Each day, roughly 43 million Americans eat at least one slice of pizza, according to experts. The hot, cheesy, Italian-inspired dish contributes a whopping $47 billion to the U.S. economy each year, and about a third of those pies come delivered to their destinations in corrugated cardboard boxes.
Even without the containers used for restaurant leftovers, that’s a lot of pizza boxes.
Unfortunately, like many other kinds of food containers, pizza boxes can’t be recycled because of all the contaminants left behind, like grease and cheese.
The contaminants particular to pizza storage are called FOGs, which stands for fats, oils and greases. FOGs like peanut butter in a jar or grease on a cardboard pizza box are next to impossible to fully remove.
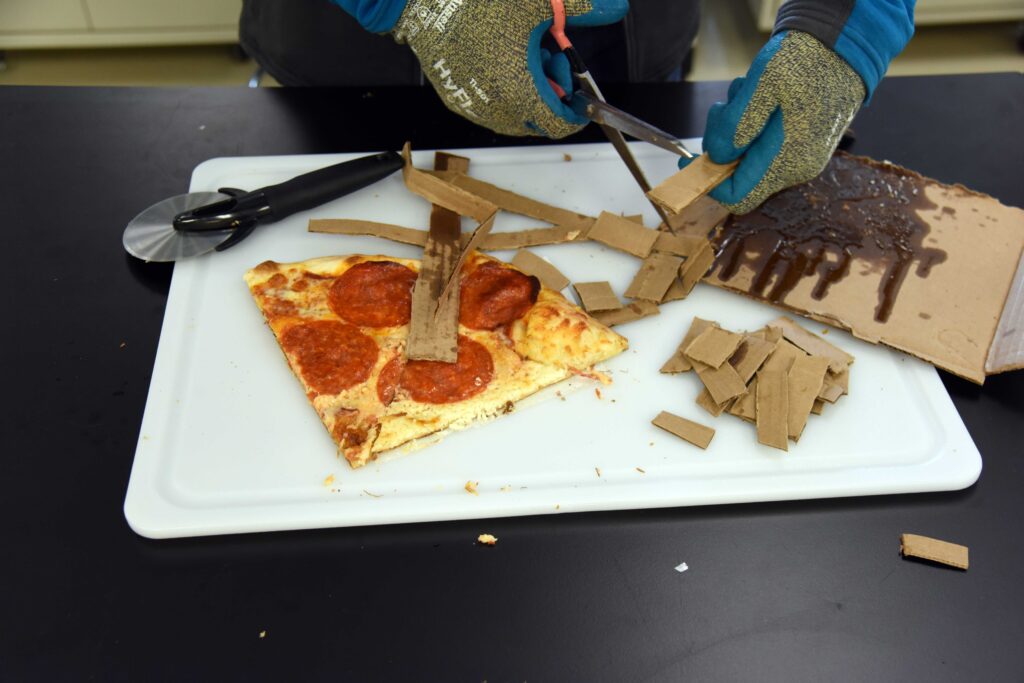
Now, pizza-loving researchers at Idaho National Laboratory (INL) are working to solve the pizza box-recycling problem. A recent study shows how to decontaminate cardboard using material separation capabilities.
The study could not only make one of the nation’s favorite foods more ecofriendly, it could also save the lives of U.S. soldiers.
The effort to separate grease, cheese and other contaminants from pizza boxes originated in a research project funded by the Defense Advanced Research Project Agency (DARPA) ReSource Program. ReSource was designed to turn warfighter waste, including common plastics, into edible macronutrients and other useful items. On the battlefield, every delivery to troops puts personnel at risk since supply runs can be as vulnerable as the frontlines to enemy attacks. These risky supply runs could be reduced if military bases could convert their waste into usable resources like fuel.
“Material separation will be important for reducing waste across the energy and defense industries,” said Aaron Wilson, the principal investigator for the pizza box experiment. “To make specific separations possible, we need to first prove the overall concept of material separations, which is what this study accomplished.”
So, Wilson and his team set out to prove a broader separation concept to enable success with the warfighter waste project.
Take the cheese out of the cardboard: The pizza box experiment
Wilson and his team created an experimental system using dimethyl ether (DME), an environmentally friendly chemical used in refrigeration processes, and a lot of pizza. The system features two vertical stainless-steel reactors — one to remove liquids from solids using a solvent and the other to remove the solvent from the liquids. A holding tank keeps the solvent separated until the experiment begins.
The team loads items they want to clean (in this case, broken down pieces of the contaminated carboard boxes) into the first reactor, then adds the solvent. Then, they mix the solvent with the cardboard boxes to trigger a chemical reaction that draws the contaminants out of the cardboard.
Once the cardboard is cleaned, the solvent is drained into the lower reactor. The team applies a vacuum to suck the DME solvent from the reactor up through a tube and either pumps it into a holding tank or back into the first cylinder to clean more material. At this point, the FOG contaminants, water and salts are concentrated as crystallized solids in the bottom of the second reactor. The FOGs and aqueous fraction separate from within these solids and can be easily collected.
“With the reactor process, we were able to extract the contaminants into separate fractions,” Wilson said. “We had a fraction dominated by oils, one dominated by water and one dominated with dryer solids.”
Why DME extraction?
This extraction process is a significant improvement over common water washing methods. As Wilson described it, water washing closely resembles soaking the waste that needs cleaning in a dishwasher and then drying the material at a high energy cost. This style of treatment results in a large volume of wastewater, generally equivalent to the volume of the material cleaned.
The wastewater contains a diverse mix of contaminants. Recycling that volume of wastewater and recovering the contaminants for disposal is such a complex process that no good option exists.
In contrast, the DME extraction process operates in a closed loop that recycles the DME solution to clean new waste items. The process can be scaled to any size.
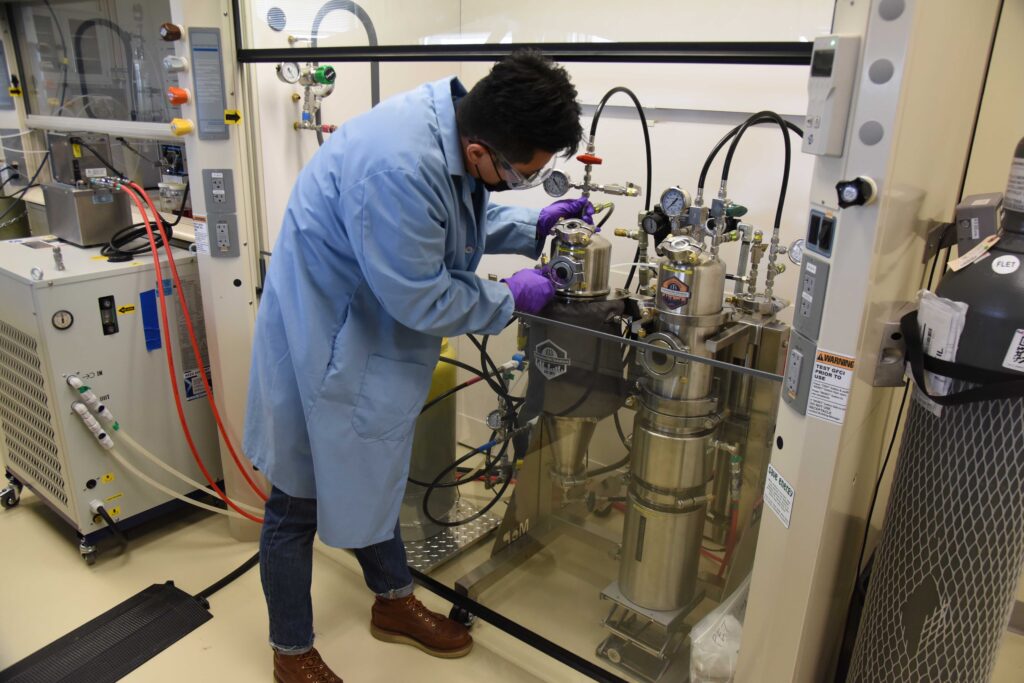
From pizza dinners to the battlefield: What’s next?
The success of the pizza box cleaning case study could enable future projects that convert waste into reusable materials, including the DARPA-funded project on repurposing military waste.
“Knowing that this works for the highly contaminated pizza boxes has helped validate the system for use in the battlefield,” said Jeff Lacey, the principal investigator for the DARPA project. “The biggest challenge now will be making the system lighter.”
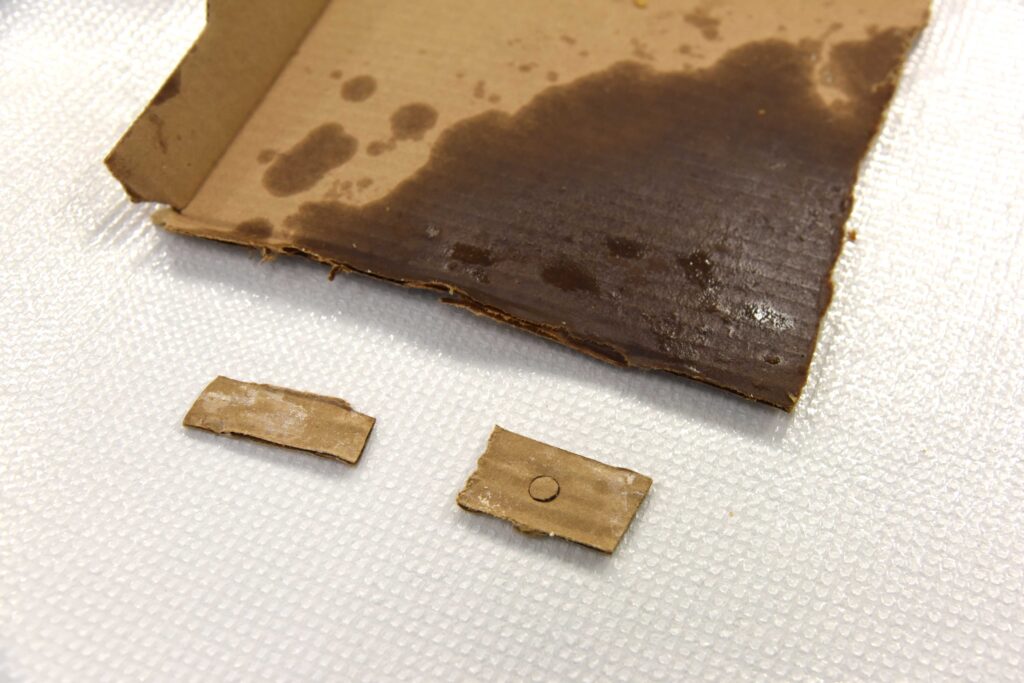
Since most military cargo must be transported overseas and across rough terrain, a lightweight system is crucial. Lacey and his team have begun identifying components that could be eliminated or replaced to reduce the reactor system’s weight. Some of the heaviest components were the pump for the DME holding tank and the two reactor vessels.
Researchers are evaluating lighter components, including solvent recovery pumps typically used in air conditioners that weigh 25 pounds compared to the 120-pound pumps used in the initial experiments. Lacey’s team is also exploring carbon fiber pressure vessels designed by a Brigham City, Utah, company for use by NASA, which reduce the reactor vessel weight from 60 pounds to 5 pounds.
The solvent extraction process also might prove useful for recycling batteries. It could enable more efficient battery waste disposal by separating the liquid intermediates from solids. Ultimately, the project contributes to the sustainable idea of a circular economy, because all the materials used to extract one volume of waste can be reused in the next waste extraction process.
“INL started with this pizza box case study because most people care about properly recycling food waste,” said Lacey. “But ultimately, this research has so many possible applications for national security and a net-zero future.”
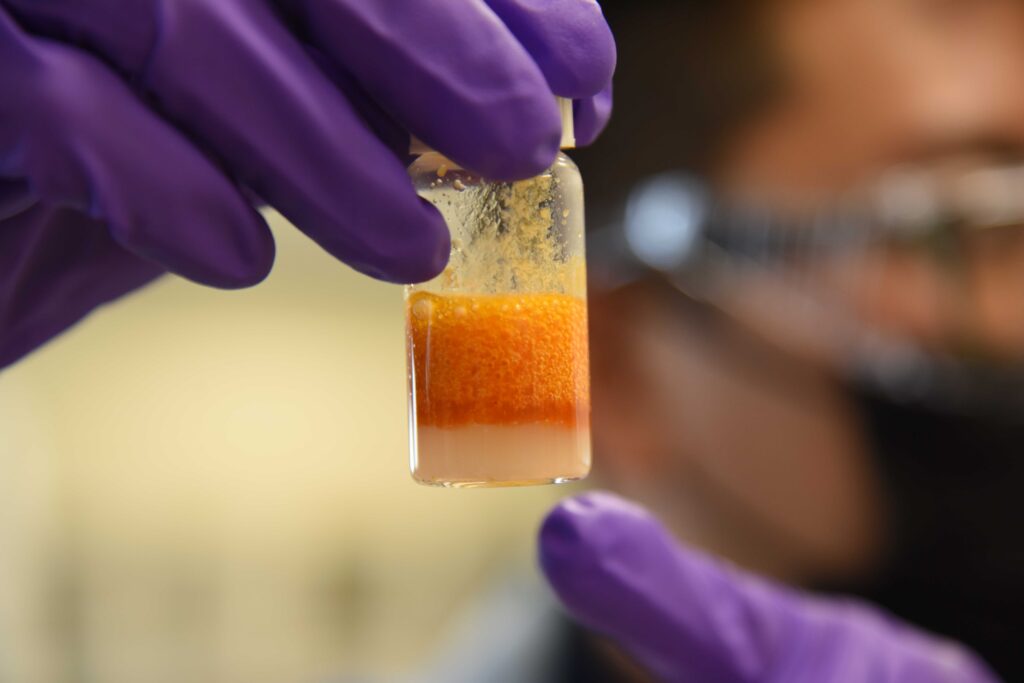