Scientific progress is anything but automatic. The path to new discoveries is not a straight line. But while the route to nuclear energy breakthroughs may be circuitous, automated solutions can enhance the efficiency of the research process and get to the innovation a little sooner.
For example, Kamrynn Schiller, an Idaho National Laboratory nuclear research facility engineer, has designed a robotic system to support post-irradiation examination work at INL’s Irradiated Materials Characterization Laboratory (IMCL).
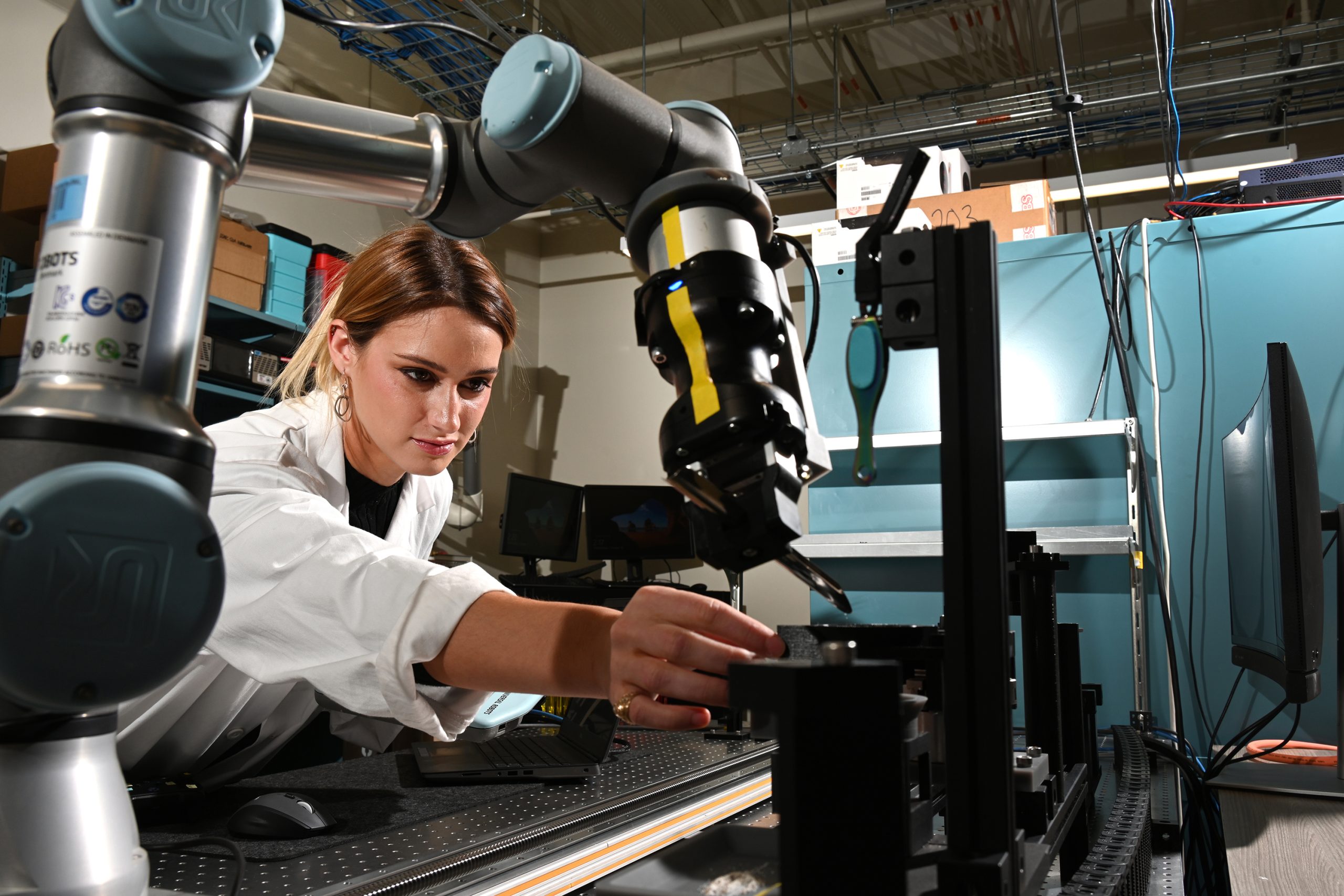
IMCL is home to an impressive array of highly sophisticated analytical instruments, with capabilities ranging from transmission electron microscopy to atom probe tomography. Researchers use its capabilities to examine irradiated materials – such as samples of nuclear fuel or its protective cladding – at the microstructural level to figure out why they responded to irradiation in particular ways. The data generated from this work is vital to ongoing efforts to develop advanced nuclear fuels and reactor materials.
The robotic arm automatically positions samples within a hot cell according to both the sample attributes and the type of examination being performed. This tool was developed on an off-the-shelf platform known as UR3e. The arm can lift up to 3 kilograms and has been developed to handle samples within a glovebox housing instruments for thermophysical property measurements. To this point, most glovebox and hot cell work has been performed with manipulators – manually controlled mechanical claws that can take months of training and are somewhat cumbersome to use.
“We first had to determine if the robot would be capable of doing the work we had in mind for it, so we tested its capabilities with pieces of a straw as well as salt to see if it could handle granular samples,” said Schiller. “We started with basic movements and expanded the repertoire from there, with more specialized tooling and more precise programming to retrieve specimens.” The robot can operate autonomously or be manually controlled by a researcher, she added.
Schiller is a relatively new hire who joined INL in late 2020. She graduated with a bachelor’s degree in mechanical engineering from Tarleton State University and is pursuing a master’s degree in mechanical engineering at Texas Tech University.
“I thought the job posting sounded interesting and wanted to take on a fun challenge outside of my wheelhouse,” said Schiller. “I did not have prior experience with nuclear science but really liked the idea of supporting this kind of research.”
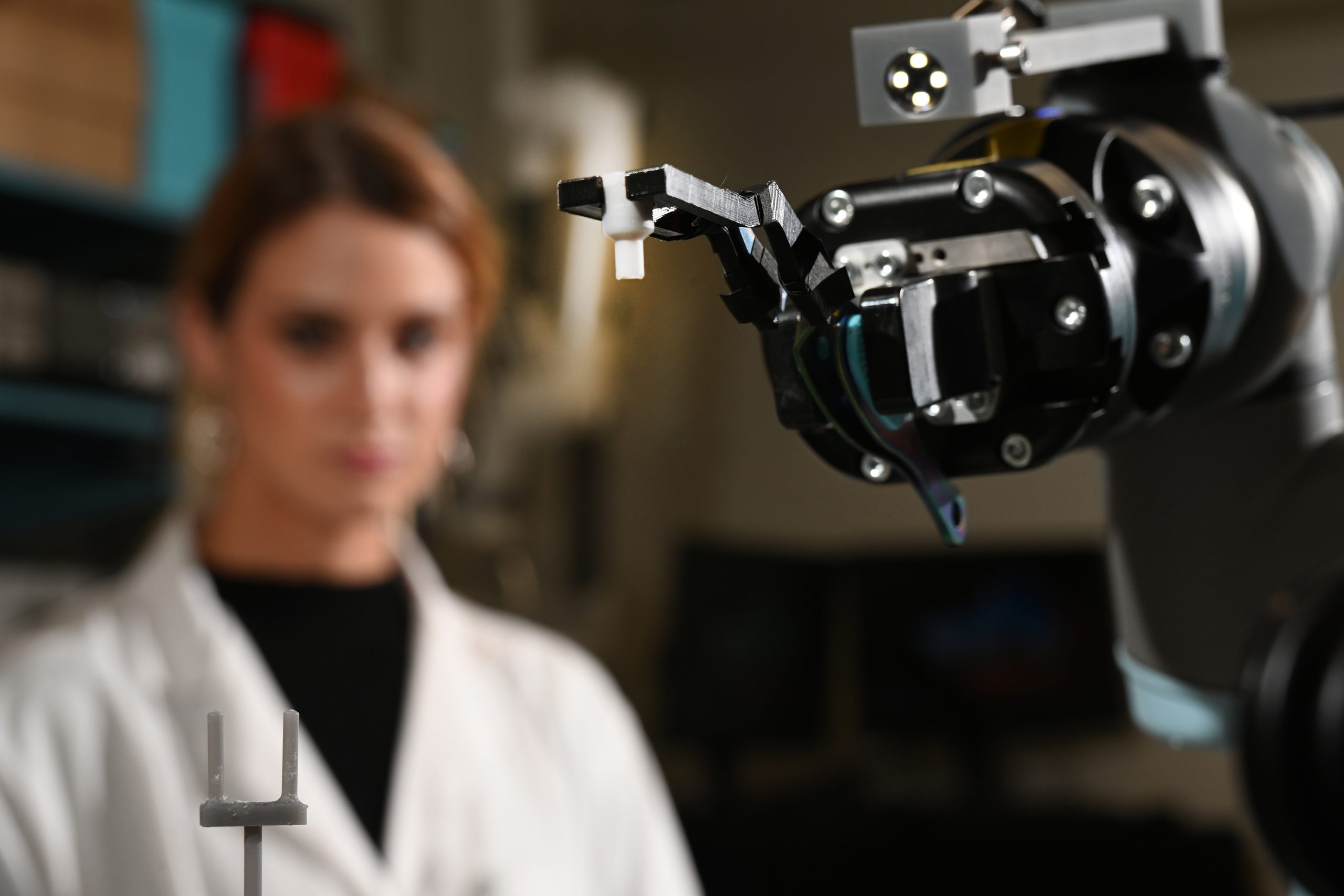
To configure the robot, Schiller utilized a series of kinematic equations to determine how it moves, whether in a straight line, along the path of least resistance or via arced motions. She programmed a series of waypoints to allow the robot to perform specific functions, further customizing the system to accommodate a range of sample types.
“One of the challenges in developing this tool was the uncertainty as far as what exactly the robot would be handling, so I tried to account for a wide variety of potential samples as I built out the programming,” said Schiller. “There was a definitely a learning curve to figure out how to program the tool as I had never worked with this kind of robot before, but ultimately I was able to develop a flexible, dynamic tool that is well-suited for numerous applications.”
This tool is playing an important role in research at IMCL and helping lay the groundwork for the automated capabilities that will be a cornerstone of operations at the Sample Preparation Laboratory (SPL), which is under construction and scheduled to begin research activities in 2025. SPL will significantly expand INL’s post-irradiation examination capacity, serving as a dedicated facility for nonfuel materials such as cladding and structural components. When complete, it will rely heavily on robotic systems like the one Schiller developed.
“The lessons learned from the design of the IMCL robot have been indispensable to the ongoing development of robotics for SPL,” said Schiller. “It’s an exciting time to work at INL and I’m grateful for the opportunity to contribute to such important research.”