Builders typically rely on a set of printed, complicated blueprints at the job site to communicate complex architectural building designs. But blueprints don’t always work, especially when there are multiple iterations of the same plan with different pieces of information across multiple sheets.
Builders are often left interpreting the designer’s intent rather than building per the plan, which can result in costly mistakes and delayed timelines.
An industry well versed in “MacGyvering” fixes or workarounds has coped. But longtime friends and co-owners of Flashpoint Building Systems, Nick Stoppello and Pat Churchman, wanted a more sustainable solution.
“We spent years during college and post-graduation in the construction-architecture realm dealing with this common theme, regardless of the project type, location (or) subcontractor base,” Stoppello said. “And after enough commiserating we decided to come up with an idea that might solve the problem. We figured the worst we could do is fail, but we should at least try.”
Their solution is the Integrated Layout System, a “paint by numbers” approach to building that sets aside traditional blueprints and provides builders with a better method of executing the work at the job site.
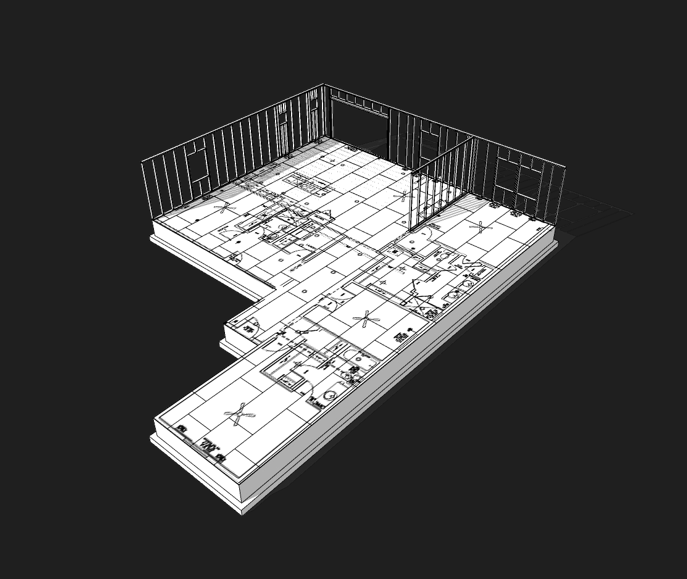
“We wanted to empower the people we have to be more effective and set them up with the tools needed to do the job right,” he said.
The Integrated Layout System laser engraves the building plans directly onto the oriented strand board (OSB) subfloors or plywood panels at a one-to-one scale. Stoppello said this large-scale solution may not seem revolutionary, but it consolidates the plan set to have all the pertinent information for the builder to complete the different assemblies at its exact spot on the plan. For example, if you’re building out a window, it gives you the exact measurements and dimensions where that window is located on the jobsite. The same goes for the electrical needs and other aspects of a build.
This shift in how designers communicate plan information and use it in the field has substantially reduced costs and construction timelines, Stoppello said.
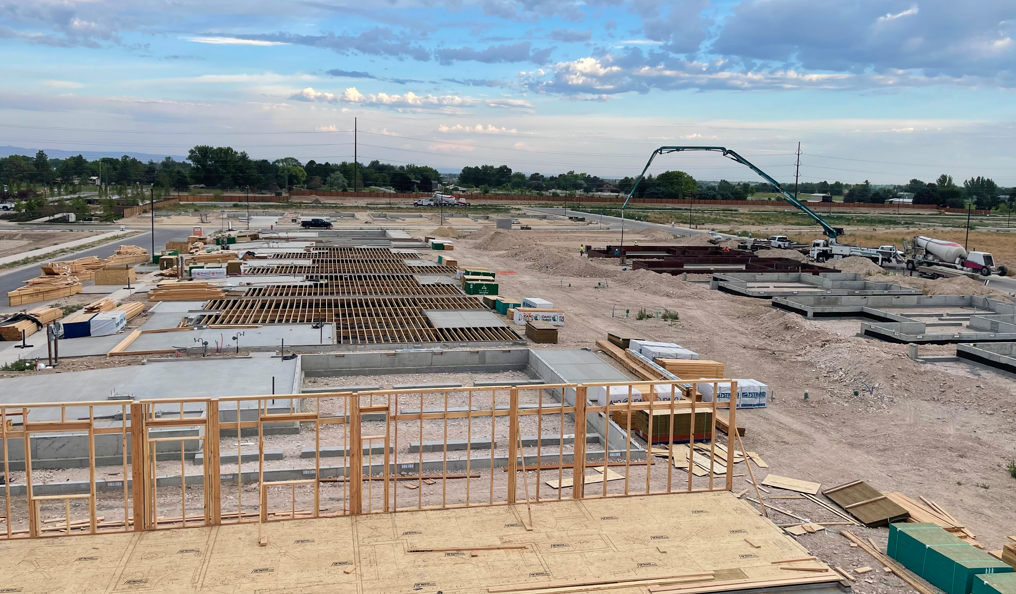
Tapping INL’s help
Flashpoint reached out to Idaho National Laboratory (INL) to make sure the laser engraving didn’t compromise the quality of the OSB material and to make sure the material maintained its waterproofing characteristics.
Flashpoint also engaged the University of Idaho to conduct tests to evaluate the structural integrity of the OSB material post laser engraving.
Under the lab’s Technical Assistance Program, INL researcher Ninad Mohale assisted Flashpoint with evaluating whether the laser engraving affected the waterproof characteristics of the OSB material. The Technical Assistance Program provides organizations and small businesses with free access to the laboratory’s world-class expertise, state-of-the-art facilities and advanced research capabilities.

Mohale took OSB samples from Flashpoint and performed a series of tests to analyze the boards to ensure they meet industry standards for strength, durability and performance.
Other ways the lab helped include:
Optical microscopy analysis: INL captured high-resolution images of the laser-engraved areas to evaluate the depth, uniformity and potential defects of the engraved lines. The results found uniformity, critical to integrity and reliability, of the material’s performance post engraving.
X-ray fluorescence analysis: Using powder samples collected from the laser-engraving regions of the OSB, researchers focused on the elemental composition of the OSB, specifically the waterproofing epoxy.
X-ray diffraction analysis: Researchers X-rayed samples to evaluate the crystalline structure of the epoxy resin in the OSB samples post laser engraving, confirming the material’s waterproof characteristics were not compromised.
“INL’s testing capabilities negated any concerns we had about the structural integrity of the OSB,” Stoppello said. “It helped us check off that box.”
INL mission
The Technical Assistance Program and other lab programs are moving INL’s mission forward as the opportunity to lend expertise or access to lab facilities benefits our communities. The lab is constantly looking for opportunities to help small businesses, industry, universities or other entities achieve or find needed energy solutions.
“Through these strategic partnerships, INL is accelerating innovation,” INL Technology Deployment Director Jason Stolworthy said. “It’s amazing to watch our visions of change become reality.”
To learn more about technology deployment programs or licensing opportunities, email [email protected].