Lithium-ion batteries have led to a revolution in consumer and industrial electronics that has paved the way for a wireless future with fewer carbon emissions.
Yet the lightweight, rechargeable energy source for everything from cellphones to electric vehicles poses one big environmental challenge: How do you dispose of a battery once it’s no longer useful?
Simply throwing it into a landfill is both dangerous and wasteful. Fires can start when bulldozers run over batteries while moving earth and debris. Plus, dead batteries contain valuable elements such as cobalt, lithium and manganese—at higher concentrations than can be found in commercial ores.
Recycling, therefore, could potentially be a big business, one that grows along with the electric vehicle fleet. Experts say that by 2040 there will be 500 million electric passenger vehicles on the road worldwide (almost a third of the predicted passenger fleet). By then, the value of the raw materials in end-of-life lithium-ion batteries will have grown from about $0.3 billion in 2020 to $1.1 billion by 2025 and nearly $24 billion by 2040.
Recycling with less heat and chemicals
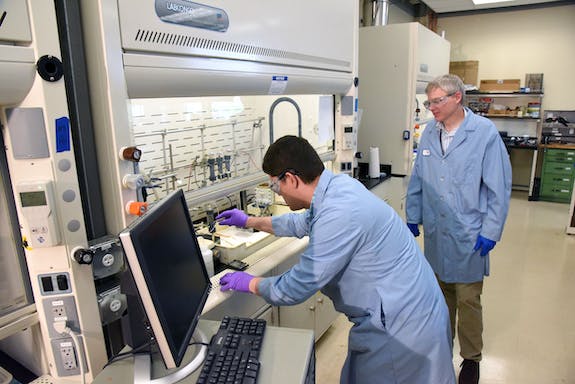
In light of these growing challenges and opportunities, Idaho National Laboratory (INL) aims to make the recycling of lithium-ion batteries easier, more efficient, and potentially greener. Encouraging results of these efforts recently appeared in the journal Resources, Conservation and Recycling.
Recycling can strengthen the supply chain for battery manufacturers by reducing the need to depend on potentially unreliable sources for new materials. That’s why the research was funded by the Department of Energy’s Critical Materials Institute. One goal of the institute is to diversify the supply of critical energy materials, partly through reuse and recycling.
Today, only an estimated 5% of lithium-ion batteries are recycled. That is, to a degree, because the process is partly manual, involves high temperature and caustic chemicals, and is inefficient, according to Tedd Lister, an INL staff scientist and paper co-author.
In their paper, the researchers reported proof-of-principle for a different approach to battery recycling, one that works at room temperature and significantly reduces the use of chemicals.
High efficiency at a lower cost
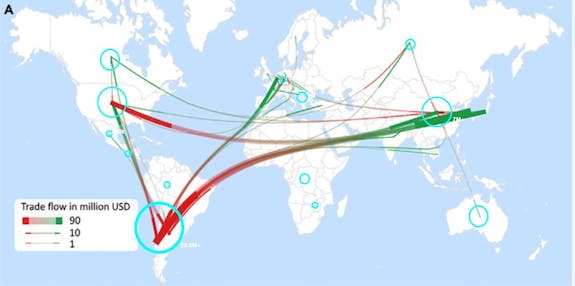
Credit for graph from Joule 1, 229–243, October 11, 2017.
The new process is electrochemical, Lister said. So, instead of heat, the energy comes from electricity, which powers the reactions that leach the cobalt, lithium, manganese and other materials out of the batteries. The researchers demonstrated the approach in a cell that measures a few inches on the side, small enough to be picked up.
The scientists started with shredded lithium-ion batteries, with material supplied by Retriev Technologies of Lancaster, Ohio. A battery recycling and management company, Retriev also participated in the research, as did Solvay, a Brussels-based company that supplied the chemicals used for metals separation.
After developing the electrochemical process, the scientists tested it out, finding they could achieve high recycling recovery rates. They reported over 96% efficiency in terms of extracted cobalt, lithium, manganese and nickel, which exit the process in a single output stream. In contrast, copper — a metal with high commercial value — deposits on the cathode, which simplifies the downstream separation process, Lister said.
A preliminary cost analysis indicated a roughly 80% reduction in energy and chemical costs as compared to present recycling techniques.
What’s next?
Future plans include developing an electrochemical procedure to separate the leach process output into cobalt, lithium, manganese and nickel. The team is also exploring reuse for another critical material, graphite, that is left over and can potentially be recycled.
Both the leaching and separation processes then need to be scaled up to a size that is useful in an industrial setting. Part of this effort will include optimizing the leaching and separation processes by tweaking parameters to improve performance and efficiency. In addition to project partner Retriev, INL scientists are interested in working with commercial partners on these next steps.
Finally, this type of battery recycling could make use of the excess energy sometimes produced by utility-sized electricity plants.
“You are using the energy to make a product that will later be used to produce energy,” said Luis Diaz Aldana, the paper’s lead author and an INL electrochemical engineer/scientist.