In the future, the biggest breakthroughs in aerospace and elemental energy will likely result from thinking small. Really small. Whether it’s rocket engines or fusion reactors, advances in these technologies require new materials equipped to handle their extreme operating environments. Making materials that can withstand intense pressures and temperatures requires advanced manufacturing techniques that can precisely manipulate a material’s microscale structures.
To address this challenge, a diverse group of Idaho National Laboratory researchers has teamed up to create the MOOSE Application Library for Advanced Manufacturing UTilitiEs, or MALAMUTE, a simulation code designed to connect the microscale behavior of materials with their engineering-scale performance for a variety of advanced manufacturing processes.
A SPARK OF INSPIRATION
MALAMUTE is the newest framework to build on the laboratory’s Multiphysics Object-Oriented Simulation Environment, or MOOSE, which allows researchers to create precise digital models across multiple scales, materials and research areas. MALAMUTE is the first MOOSE application to focus on simulating advanced manufacturing techniques, and the researchers hope their simulation code will accelerate development of cost-effective, high-performance and environmentally sustainable materials for nuclear and non-nuclear applications.
Although MALAMUTE is meant to simulate a variety of advanced manufacturing techniques such as laser welding and 3D printing, its first application is to model a technique called electric field assisted sintering (EFAS). Also referred to as spark plasma sintering, the technique uses a strong electric field to consolidate a metal or ceramic powder into a solid form.
EFAS has been used to research materials used in the aerospace and nuclear industries for decades because it has been shown to create many unique high-performance materials.

EFAS has been used in the aerospace and nuclear industries for decades because it allows manufacturing systems with unusual geometries using a wider variety of high-performance materials.
“Whenever you’re trying to create a difficult to process or unique alloy composition, sintering techniques, including EFAS, are often part of the conversation,” said Casey Icenhour, an INL graduate fellow and lead of this project. “There are a lot of interesting things you just can’t create with traditional manufacturing processes.”
By fine-tuning the ways electric fields are applied to a powder, manufacturers have more precise control over the materials they’re working with, which allows them to use a broader range of materials and geometries. But to leverage the full potential of EFAS, researchers need a better understanding of how it affects materials on a micro (i.e., under 1 millimeter) and macro (i.e., greater than a millimeter) scale. That’s where MALAMUTE comes in.
SMALL SCALES, BIG IMPACT
Prior to MALAMUTE, researchers studying advanced manufacturing techniques such as EFAS had limited insight into how these techniques affected the properties of a material. They could run simulations that modeled the material at engineering scales (i.e., full-scale), and microscales (i.e., individual grains of powder), but they struggled to connect these simulations to show how the material changed across scales.
Five teams of researchers participating in INL’s Laboratory Directed Research and Development program recognized there was enough overlap in the advanced manufacturing simulation techniques they were studying to justify a more comprehensive and collaborative approach. In 2021, they came together to create MALAMUTE, which is designed to be a “plug-and-play” approach to multiscale modeling for a variety of advanced manufacturing techniques.
“One of the things we’re really trying to build into MALAMUTE is a modular ethos that allows us to look at different manufacturing techniques,” said Stephanie Pitts, a computational scientist with INL’s Computational Mechanics and Materials Department. “That way we can look at how to make materials fast and energy efficient while still having the microstructure that we need to meet the performance requirements for that part.”
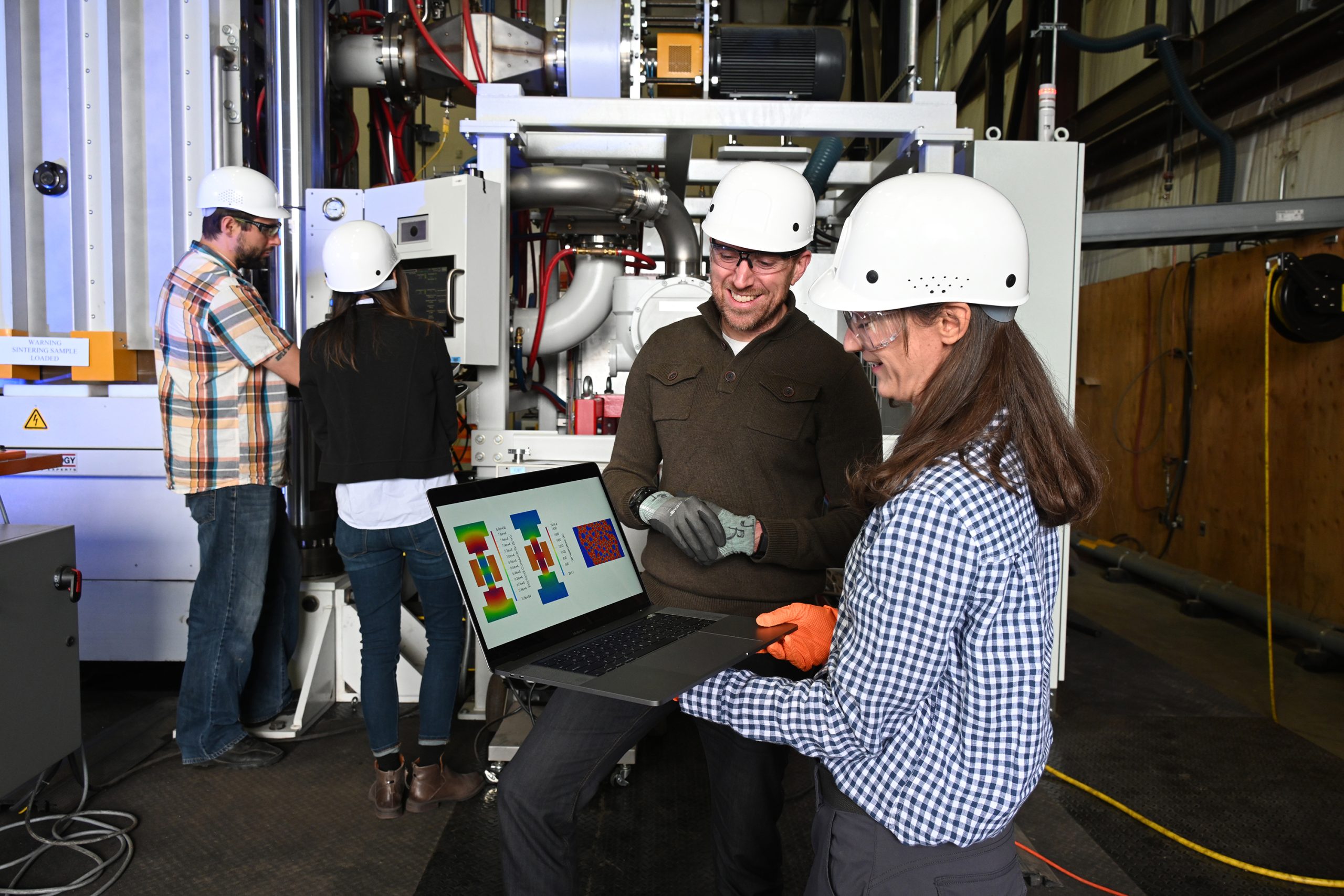
Multiscale modeling is where the cutting-edge work in materials science is happening today and is widely recognized as the key to developing novel materials that will drive breakthroughs in nuclear and non-nuclear technologies. MALAMUTE is the latest addition to INL’s growing library of application-specific multiscale simulation apps. It will provide experimentalists with a powerful new tool for understanding advanced manufacturing techniques as it moves out of its prototype phase.
“If a researcher wants to learn more about the experiment they’ve just run, they can take this modeling tool and use it to know more about the physical processes that are happening on a deeper level,” Icenhour said.
To continue their work, the team plans to leverage data from INL’s Direct Current Sintering-800, the largest EFAS machine of its kind in the world.
Earlier this year, NASA’s Ames Research Center established a Government Use Agreement with INL to become the first user of the MALAMUTE platform. The collaboration will allow researchers in NASA’s in-space manufacturing program to model sintering and other advanced manufacturing techniques in a zero-gravity environment. The agreement builds on a previous collaboration using MOOSE and an open source sintering model developed by Sudipta Biswas, an INL computational scientist.
This summer, Biswas coauthored a paper with several NASA researchers demonstrating the potential of using the MOOSE simulation environment and her open source sintering code to model sintering in a microgravity environment. She hopes MALAMUTE’s specialized focus on advanced manufacturing techniques will provide deeper insights into how materials respond to these processes across a range of scales – both on Earth and in space.