If you follow the directions in a cake recipe, you expect to end up with a nice fluffy cake. In Idaho Falls, though, the elevation can affect these results. When baked goods don’t turn out as expected, the troubleshooting begins. This happens in chemistry, too. Chemists must be able to account for how subtle changes or additions may affect the outcome for better or worse.
Chemists make their version of recipes, known as reactions, to create specific materials. These materials are essential ingredients to an array of products found in healthcare, farming, vehicles and other everyday products from diapers to diesel. When chemists develop new materials, they rely on information from previous experiments and predictions based on prior knowledge of how different starting materials interact with others and behave under specific conditions. There are a lot of assumptions, guesswork and experimentation in designing reactions using traditional methods. New computational methods like machine learning can help scientists better understand complex processes like chemical reactions. While it can be challenging for humans to pick out patterns hidden within the data from many different experiments, computers excel at this task.
Using machine learning to predict chemical reactions
Machine learning is an advanced computational tool where programmers give computers lots of data and minimal instructions about how to interpret it. Instead of incorporating human bias into the analysis, the computer is only instructed to pull out what it finds to be important from the data. This could be an image of a cat (if the input is all the photos on the internet) or information about how a chemical reaction proceeds through a series of steps, as is the case for a set of machine learning experiments that are ongoing at Idaho National Laboratory.
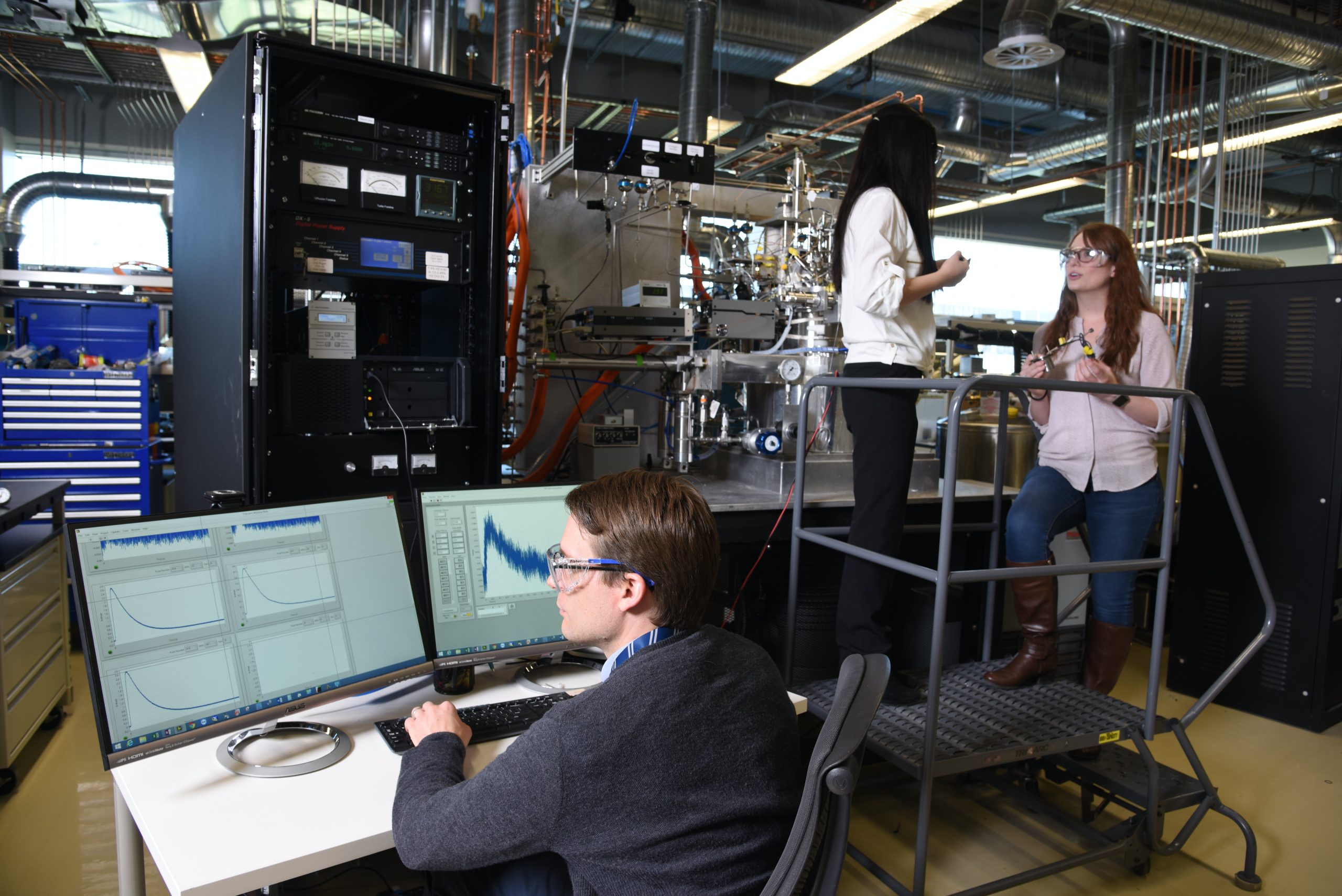
At the lab, researchers working with the innovative Temporal Analysis of Products (TAP) reactor system are trying to improve understanding of chemical reactions by studying the role of catalysts, which are components that can be added to a mixture of chemicals to alter the reaction process. Often catalysts speed up the reaction, but they can do other things, too. In baking and brewing, enzymes act as catalysts to speed up fermentation and breakdown sugars in wheat (glucose) into alcohol and carbon dioxide, which creates the bubbles that make bread rise and beer foam.
In the laboratory, perfecting a new catalyst can be expensive, time-consuming and even dangerous. According to INL researcher Ross Kunz, “Understanding how and why a specific catalyst behaves in a reaction is the holy grail of reaction chemistry.” To help find it, scientists are combining machine learning with a wealth of new sensor data from the TAP reactor system.
The TAP reactor system uses an array of microsensors to examine the different components of a reaction in real time. For the simplest catalytic reaction, the system captures 8 unique measurements in each of 5,000 time points that make up the experiment. Assembling the time points into a single data set provides 165,000 measurements for one experiment on a very simple catalyst. Scientists then use the data to predict what is happening in the reaction at a specific time and how different reaction steps work together in a larger chemical reaction network. Traditional analysis methods can barely scratch the surface of such a large quantity of data for a simple catalyst, let alone the many more measurements that are produced by a complex one.
Taking the next step with artificial intelligence
Machine learning methods can take the TAP data analysis further. Using a type of machine learning called explainable artificial intelligence, or AI, the team can educate the computer about known properties of the reaction’s starting materials and the physics that govern these types of reactions, a process called training. The computer can apply this training and the patterns that it detects in the experimental data to better describe the conditions in a reaction across time. The team hopes that the explainable AI method will produce a description of the reaction that can be used to accurately model the processes that occur during the TAP experiment.
In most AI experiments, a computer is given almost no training on the physics and simply detects patterns in the data based upon what it can identify, similar to how a baby might react to seeing something completely new. By contrast, the value of explainable AI lies in the fact that humans can understand the assumptions and information that lead to the computer’s conclusions. This human-level understanding can make it easier for scientists to verify predictions and detect flaws and biases in the reaction description produced by explainable AI.
Implementing explainable AI is not as simple or straightforward as it might sound. With support from the Department of Energy’s Advanced Manufacturing office, the INL team has spent two years preparing the TAP data for machine learning, developing and implementing the machine learning program, and validating the results for a common catalyst in a simple reaction that occurs in the car you drive everyday. This reaction, the transformation of carbon monoxide into carbon dioxide, occurs in a car’s catalytic converter and relies on platinum as the catalyst. Since this reaction is well studied, researchers can check how well the results of the explainable AI experiments match known observations.
Using computer simulations to predict outcomes
In April 2021, the INL team published their results validating the explainable AI method with the platinum catalyst in the article “Data driven reaction mechanism estimation via transient kinetics and machine learning” in Chemical Engineering Journal. Now that the team has validated the approach, they are examining TAP data from more complex industrial catalysts used in the manufacture of small molecules like ethylene, propylene and ammonia. They are also working with collaborators at Georgia Institute of Technology to apply the mathematical models that result from the machine learning experiments to computer simulations called digital twins. This type of simulation allows the scientists to predict what will happen if they change an aspect of the reaction. When a digital twin is based on a very accurate model of a reaction, researchers can be confident in its predictions.
By giving the digital twin the task to simulate a modification to a reaction or new type of catalyst, researchers can avoid doing physical experiments for modifications that are likely to lead to poor results or unsafe conditions. Instead, the digital twin simulation can save time and money by testing thousands of conditions, while researchers can test only a handful of the most promising conditions in the physical laboratory.
Plus, this machine learning approach can produce newer and more accurate models for each new catalyst and reaction condition tested with the TAP reactor system. In turn, applying these models to digital twin simulations gives researchers the predictive power to pick the best catalysts and conditions to test next in the TAP reaction. As a result, each round of testing, model development and simulation produces a greater understanding of how a reaction works and how to improve it.
“These tools are the foundation of a new paradigm in catalyst science but also pave the way for radical new approaches in chemical manufacturing,” said Rebecca Fushimi, who leads the project team.