Salt isn’t just for popcorn anymore. In fact, molten salt has caught the eye of the nuclear industry as an ideal working fluid for reactor cooling, energy transfer, fueling and fission product absorption. Many of the salts being considered are inexpensive, nontoxic, and easily transportable. In fact, table salt is one of the constituents many reactor developers are choosing to use.
Heightened interest in molten salt reactors (MSRs) has led to increased investment in their research and development. Idaho National Laboratory has already dedicated efforts to establish comprehensive molten salt capabilities. In the coming years, these efforts will establish a molten salt characterization facility, irradiate fuel salt and, for the first time, start up an experimental “fast” reactor that runs on molten salt.
“Molten salt research is essential for the future of nuclear energy, and INL is the ideal resource for industry projects in this area,” said Advanced Technology of Molten Salts Manager John Carter. “MSRs are an attractive option for future power generation, and we are prepared to make significant progress toward full-scale operations.”
Why salt?
Molten salt, as a coolant and nuclear fuel, offers numerous safety, efficiency and flexibility benefits.
Interestingly, molten salt fuel comes with an inherent safety feature. If the salt overheats, it naturally expands and makes the fission reaction less effective, which shuts down the reactor. The MSR reactor core naturally changes its power level to match heat removal for electricity production, allowing it to appropriately meet consumer demand.
Another benefit: fuel flexibility. Uranium, plutonium and thorium all form salts that can be used as fuel for MSRs. At reactor operating temperatures, the salt is liquid, which means new fuel can be introduced and in-use fuel can be cleaned, filtered and managed during operation. This eliminates the need for refueling outages.
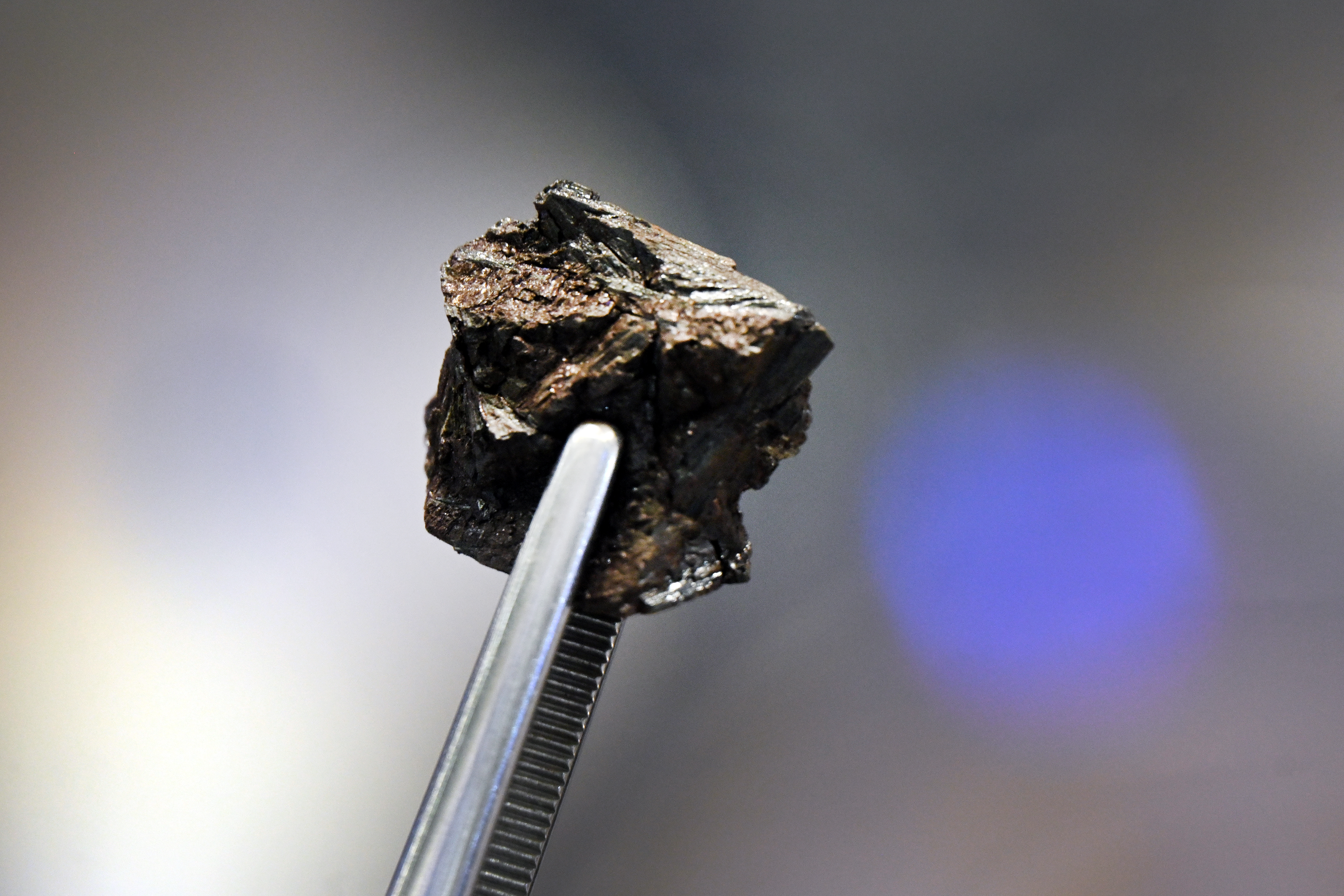
Molten salt fuel opens a whole new world of possibilities to reactor designers. The characteristically high temperatures in MSRs translate into efficient electrical power conversion, but the low-pressure feature eliminates the need for costly, thick-walled pipes and tanks.
The use of fast neutrons has its own set of benefits as well.
What are fast neutrons?
A fast-spectrum nuclear reactor uses fast, high-energy neutrons to sustain the nuclear reaction. Fast neutrons are more effective than slow neutrons at consuming certain waste products. This greatly reduces the amount of long-lived waste that must be isolated from the environment.
While fast-spectrum reactors can produce clean and reliable electricity for the grid, they can also provide thermal energy for industrial needs such as water desalination, aluminum and steel production, hydrogen production, and carbon capture. Today, those processes burn fossil fuels to generate high-temperature heat. Getting that heat from the power of fission instead would further reduce the globe’s dependence on carbon-based energy sources.
With these benefits in mind, the prospect of adopting a fast-spectrum, salt-based MSR design is a high priority for the nuclear energy industry, the United States and international governments.
What research is happening now?
INL researchers and engineers are helping answer some outstanding questions about MSR technologies.
For instance, as part of the Molten Salt Research Temperature Controlled Irradiation project, a Laboratory Directed Research and Development project at INL, researchers have designed the first fuel-bearing molten chloride salt irradiation experiment. This experiment places encapsulated fuel salt into an operating reactor to better understand how chloride fuel salt properties change during irradiation. The test is planned for later this year.
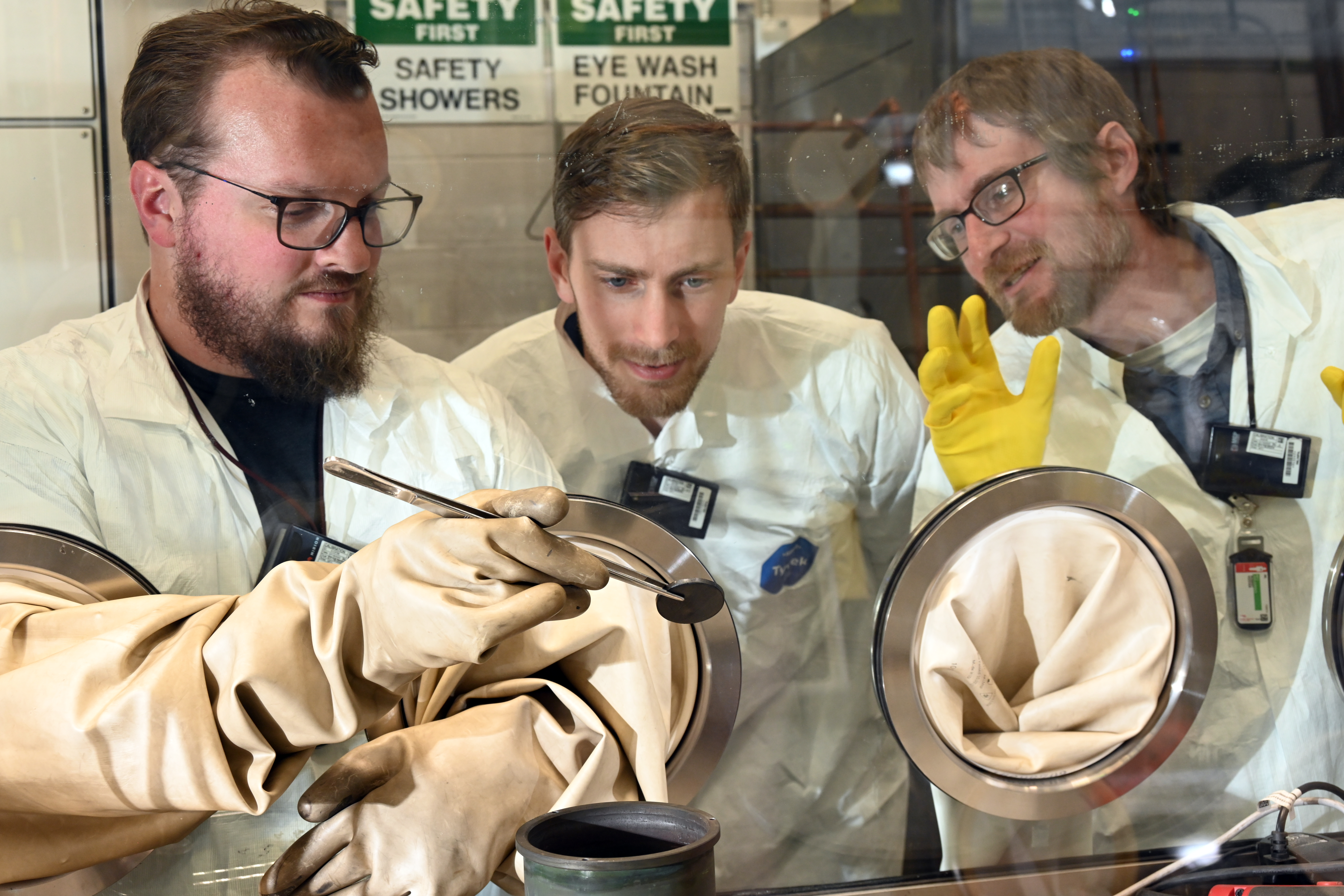
Another project, the Molten Salt Thermophysical Examination Capability, is a state-of-the-art facility where researchers will use specialized equipment inside a shielded glovebox to handle and closely examine irradiated fuel salt. Researchers hope to learn how materials will behave under operating conditions by observing their density, heat capacity and viscosity. The team should complete this National Reactor Innovation Center project next year.
INL is also part of a team developing the Molten Chloride Reactor Experiment (MCRE), a six-month sub-scale test that will demonstrate the first operational fast spectrum molten salt reactor in the world. In partnership with Southern Company and TerraPower, INL will synthesize and handle the fuel salt, load and operate the reactor, and perform all post-operation deactivation and disassembly work. The test-bed experiment, a public-private partnership under the Department of Energy Office of Nuclear Energy’s Advanced Reactor Demonstration Program, is expected to begin operation as soon as 2027 and will provide the data necessary to take the next step toward licensing a commercial Molten Chloride Fast Reactor.
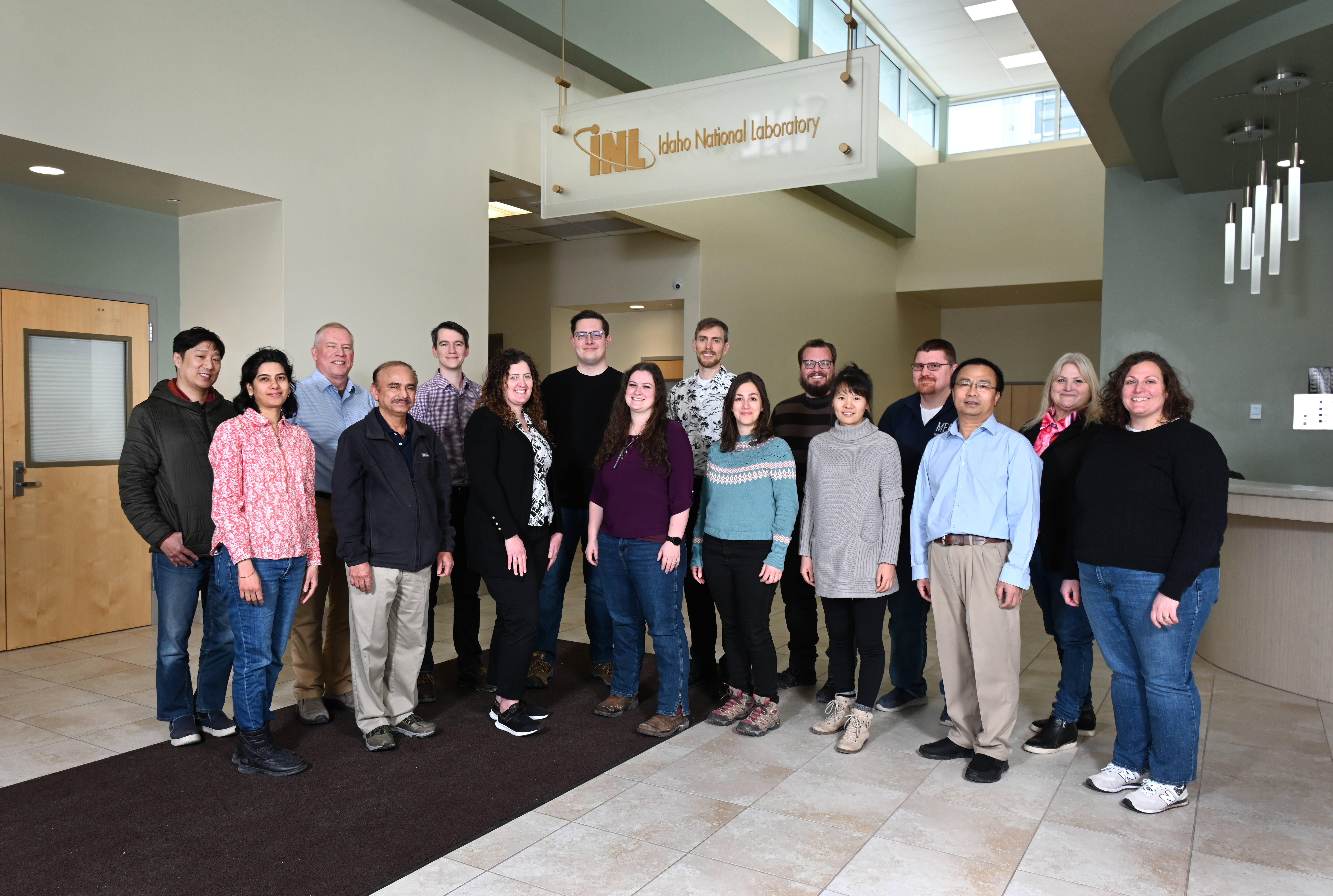
“It is incredible to see so much knowledge and talent come together for the MCRE Project” said Nick Smith, MCRE Project Director. “We are leveraging INL’s experience in fuel and reactor demonstrations, combining that with the innovative ideas and sense of urgency of our industry partners, and working through the engineering of a technology no one has ever built before. It is the most exciting thing I have ever been a part of.”
INL is also leading research related to molten salt properties, risk mitigation and MSR condition optimization with the help of dedicated computational modeling efforts.
Multiphysics computer modeling and simulations have been developed or customized specifically for MSRs using INL’s open-source Multiphysics Objected-Oriented Simulation Environment, or MOOSE, code. This application allows researchers to create precise digital models across multiple scales, materials and research areas. These high-fidelity simulations, informed by real-world experiments, help researchers and industry enhance MSR safety and performance by reliably predicting molten salt properties, thermodynamics and irradiation behaviors.
“The research activities going on at INL will help advance the technical readiness level of advanced molten salt reactors,” said research scientist Toni Karlsson. “INL has technical staff members with a passion for molten salts and unique experimental capabilities for actinide and irradiated salts not found anywhere else in the world. Along with industry partners, we are bridging the gap from advanced reactor development to deployment.”