Many of today’s high-performance technologies—nuclear reactors, spacecraft, concentrated solar plants and hydrogen cells—require advanced materials. The “advanced” aspect comes from the fact that they’re made of metals and ceramics that can withstand extreme conditions or meet exacting specifications.
In the past, these advanced materials were typically manufactured from powder that was poured into a die, subjected to high pressure and slowly heated in a process called hot pressing.
However, hot pressing results in lot of waste heat, contributing to high costs. Those costs have limited the widespread use of advanced materials in industries that manufacture everyday items such as automobiles.
More recently, engineers have developed a cost-saving process called spark plasma sintering (SPS). Instead of heat, SPS sends electricity through the die, and sometimes the material itself, to fuse the molecules of powdered metals, ceramics or a mixture of both.
Now, Idaho National Laboratory has developed world-class capabilities to help industry design efficient SPS manufacturing processes. The lab’s newest addition, one of the largest machines of its kind in the world, makes it possible to manufacture new materials at industrially relevant scales.
“The SPS process is much faster, much more energy efficient, and more capable of maintaining the original, superior powder properties in the fully sintered part,” said Troy Holland, a senior SPS materials scientist/engineer at INL.
Maintaining the properties of the original powdered material is important because of the often-stringent performance requirements of these parts. “If you heat them up for a long time you often lose the benefits that you had in the original powder,” Holland said.
Four custom-built machines
INL has designed and built four custom SPS machines that range from supporting small experiments on the bench-scale to industrial-scale, large-format, high-throughput systems.
As its name implies, the Nano-SPS is a small machine that can fuse together metal or ceramic powder to make parts from the nano- to micrometer scales. The Nano-SPS isn’t made for building commercial parts, per se, but is an experimental machine that can help researchers predict and control the nanostructure and microstructure of a component by observing how powder materials flow and interact at nanometer resolution.
X-ray and neutron diffraction experiments using the Nano-SPS setup provide real time data about chemical and microstructure evolution during the SPS process.
Understanding how the powder molecules interact during SPS, from atomic bonds to local nanostructures to microstructures, is important because variation at these scales can make a big difference in performance.
“Our goal is to understand and control the process well enough to be able to control local microstructures of parts,” Holland said, “This allows us to minimize variation or take advantage of local intentional variation within the part in as repeatable a way as possible to produce prequalified parts.”
The next machine, the Micro-SPS, can manufacture parts from roughly micrometer to centimeter scales and is also useful in understanding microstructural evolution. The Micro-SPS is used to determine bulk material sintering kinetics data. It does this by providing windows into the tooling to support real time X-ray and neutron radiography of bulk SPS processing.
The Center for Advanced Energy Studies at INL houses a bench-scale system designed for small specimens up to 20mm diameter. The machine is primarily designed to explore how SPS affects new materials, and to demonstrate the SPS process for academic and industry partners.
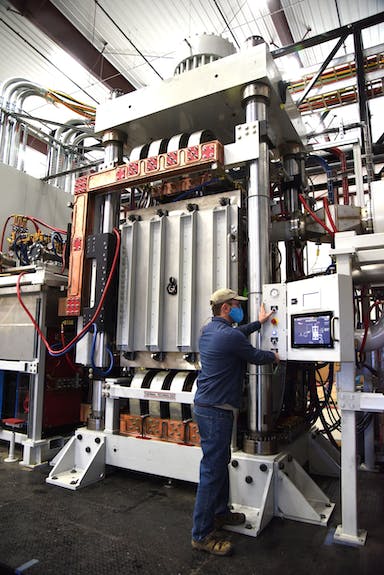
SPS is also an emerging technology for advanced nuclear fuels fabrication. The Radiological Spark Plasma Sintering System (RSPS) at INL’s Materials and Fuels Complex is a purposefully engineered system that is integrated within a radiological work glovebox.
Nuclear fuel fabrication and other highly air-sensitive work can be performed within the RSPS. A recent demonstration involved accident tolerant fuels and nuclear fuels fabricated for NASA’s Nuclear Thermal Propulsion applications. The demonstration used the RSPS to make materials that were then irradiated at almost 3000 K in INL’s Transient Reactor Test facility.
The DCS-800 is a larger SPS machine that can make parts up to about one square meter in size. Located at INL’s Energy Systems Laboratory, the DCS-800 operates at high power, high temperatures and high pressure, and is one of the largest machines of its kind in the world. It allows materials that have been discovered on the bench scale to be demonstrated at industrially relevant scales.
Finally, the Roller SPS will allow INL experts to spark plasma sinter continuous sheets of material from powders. That means they can make parts of unlimited size, while further decreasing the energy use and manufacturing time.
The real value to customers
While these machines form the core of INL’s SPS capabilities, the real value to users comes from INL’s extensive analytical and modeling capabilities.
Microscopy helps researchers peer at the microstructure of a part so they can understand how metal and ceramic powers evolve under different parameters such as temperature, pressure, current, voltage and time.
Experts can then use that experimental data to create models using tools such as INL’s Multiphysics Object-Oriented Simulation Environment (MOOSE) framework. Though INL’s computer scientists originally designed MOOSE to model how nuclear fuel performs in a reactor, the open-source software is flexible enough to simulate all kinds of physics problems from the movement of fluids through shale to electromagnetic wave propagation.
“The MOOSE team had already created the modeling framework that I need to understand the microstructure evolution during sintering,” Holland said. “Now we have experimental and modeling breadth that is unique in the world for understanding how the SPS process produces parts.”
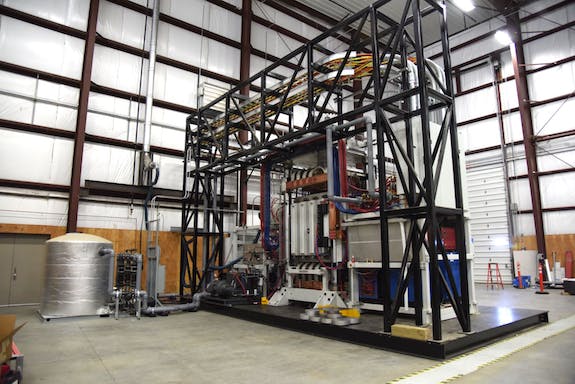
With computer modeling, INL’s SPS experts will be able to advise collaborators on the best process to meet their specifications without large numbers of real-world experiments that can cost hundreds of thousands of dollars each to perform.
“Our goal is to have the capabilities to couple models and experiments in a way that we can quickly and efficiently develop processes for our customers to implement themselves,” Holland said. “We don’t want to deliver parts. We want to deliver the process approach or a process design.”
Modeling allows Holland and his colleagues to specifically design and engineer a material’s property while also making a full-size sample.
“The sample has better properties, it was cheaper to make, and you can make it in larger sizes,” Holland said. “All of a sudden your cost per performance goes down. You can start to see cheaper, higher performing components available to the rest of the U.S. or the rest of the world.”
A comprehensive approach
Holland and his colleagues have developed a scientific methodology that sets INL’s SPS capabilities apart from similar efforts at other research facilities.
“What we’re bringing is wider capability and more awareness of manufacturing techniques and materials performance,” Holland said. “This comprehensive approach has never been done in the SPS community.”
The new SPS capabilities have clear benefits for INL’s nuclear science and technology research—where advanced materials must withstand corrosive, high temperature, high radiation environments. Yet those capabilities also have broad applicability across other research areas and industries outside of INL and the other national laboratories.
INL’s boasts distinctive expertise in the handling of high consequence, harsh environment materials. INL’s advanced SPS capabilities can help industry partners move from research to real-world use in industries such as mining, where improving the efficiency of manufacturing material for harsh environments, or in harsh environments, is crucial.
Likewise, INL can now help industry manufacture products from high-temperature materials such as tungsten, which has a melting point of 3422 C. With SPS, making products from high temperature materials can slash the cost of energy and materials. SPS reduces temperatures by as much as 50 percent and can reduce the energy cost ten-fold.
“This is a cross cutting capability that we’re developing,” said Robert O’Brien, INL’s Director of Advanced Manufacturing. “SPS touches everything from renewable hydrogen, advanced heat exchanger technologies, nuclear fuels and systems components, fuel pellets, reactor components and advanced moderator materials.”