For almost three years, Idaho National Laboratory has been involved in Battery500, a U.S. Department of Energy-sponsored initiative to develop high energy, long-life batteries. The researchers have produced a number of papers that explain why battery designers might want to “think outside the lab” and pay some attention to the real world.
Researchers at four national laboratories and five universities, along with advisers from the U.S. Advanced Battery Consortium and NAATBatt (a not-for-profit trade association) are working to meet the five-year project goal. Their aim: engineer a rechargeable lithium-metal battery (RLB) with more than twice the “specific energy” found in the batteries that power today’s electric vehicles (EVs) while simultaneously achieving 1,000 EV charge/recharge cycles. Specific energy is the amount of energy packed into a battery based on its weight. Because EVs need to be lightweight to drive farther on the same charge, EV batteries with high specific energies are essential.
At INL, the focus has been on defining and testing RLB configurations that resemble what’s likely to be used in the real world. Weight is a particular concern, as greater amounts of electrolyte are likely to make batteries too heavy to meet the 500 Wh/kg goal.
While most electric vehicles and consumer devices have lithium-ion batteries, researchers have shifted their focus to RLB systems because they show potential for 2.5 times the energy density of today’s lithium-ion cells. Battery500’s goal is to produce an RLB unit that stores 500 watt-hours per kilogram (Wh/kg) and is capable of 1,000 charging cycles. So far, researchers at Pacific Northwest National Laboratory, the lead Batttery500 lab, have produced a cell in a lab setting with specific energy of 350 Wh/kg and more than 250 cycles.
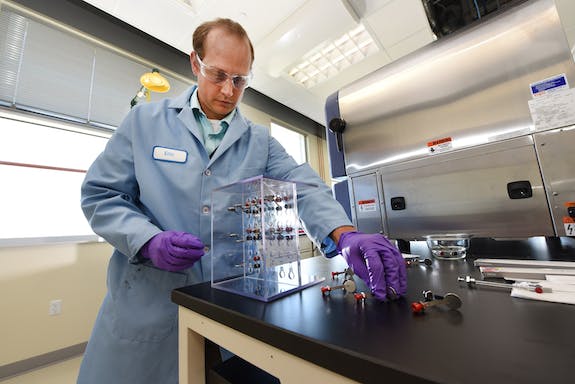
“We’ve seen how coin cell research can misstate cycle life by as much as 4.5 times,” said Eric Dufek, lead researcher in INL’s Energy Storage Group. “Coin cells can be loaded with 45 to 75 times the electrolyte as a commercial lithium-ion battery.”
Since 2018, researchers in INL’s Clean Energy Transportation Division have authored or contributed to five papers on the topic in various journals.
One of the recent papers, Impacts of lean electrolyte on cycle life for rechargeable Li metal batteries — published in October 2018 in the Journal of Power Sources — describes how experimental studies of electrolyte performance may be missing the mark because they use more electrolyte than is practical in real-world applications.
The study suggests that when comparing high-performing electrolytes, engineers need to pay more attention to the expected commercial design criteria when making claims about enhanced performance. Otherwise, when the time comes to develop a commercial battery, customers excited by lab test numbers might end up feeling like victims in an “overpromise/underdeliver” scenario, Dufek said.
When a battery cell is being charged and discharged, ions flow through electrolyte between the cathode and anode. Two things happen to cause a decline in performance: the electrolyte gets used up, and side reactions cause layers of buildup on the electrodes that damages them.
While a “lean” cell with lower-than-standard electrolyte content will die quicker, a “flooded” cell has its own failure pathway, involving aging of the positive electrode, electrode kinetics, and loss of accessible lithium from the negative electrode. A researcher might get a desired result by putting 25 times more electrolyte in a cell than a regular battery might have, Dufek said.
“Unlike the first failure pathway, the use of excess electrolyte masks variations among a group of cells and key failure mechanisms due strictly to the flooded nature of the experiment,” the paper says. “Thus, while a comparison between different electrolytes is feasible using flooded conditions, little information which can be translated to a high specific energy cell design is generated.”
Shrikant Nagpure, a former employee and one of the paper’s lead authors, said the Battery500 goals forced them to think outside the lab. Too much electrolyte in a battery might make the battery too heavy when expanded to a unit designed for use in an electric vehicle.
“There was a shift in thought we had in our group,” Nagpure said. “We’re saying now, ‘Think of how much it is going to weigh when you scale up.’”
In addition to Dufek and Nagpure, the paper was co-authored by Tanvir Tanim, Sean Wood, Charles Dickerson and Boryann Liaw. INL collaborated with PNNL on cell design calculations.
The article acknowledges that getting electrolyte levels right is only a first step. “(As) the quantity of electrolyte becomes closer to the levels needed to design a high specific energy cell, cell-to-cell variability increases,” the authors wrote. “… more profound understanding of the factors which drive variability need to be addressed to further advance the possibility of RLBs. Only with conditions more in line with true cell designs can inference of increased cycle life or performance be achieved.”
Nagpure said they have since focused on more detailed analysis of failure mechanisms, mainly loss of electrolyte and loss of electrode materials.
DID YOU KNOW?
Idaho National Laboratory started testing batteries in 1983, the year the U.S. Department of Energy moved electric car research there from Jet Propulsion Laboratory in California. At the time, EVs were typically powered by lead acid batteries with energy density of 35 to 40 watt-hours per kilogram.
Battery500-related research papers in which INL researchers have participated:
“Critical Parameters for Evaluating Coin Cells and Pouch Cells of Rechargeable Lithium-Metal Batteries,” Joule; Eric J. Dufek contributor; published March 20, 2019
“Implications of Local Current Density Variations on Lithium Plating Affected by Cathode Particle Size,” Journal of The Electrochemical Society; Alexander W. Abboud, Eric J. Dufek and Boryann Liaw; published March 2, 2019
“Pathways for practical high-energy long-cycling lithium metal batteries,” Nature Energy; Dufek, Liaw; published Feb. 25, 2019
“Impacts of lean electrolyte on cycle life for rechargeable Li metal batteries,” Journal of Power Sources; Shrikant C. Nagpure, Tanvir R. Tanim (co-lead authors), Eric J. Dufek, Sean M. Wood, Charles C. Dickerson, Boryann Liaw; published Oct. 23, 2018
“Predicting Calendar Aging in Lithium Metal Secondary Batteries: The Impacts of Solid Electrolyte Interphase Composition and Stability,” Advanced Energy Materials; Dufek, Wood, Nagpure, Liaw Sergiy V. Sazhin; published Aug. 6, 2018
Published Oct. 15, 2019
By Paul Menser for INL Communications & Outreach