For the bioeconomy to continue expanding, biomass must be produced and converted into biofuels in a cost-effective way.
In September, Idaho National Laboratory (INL) bioenergy researchers helped meet those cost challenges by reducing the modeled cost of growing, harvesting, storing, transporting and preprocessing biomass from $149.58 per dry ton to $82.86 per dry ton.
The modeled feedstock cost is lower than a U.S. Department of Energy (DOE) Bioenergy Technologies Office (BETO) performance goal of $84.45 per dry ton from harvest to the biorefinery reactor throat, including the grower payment. A similar change in crude oil prices between 2008 and 2010 shrunk gasoline prices by more than $1/gallon, according to data from the U.S. Energy Information Administration.
“We have been working on this for five years,” said Kevin Kenney, director of INL’s Bioenergy Program. “To see technical targets met that seemed to be such a stretch is rewarding.”
The challenge arises from the fact that converting raw biomass to bioenergy requires a number of steps to create a stable, consistent feedstock for biorefineries. In particular, preprocessing steps such as grinding, drying, pelleting, roasting and chemical treatments can make biomass more uniform, easier to handle and easier to convert to biofuels or energy, but also add significant costs.
INL researchers were able to exceed the cost target milestone thanks to the combined efforts of three different BETO-funded projects – fractional milling and high moisture pelleting, intelligent and adaptive controls, and modeling that assesses biomass cost, availability and blending.
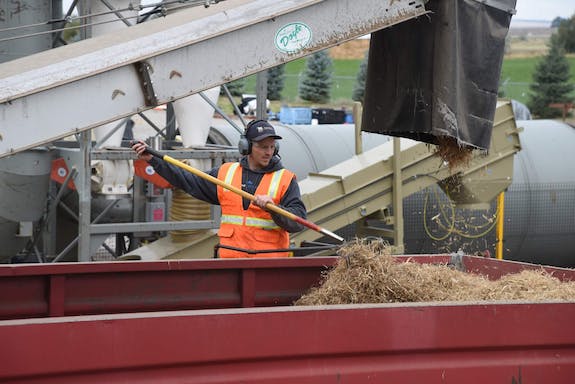
Two significant technical accomplishments – high moisture pelleting and factional milling – resulted in lower energy usage and greater than 50 percent cost reduction in biomass preprocessing.
INL researcher Jaya Tumuluru developed a high-moisture pelleting process for various high-moisture feedstocks such as switchgrass, corn stover, lodgepole pine and municipal solid waste.
The high-moisture pelleting process eliminates the energy-intensive rotary drying stage. Instead, high-moisture biomass goes through two grinding steps and enters the pellet mill at moisture contents higher than 26 percent. Friction created from the compression and extrusion of pellets from the pellet die reduces biomass moisture content to roughly 20 percent.
Compared with standard pelleting methods, Tumuluru reduced the overall preprocessing cost of pelletized biomass by 35 to 40 percent using biomass with moisture contents ranging from 26 to 39 percent. Those savings include a roughly 55 percent reduction in operating energy costs and a 35 percent reduction in capital costs.
Likewise, INL engineer Neal Yancey used a flat orbital screen to separate biomass particles less than a quarter inch from larger particles destined for the stage two grinder. This “fractional milling” reduces energy costs during preprocessing because smaller-sized material that already meets particle size specifications doesn’t go through an additional, unnecessary grinding stage.
During tests conducted in September, Yancey used fractional milling to divert more than 40 percent of the material after stage one grinding.
Yancey not only reduced energy usage at the stage two grinder by 40 percent, but he also increased the throughput of the system by 80 percent compared to conventional grinding of high-moisture corn stover.
Fractional milling also reduces the amount of fine particles produced during stage two grinding because smaller-sized material is spared additional size reduction. This creates more uniform particle size entering the pellet mill, which allows the mill to operate more efficiently.
Another solution that helped reduce delivered feedstock costs was a combination of “least-cost formulation” and blending of different biomass types in a scenario where depots are used to supply biomass to the biorefinery.
Least-cost formulation is a model that researchers use to determine where biomass is available and how much that biomass would cost. The model helps make sure that the biomass meets quality specifications set by the biorefinery by taking into account key biomass characteristics such as carbohydrate, ash and moisture content. The model also assesses biomass based on the cost of individual biomass types that comprise a blend, including individual grower payments and transportation costs to the biorefinery.
Blending biomass lowers grower payments by combining high-quality, high-cost feedstocks with lower-quality, low-cost feedstocks. The resulting blended feedstock is designed to meet carbohydrate, ash and other quality specifications for conversion at the biorefinery.
Researchers achieved a 46 percent reduction in grower payment, an 18 percent reduction in harvest and collection costs, and a 94 percent reduction in dockage costs – the penalties imposed when biomass doesn’t meet specifications – when applying least cost formulation and blending strategies with depots in an analysis of data from the 2016 Billion Ton Report.
The depot concept locates biomass preprocessing depots in high-yield areas where biomass costs less because of an abundance of supply. The depot grinds, blends and densifies biomass into pellets or briquettes before the feedstock is sent to the biorefinery.
In turn, the biorefinery is not as dependent upon having a source of biomass nearby, and can instead be located near resources such as utilities, rail lines and labor.
Depots increase the radius and therefore the supply of available biomass, lowering grower payments by 46 percent, according to the analysis, which is the first of its kind to document the cost benefits of depots.
For more information about Idaho National Laboratory’s bioenergy team, visit https://bioenergy.inl.gov/SitePages/Home.aspx.