Research underway at Idaho National Laboratory using 3D printing could be the beginning of applications that disrupt the nuclear industry.
Also called additive manufacturing, 3D printing produces some types of parts in less time and for less money. For the nuclear industry, 3D printing could overcome part supply challenges and enhance innovation by removing the constraints of traditional manufacturing.
INL, for example, recently benefited significantly from 3D printing. Additive manufacturing sped up component fabrication tenfold for a set of experiments and cut the cost as much as 90%, according to Daniel Wachs, national technical lead for fuel safety research at INL.
With additive manufacturing, the guts of a TREAT test module can quickly be adapted as needed for a new experiment. What’s more, the one-off nature of the manufacturing is well-suited to the current state of the art in 3D printing, which can quickly and inexpensively make a limited number of devices.
The approach of slowly and rapidly changing modules was implemented at INL’s Transient Reactor Test Facility (TREAT). Scientists use TREAT to conduct basic materials research, such as what happens to nuclear fuels exposed to abnormal reactor conditions. To do that, investigators need a test capsule that can provide information while meeting regulatory and safety requirements.
The research done at TREAT aids in the development of new, advanced nuclear fuels and next generation nuclear power plants, both of which must meet strict safety standards. Such ongoing research and development is important to the national electric grid because nuclear plants are a carbon-free source of power available at any time of day or night, in any kind of weather.
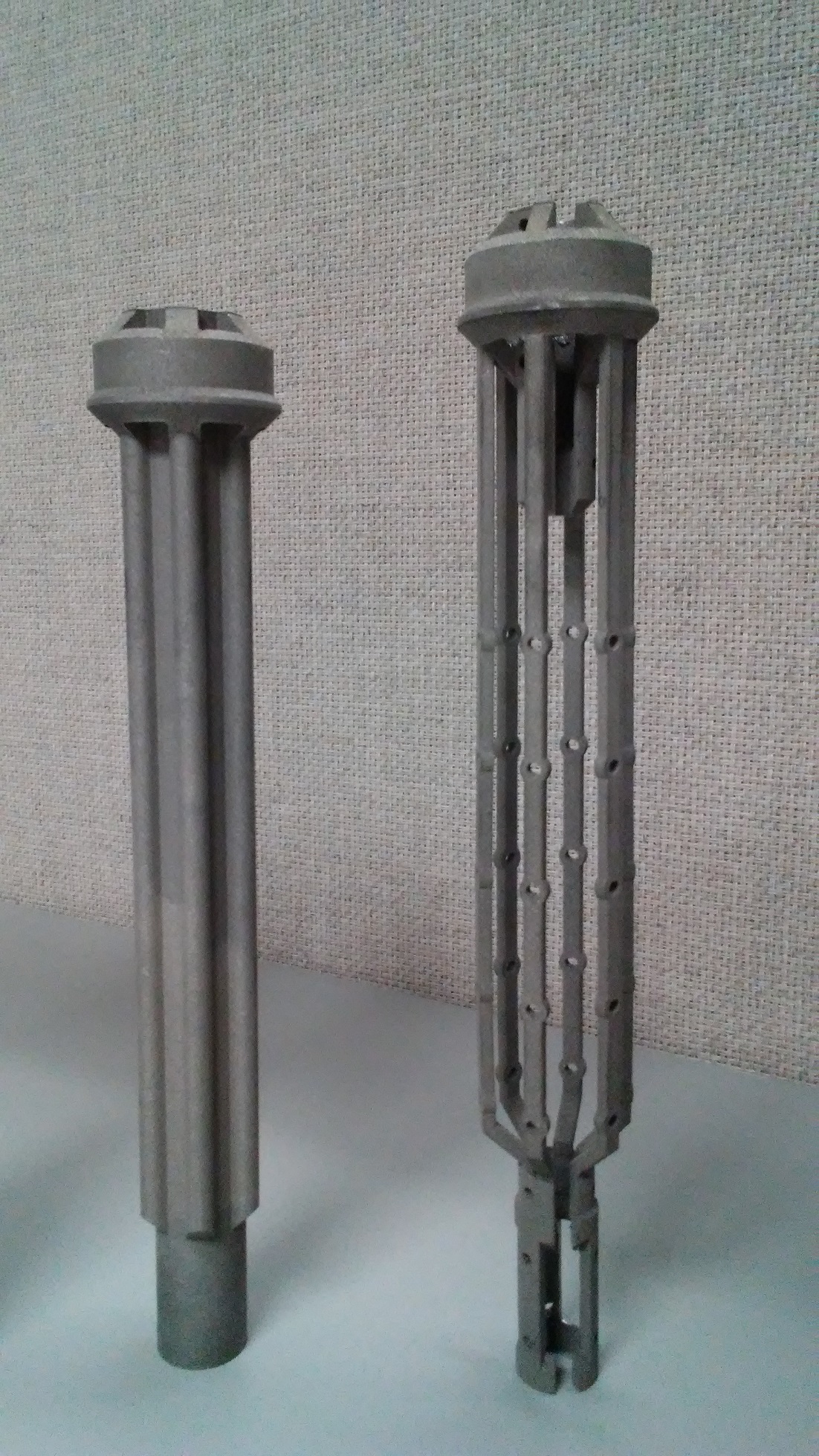
In INL’s use of additive manufacturing for TREAT research, the 3D printed interior goes inside a safety-rated and certified exterior. This outer module changes very slowly, does not have to be modified for every new experiment, and can be reused many times. This divide-and-conquer approach minimizes the time and money it takes to run an experiment and significantly reduces a hurdle to innovation.
“Historically, safety testing has been difficult and time-consuming and has always been a major barrier to new technology,” Wachs said.
3D printing and the splitting of the test assembly into two parts cut the cost to run a set of TREAT experiments at least in half and by as much as a factor of 10, saving hundreds of thousands of dollars. The two innovations also reduced the time needed to manufacture experiment components. Ten can now be done as quickly as one was before. The 3D approach has already been employed successfully in a test campaign, with more planned.
The additive manufacturing is done for INL by an outside contractor, using what is known as selective laser sintering, or SLS. This starts with a bed of metal powder, which in INL’s case is a standard commercial titanium-based alloy. Under computer direction, a laser traces a pattern over the powder, fusing it into a thin layer of metal. This process repeats as the desired part is built up layer by layer.
Additive manufacturing offers advantages over the traditional, or subtractive, approach. For instance, the final part may be significantly lighter, which is one reason why 3D printing is now being used in aerospace. Another advantage is that making a few parts the new way can cost less and take less time. A third benefit is that 3D printing can make parts that cannot be manufactured in a single piece by traditional methods. Because of this, the layer-by-layer approach can eliminate welds and joinery that may be weak points, Wachs said.
3D printing is still undergoing research and development. INL is working with national laboratories in Los Alamos and Oak Ridge to determine how best to inspect part manufacturing as it happens, using infrared cameras and other sensors. This could lead to ways to ensure parts are good as built, ending the need for post-production inspection.
“It could significantly reduce the time and energy that goes into building an acceptable part,” Wachs said.
Taking full advantage of additive manufacturing capabilities, though, requires engineers and scientists to rethink part function and how problems are solved. By using additive manufacturing, INL is demonstrating 3D printing’s potential and developing techniques industry can use. The expectation is the impact of the technology on the nuclear industry will grow as ingenious applications are developed.
“The innovation that will come out of it is going to be remarkable,” Wachs said.
Learn more about TREAT: https://factsheets.inl.gov/FactSheets/Transient_Reactor_Test_Facility.pdf
Learn about TREAT’s recent restart: https://inl.gov/article/inls-treat-reactor-successfully-completes-first-fueled-experiment/
Take a virtual tour of TREAT and check out other INL 360 virtual tours: https://inl.gov/360-tour-map/