Digital Engineering
Digital engineering describes a holistic approach to the design of a complex system: Design using models/data instead of documents, integration of data across models, and the culture change across project teams to realize significant risk reduction on construction cost and schedule.
In the modern world, megaprojects represent the sort of ambitious efforts that can change the world: better airplanes, integrated defense systems, new nuclear reactor systems. The benefits of such projects are enormous, but the challenges can be daunting.
Primary concerns are cost and schedule overruns. Undetected design errors can cascade into construction woes that can put a project over budget or behind schedule. Robust digital engineering helps prevent such calamities. By coordinating design, engineering and construction, the approach keeps cost and schedule on track while dramatically reducing overall program risk.
DID YOU KNOW? The cost to correct a defect during the conceptual design is 1,000x less than correcting a defect during operations.
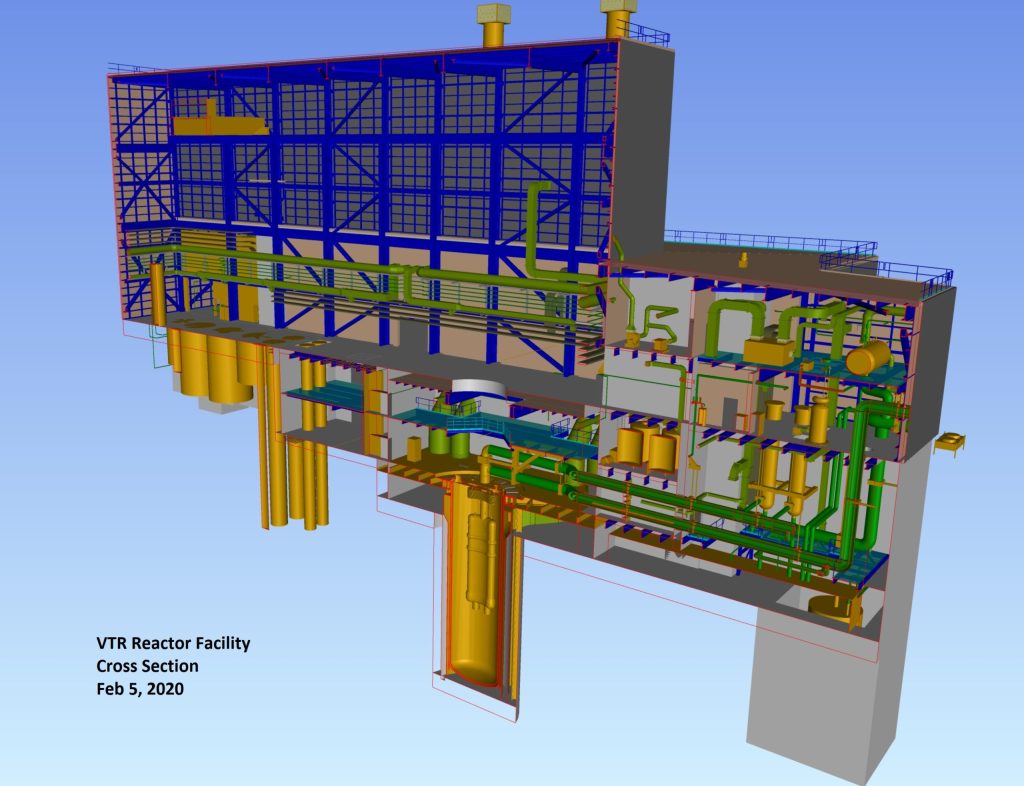
What is Digital Engineering?
Digital engineering (DE) embodies a deliberate approach to integrating information for the life cycle of a megaproject. DE uses digital information management systems to design, engineer, build, operate and maintain complex megaprojects.
Engineering teams can migrate to new digital engineering systems by developing new data models, data sharing methods, tool architectures and processes.
What industries use Digital Engineering?
DE is routinely used in aerospace, automotive and other industries to realize significant savings, quality and schedule improvements.
- Mortenson Construction realized a 600-day schedule savings and 25% productivity increase using virtual design and construction (VDC) technologies on more than 400 projects.
- By building digital twins for assets, systems and processes, GE has avoided more than $1.05 billion in customer, production and mechanical losses.
Are nuclear energy projects using Digital Engineering?
As first-of-a-kind commercial and test reactors are being planned in the United States, managing construction cost, timing and performance will be essential to maintain U.S. competitiveness.
As a result of proven benefits in other industries, Idaho National Laboratory launched a DE program in 2018 to support new reactor projects such as the Versatile Test Reactor (VTR).
The proposed 300-megawatt thermal, sodium-cooled fast reactor will support materials research and testing under closely controlled environmental conditions.
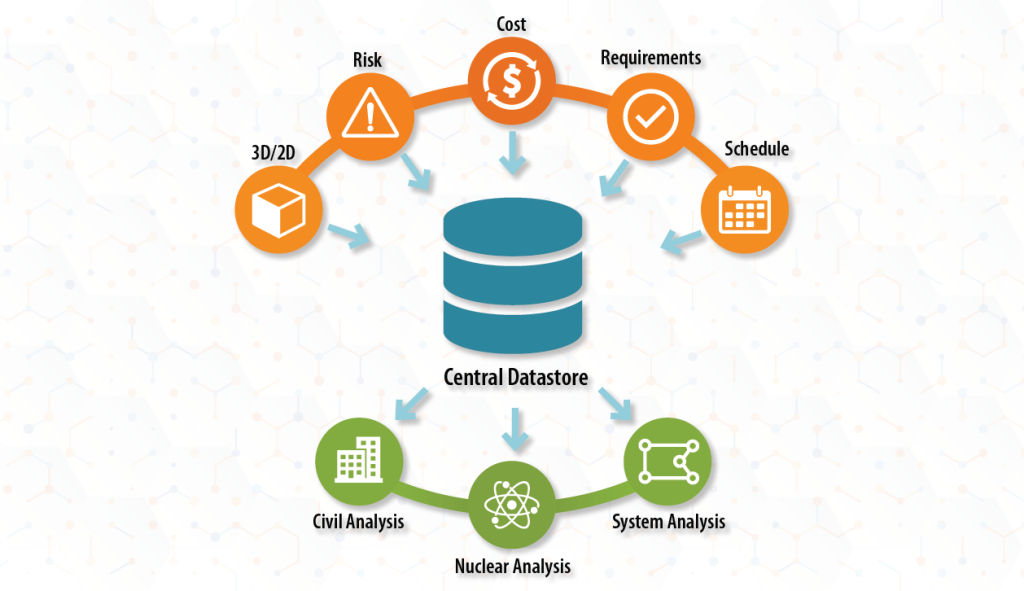
How are Digital Engineering advances shaping the VTR Project?
INL is implementing DE strategies to predict reactor performance and design issues early in the process, minimizing cascading risk. Numerous advances in the VTR design and engineering processes have already been achieved using DE.
Cloud-Based Collaboration
The VTR team has engineers across the United States using tools that demand a lot of computing power. INL’s new cloud-based platform allows real-time collaboration across geographic regions so that national laboratory, industry and university partners can access VTR information quickly and securely. This technology has reduced latency by a factor of 100 during peak use. The VTR is the first Department of Energy nuclear program using cloud computing to reduce technical barriers such as latency and computer performance.
Digital Modeling
A 3D model of the VTR was developed in the first three months of the project – 10 times faster than similar past efforts. For VTR, North Carolina State University developed a method to automate mesh creation for 3D modeling. The resulting 3D model makes it possible to automate seismic and pipe stress analysis, an industry first that will boost accuracy and efficiency.
Integrated Design & Construction
To capture integrated 2D and 3D models of the plant, the VTR uses a virtual design construction (VDC) and Building Information Management (BIM) tool from conceptual design through construction. A nuclear ontology (DIAMOND) connects object types across the nuclear construction discipline, allowing real-time access to how changes in construction will affect requirements. For example, project managers will be able to conduct near real-time reviews of how construction changes can affect seismic performance. The methodology will be applied to a broad set of performance factors.
Information Management
A tool that uses data to generate documentation has driven a culture change. The Requirements Information Management (RIM) tool helps ensure the requirements process is based upon essential information needs. The tool captures requirements, risks and tests in a fully integrated database to understand the full impact of changes. Research conducted at Virginia Commonwealth University will automate discovery of missing links, find incorrect object types and automate traditionally manual processes.
Integrated Modeling
Integrating modeling codes rather than running modeling and simulations independently can increase the efficiency of experimental design. TerraPower developed the Advanced Reactor Modeling Interface (ARMI) to enable such integration. This software framework will be integrated into the VTR’s DE databases through Colorado School of Mines and TerraPower research.
Download a copy of the fact sheet below.