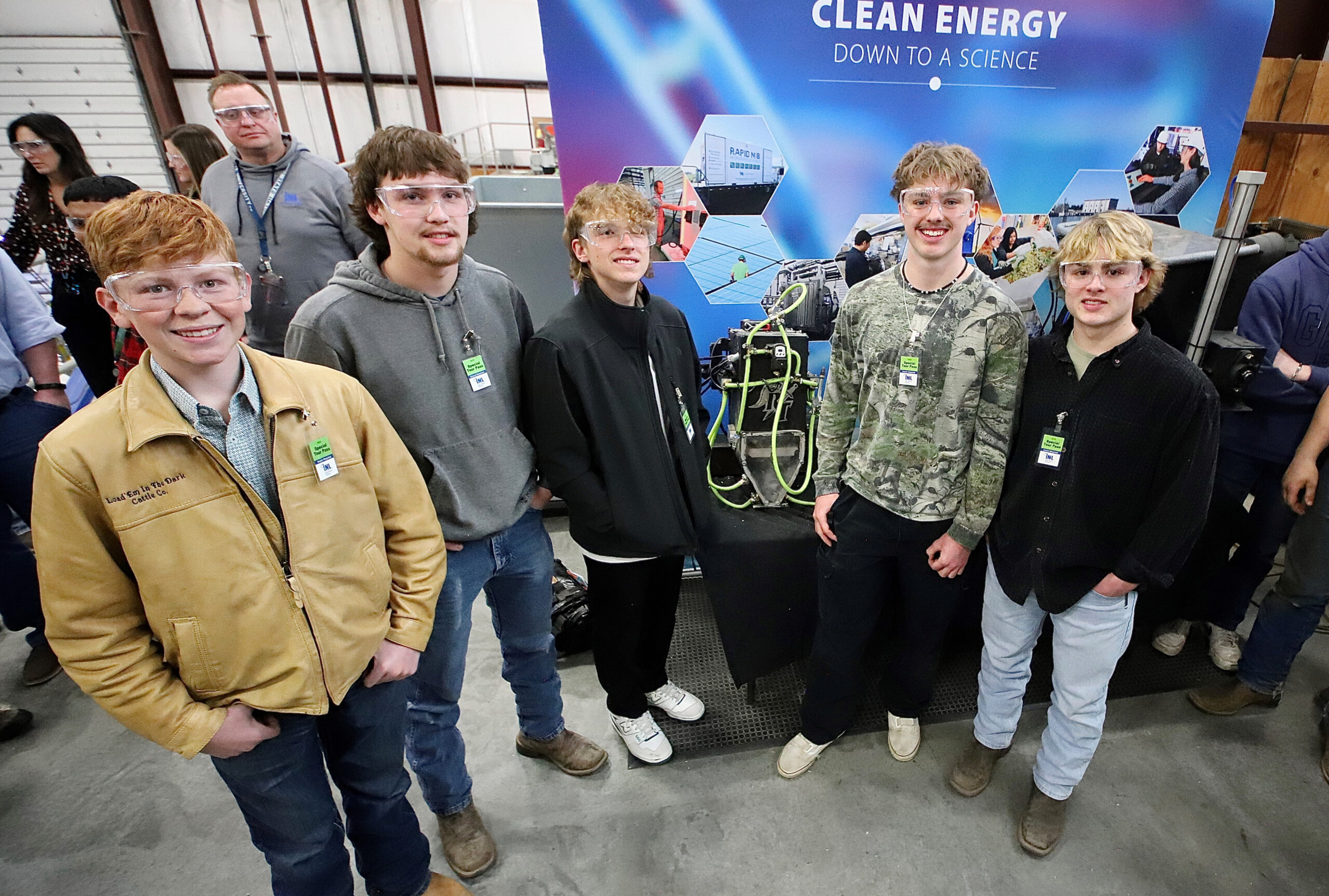
The teams had professional help from two INL employees: Biomass Engineer Kristian Egan and Tyler Butikofer, a design drafter (also the uncle of a team member). “I just gave advice,” Butikofer said. “I think they did a great job. I was concerned about the belt, and I am proud they came up with their own solution.”
For Team 1, simplicity was the goal. The team focused on combining ideas to develop a functional design. They first decided to incorporate the sensor-activated plunger. After considering a conveyor belt, they settled on using an augur instead.
For both teams, safety was a chief concern, with Team 1 incorporating a cover for the chain drive and Team 2 using air filters and latches to minimize dust.
At lunch, after the dust had settled, Team 1 was announced the winner. The judges considered much more than just the performance of the machines. Each team was judged on reports they presented and the “elevator pitches they made.”
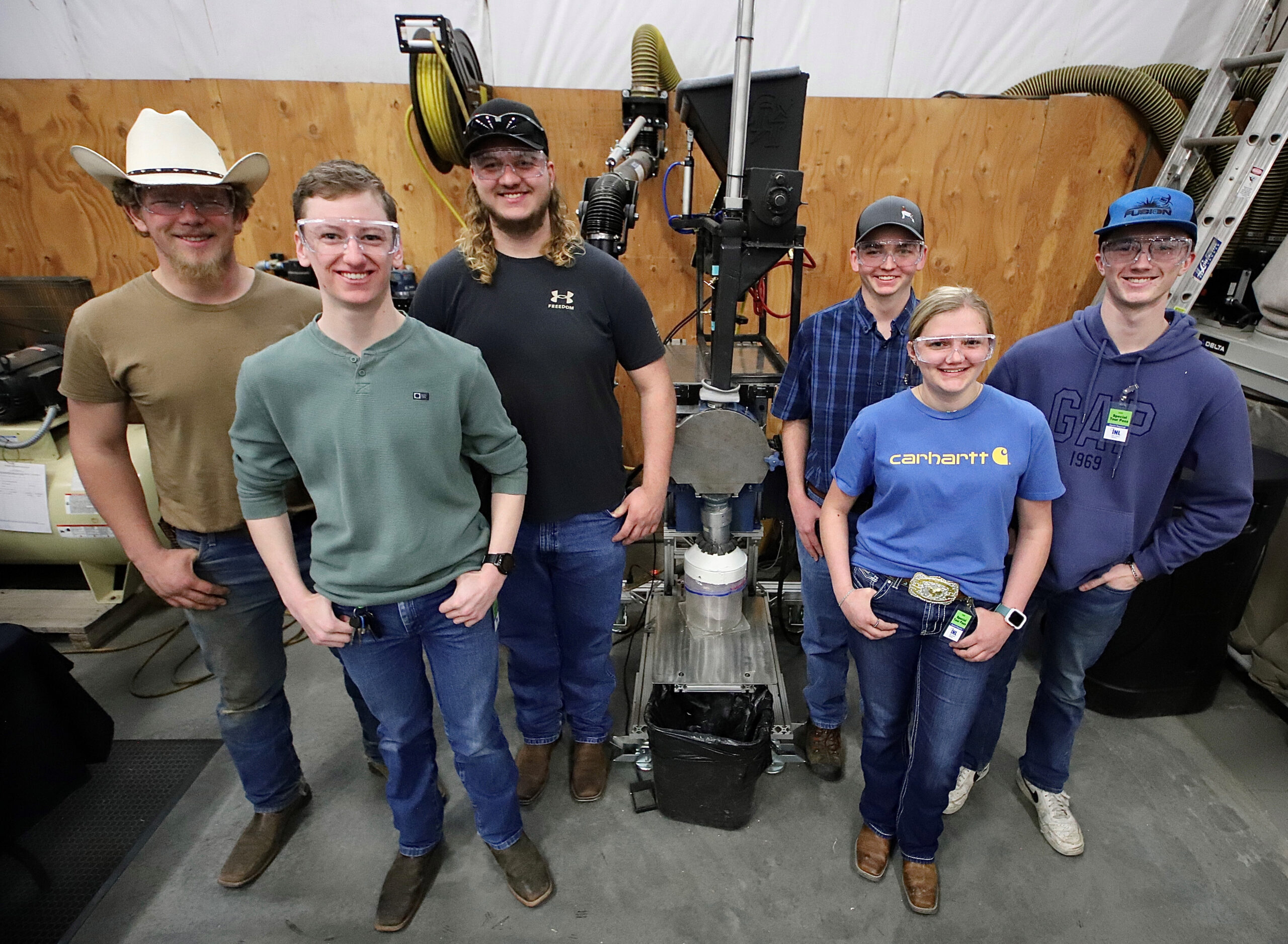
Coordinator Miranda Kuns of INL said the lessons learned from this inaugural event would be applied to next year’s competition. “Our goal is to get more rural schools involved with INL,” she said.