Whether it’s Edward Jenner, whose development of vaccines has likely saved billions of lives, or Marie Curie, whose theory of radioactivity helped unlock the mysteries of the atom, develop radiation therapy for cancer and create a carbon-free power source for the future, few endeavors wield as much power to change lives as that of the scientist/innovator.
At Idaho National Laboratory, 6,000 researchers and support staff members develop innovations to secure the nation’s energy future. That work includes not only nuclear energy but a wide range of disciplines, including electric vehicles, batteries, homeland security, bioenergy, critical materials and advanced manufacturing, to name a few.
While these innovations advance the laboratory’s mission, some make immediate, tangible differences for industry, customers or the public.
To recognize these achievements, the R&D 100 Awards, established in 1963, celebrate the top 100 revolutionary innovations — new commercial products, technologies and materials — that are available for sale or license in the past year.
INL researchers have tallied more than 70 R&D 100 Awards since 1986 for technologies as diverse as communications hardware to stop cybercriminals, processes that recycle valuable metals and computer codes that model nuclear fuel.
And, while winning just one R&D 100 Award can burnish a professional resume, INL boasts a handful of researchers who have won multiple times over their careers.
Of those, Robert Fox, Vicki Thompson, Seth Snyder and Aaron Wilson are threepeat winners and owe a large part of their success to years of expertise as leaders in their fields. Some have found a secret sauce that makes their research not only more relevant to industry and the world but also more appealing to the judges.
Vicki Thompson
Thompson, a distinguished staff engineer and manager of INL’s Bioenergy Feedstock Technologies Department, led teams that developed three award-winning biochemical processes.
Thompson and her colleagues took a deliberate approach.
“When we wrote those research proposals, we looked at existing technologies and processes and found gaps where they could be improved,” said Thompson. “It’s a strategy I think a lot of researchers take. Finding and identifying those gaps is something people don’t have time for or don’t think is important. But, in each of those winning projects, we were able to find something extraordinary.”
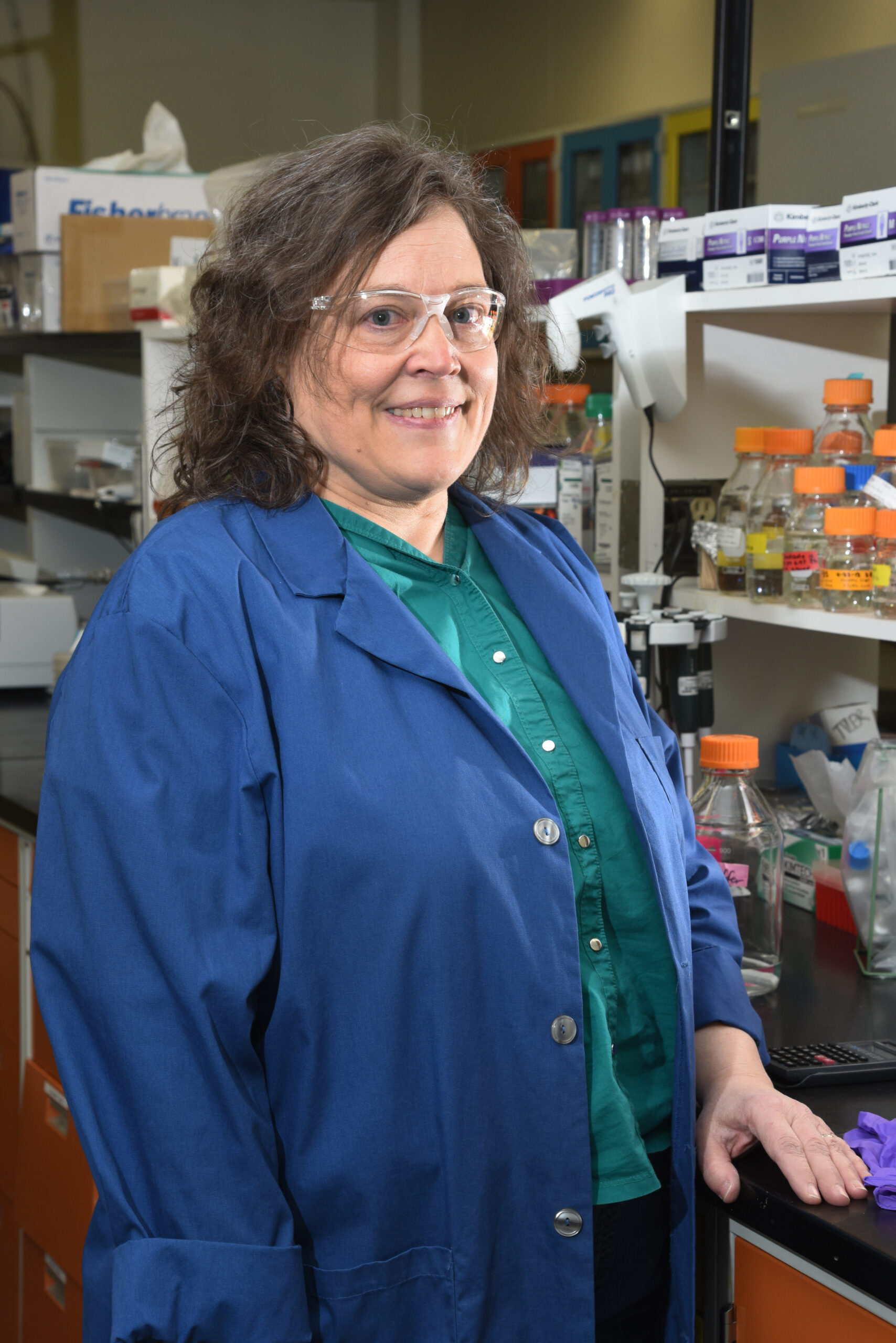
Robert Fox
Fox, the Materials Separations and Analysis department manager, attributes part of his team’s success to working in a science field that’s ripe for impacting industry, and part to the team itself.
“We’re the kind of people who sit upright in bed in the middle of the night and say, ‘That’s the answer,’” he said. “We’re swinging for the fence, and we’re connecting. We’ve got some really innovative people.”
Like Thompson, Fox won multiple R&D 100 Awards for seemingly dissimilar technologies.
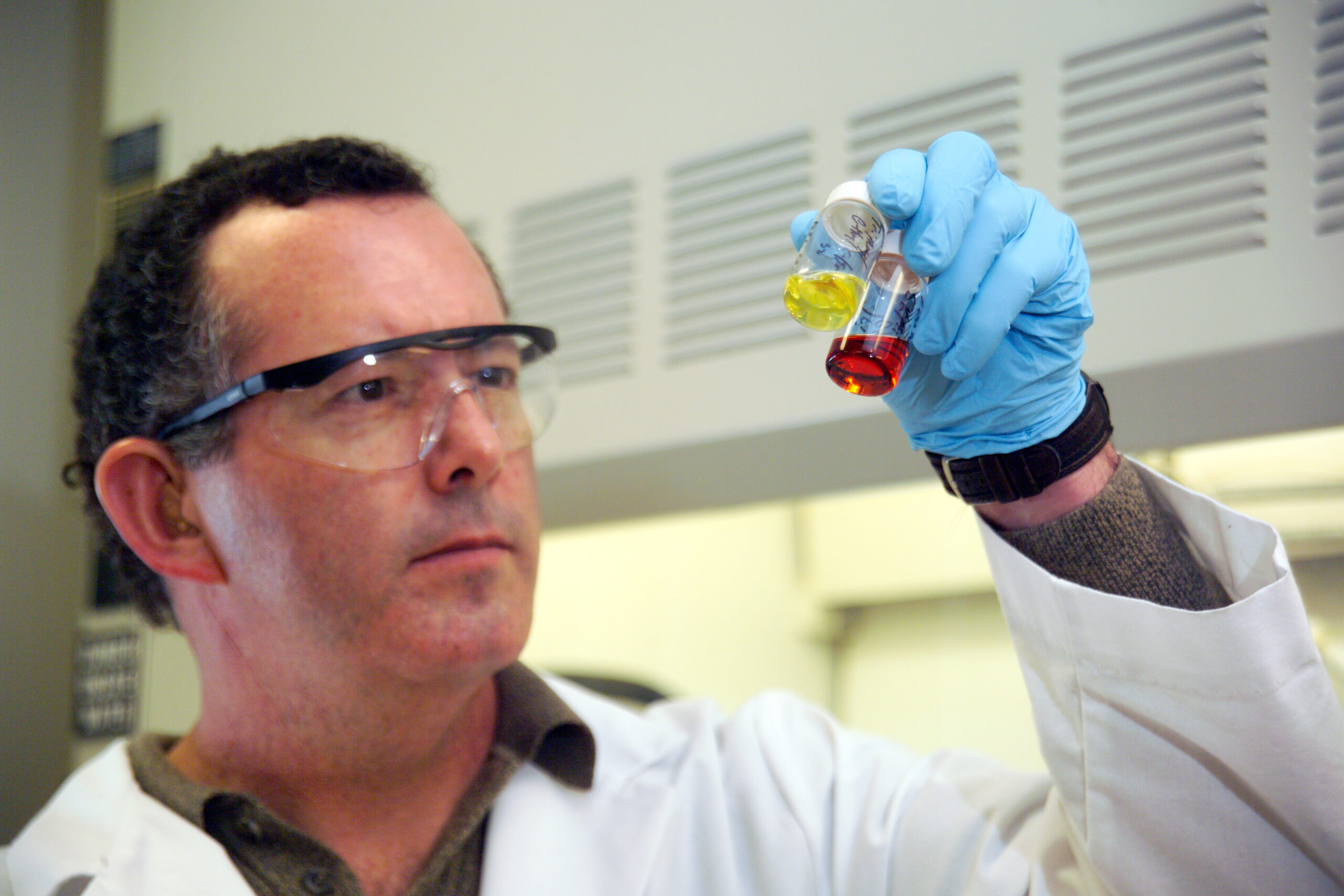
Seth Snyder
Snyder, directorate fellow in the Energy and Environment Science and Technology directorate, said the R&D 100 Awards are a good way to motivate people. “It’s great for early-career scientists,” he said. “It has a lot of gravitas with sponsors at the Department of Energy.”
Snyder won his three R&D 100 Awards during a 20-year stint at Argonne National Laboratory.
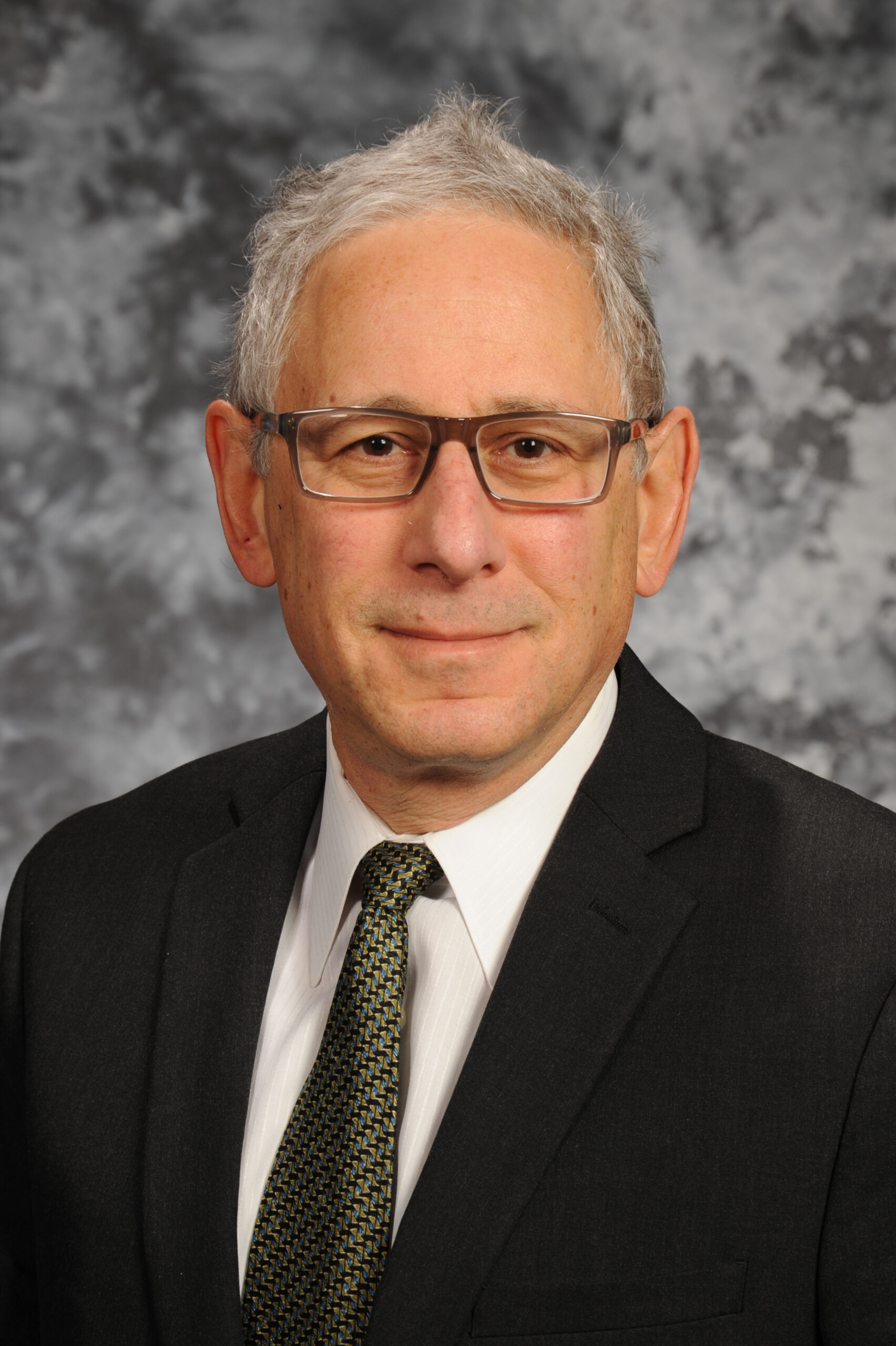
Aaron Wilson
Wilson, lead of the Chemical Separations group and a research lead in the Critical Materials Innovation Hub, agreed that it helps to be in a scientific field committed to solving problems for industry in real time.
“We’re culturally different from a lot of the laboratory,” he said. “We can say with a straight face we’re within five years of commercializing.”
Wilson’s secret for winning R&D 100 awards is threefold: “Get a good publication, get letters from people who want to license it and then do a one-to-one comparison with an existing technology.”
All three of Wilson’s wins came from using liquids with unusual phase behavior to solve different technical challenges, including wastewater treatment, carbon capture and conversion, and isolating critical minerals as solids.
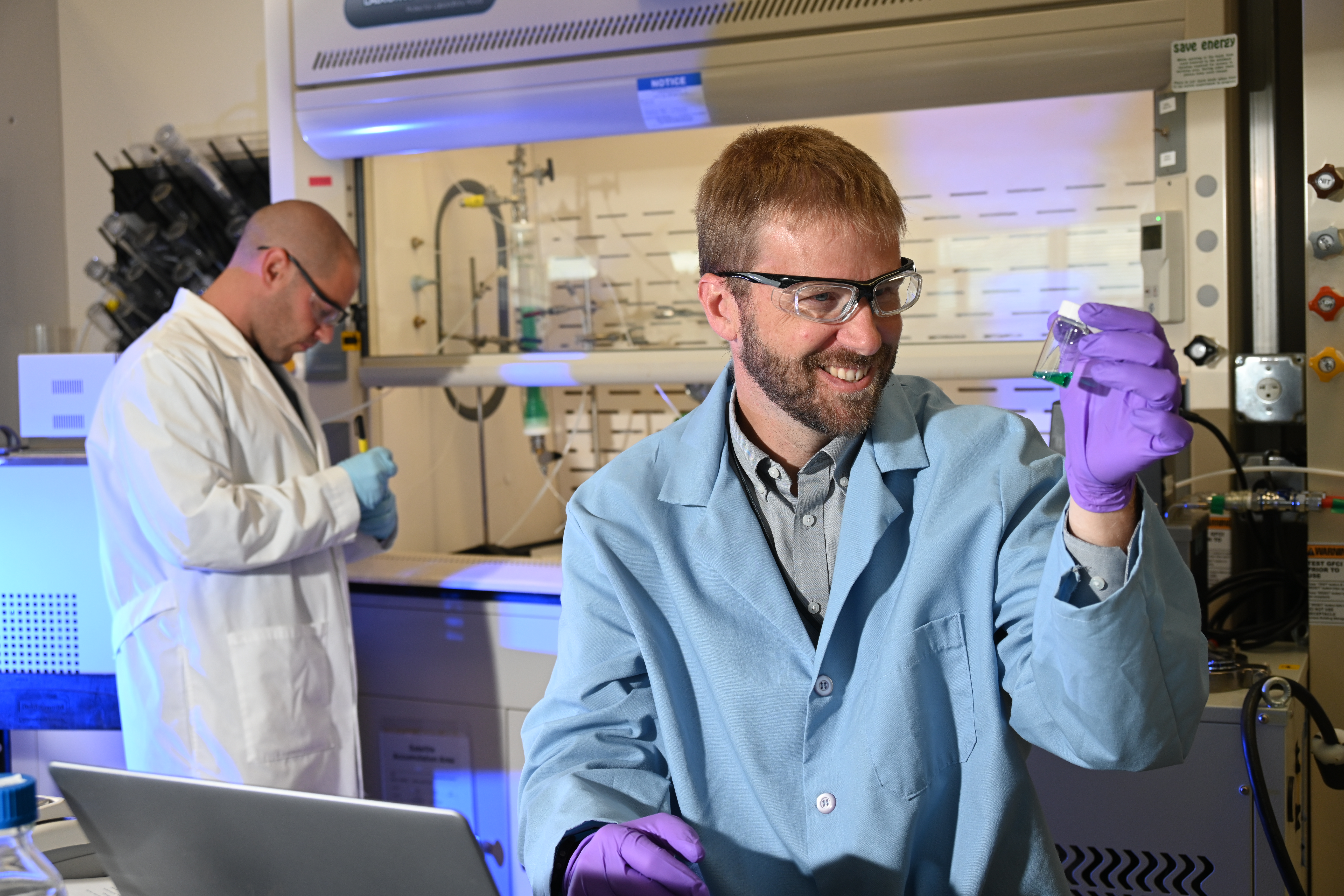
Laboratory Directed Research and Development
Of the 12 R&D 100 Awards earned by Thompson, Fox, Snyder and Wilson, nine projects were funded by INL or Argonne through the Laboratory Directed Research and Development (LDRD) programs.
The Department of Energy authorizes the lab to use a percentage of its budget for LDRD projects — highly innovative, high-risk, potentially high-value research and development.
“All of my R&D 100s came from LDRD funding,” Thompson said. “It gives you the freedom to explore things more than you would get from programmatic funding.”
Wilson agreed. “The most productive funds are LDRD funds,” he said. “LDRD trusts the researcher in a way that other DOE funding does not. It gives us the freedom to concentrate on the research without getting tied up with predetermined milestones.”
Long-term success?
In the end, the real motivation for researchers to innovate is less about awards and recognition and more about making a difference — ideally through the commercialization of their technology — even for a short amount of time.
“If you throw a pebble into a still lake, the ripple lasts for a long time,” said Fox. “Research and development is more like throwing a pebble into a stream of water.”
“For the average innovator out on the cutting edge of technology, often the impact lasts three to five years before they are overcome with other innovations,” he continued. “If that impact lasts for 10 or 15 years, wow, that is something. Now think about someone who has an impact for 30 to 50 years. That is Nobel Prize caliber.”
In the end, accolades like the R&D 100 Awards almost never give full credit to everyone behind the scenes who make innovations possible, Fox said. “The writers, the admin staff, the janitorial staff, the pipe fitters, the people in procurement who kept the supplies coming in — it’s Team INL all the way. All of them contributed,” Fox added.
A closer look at their winning technologies
Vicki Thompson
Ultra-Stable Catalase (2004)
Researchers: Vicki Thompson, William Apel, Kastli Schaller
Description: An enzyme that catalyzes the decomposition of hydrogen peroxide into oxygen and water at high temperature and pH. The enzyme could have a major impact on textile, food and pulp, and paper industries by enabling conversion to environmentally safe, cost-effective hydrogen peroxide processes as oxidizing and antimicrobial agents.
Xtreme Xylanase (Hemicellulase) (2006)
Researchers: William Apel, Kastli Schaller, Elizabeth Taylor, David Thompson, Vicki Thompson, Morgan Bruno
Description: Xtreme Xylanase is a highly acid- and heat-stable xylanase enzyme isolated from a Yellowstone National Park microbe cataloged in 1971. This enzyme can efficiently convert components of biomass feedstocks into energy-rich sugars that can replace petroleum to make fuels and high-value chemicals.
Antibody Profiling Identification (AbP ID) (2008)
Researchers: William Apel, Joni Barnes, Debra Bruhn, Karen Delezene-Briggs, Gregory Lancaster, Gordon Lassahn, Heather Silverman, Elizabeth Taylor, Vicki Thompson
Description: AbP ID is a rapid, inexpensive method to identify forensic evidence based on unique individual auto-antibody patterns. AbP ID incorporates a testing system and innovative pattern recognition software to expedite identifications.
Robert Fox
Precision Nanoparticles (2009)
Researchers: Robert Fox, Joshua Pak (Idaho State University), Rene Rodriguez (Idaho State University)
Description: This process uses supercritical carbon dioxide to produce high-quality, uniform nanomaterials of a prescribed size, ranging from smaller than 1 nm to 100 nm. Using temperature and pressure variances well within current commercial capabilities, Precision Nanoparticles can deliver specified-sized copper indium disulfide nanoparticles to harvest photon energy across the most intense segments of the solar spectrum. This may offer a major advance in producing new, more efficient solar materials to heat and power homes and businesses.
Supercritical/Solid Catalyst (SSC) (2010)
Researchers: Robert Fox, Daniel Ginosar, Lucia Petkovic, Daniel Wendt
Description: Discarded and environmentally unfriendly wastes can be converted into biodiesel fuels using SSC. INL scientists worked to find ways to create liquid fuels from a variety of streams, including municipal wastewater or food processing waste. SSC mixes fat or oil feedstock with supercritical fluid solvents and alcohols at specific temperatures and pressures to completely dissolve the materials during a single supercritical phase. This approach overcomes a key barrier — the polar liquid phase in conventional biodiesel production, which requires multiple steps.
RE-Metal (2021)
Researchers: Donna Baek, Robert Fox, Abderrahman Atifi
Description: RE-Metal helps solve an enormous challenge for U.S. manufacturers: enabling the environmentally friendly recycling of a limited supply of essential rare earth elements required for most of today’s high-tech devices. Recycling rare earth elements from high-tech devices typically involves a toxic process that’s banned in many countries, including the United States. RE-Metal enables the recovery of rare earth metals from waste electronics and other sources.
Seth Snyder
Electrodeionization (EDI) of Corn Syrup* (2002)
Researchers: Edward St. Martin, Michael Henry, Seth Snyder, Carl Landahl, Paula Moon, James Frank, YuPo Lin, Shih-Perng Tsai, Rathin Datta, Dennis Burke
Description: An electrochemical technology that uses ion exchange resins to remove salt after the isomerization process during the manufacture of high-fructose corn syrup.
Separative Bioreactor* (2006)
Researchers: Michael Henry, Seth Snyder, Edward St. Martin, Michelle Arora, Yupo Lin, James Frank, Jamie Hestekin, Rishi Shukla (Archer Daniels Midland Co.)
Description: A bioreactor for the production and recovery of biobased products in the bioenergy industry. The technology recovers organic acids from fermentation while eliminating the acidic environment that is incompatible with the microbes and enzymes that make fermentation possible.
Enhanced Renewable Methane Production System* (2008)
Researchers: Seth Snyder, Richard Doctor, Michael Henry, Rathin Datta, Meltem Urgun Demirtas, George Crandell, Taras Lysenko, Richard Leber
Description: A low-cost process for wastewater treatment plants, farms and landfills that uses calcium and magnesium silicates to accelerate methane production and sequester carbon dioxide. The resulting biogas is close to commercial quality.
*Developed when Seth Snyder worked for Argonne National Laboratory
Aaron Wilson
Switchable Polarity Solvent Forward Osmosis (SPS FO) (2013)
Researchers: Mark Stone, Fred Stewart, Aaron Wilson
Description: SPS FO combines the switchable polarity quality with forward osmosis to cleanse industrial wastewater. It leverages the switching qualities of selected specialized thermolytic salts and the characteristics of specialized membranes to accomplish the task. Low cost and environmentally friendly, SPS FO can purify water from extremely concentrated solutions, especially those containing salts, organics, inorganics, biologics and many other materials.
Carbon Capture and Utilization through Reduction Electrolysis (CURE) (2020)
Researchers: Luis Diaz Aldana, Ningshengjie Gao, Tedd Lister, Birendra Adhikari, Aaron Wilson, Eric Dufek
Description: Decarbonizing energy production through carbon capture and sequestration is a popular idea that has been plagued by operational and economic challenges, but integrating carbon capture with reuse to make high-value products could offer an operational advantage. The Carbon CURE process provides a solution by using recyclable solvents as a carbon capture medium that can be fed directly to an electrochemical cell. The cell converts carbon dioxide to syngas, the building block for a range of high-value products. The process will help achieve economical carbon capture at an industrial scale.
Ether-based Aqueous Separation and Extraction (EASE) (2023)
Researchers: Aaron Wilson, Ikenna Nlebedim (Ames National Laboratory), Caleb Stetson, Denis Prodius (Ames National Lab), Christopher Orme, Hyeonseok Lee, Ashini Jayasinghe
Description: EASE is an emerging technology to separate valuable mineral salts as solids from wastewater and dilute sources. This process significantly reduces the energy and chemicals used for water treatment and mineral recovery without creating a new waste stream.