Nuclear power plants are complex, depending on intricate mechanical, electrical and nuclear systems to maintain safe and efficient operation. The power plant buildings also must be built to exacting standards, making their construction challenging.
It isn’t just nuclear power plants that are difficult to build. According to consulting firm McKinsey, 98% of all megaprojects – those that cost $1 billion or more – suffer cost overruns of more than 30% and nearly as many, three in four, are behind schedule by at least 40%.
Now, a new collaboration aims to improve the management of complex construction projects by generating a digital twin of an actual one. A digital twin is a virtual representation of a physical object that helps identify potential problems and understand performance. North Carolina State University is leading the collaboration, and Idaho National Laboratory is contributing nuclear facility expertise, digital twin frameworks and data from the Sample Preparation Laboratory. A nuclear technology laboratory under construction at INL’s Materials & Fuels Complex, the Sample Preparation Laboratory will be a state-of-the-art facility for analyzing irradiated materials.
Using drones to get the picture
“We are flying drones around the construction site on a regular basis, and we are capturing imagery of the facility. We are comparing that to the building information management model, or BIM,” said Christopher Ritter, director of INL’s Digital Innovation Center of Excellence.
“The drones take overlapping 2D imagery that we can turn into 3D data,” added Christopher Forsgren, a geospatial analyst who’s leading the data capture project at INL. A ground-based laser scanner provides data for those locations where the drones cannot.
Such information about what a building looks like is called “as-built” data. Traditionally, gathering these measurements required expensive and slow laser scanners, which meant they were not often used for construction management purposes, said Kevin Han, project lead and assistant professor of Civil, Construction and Environmental Engineering at NC State University.
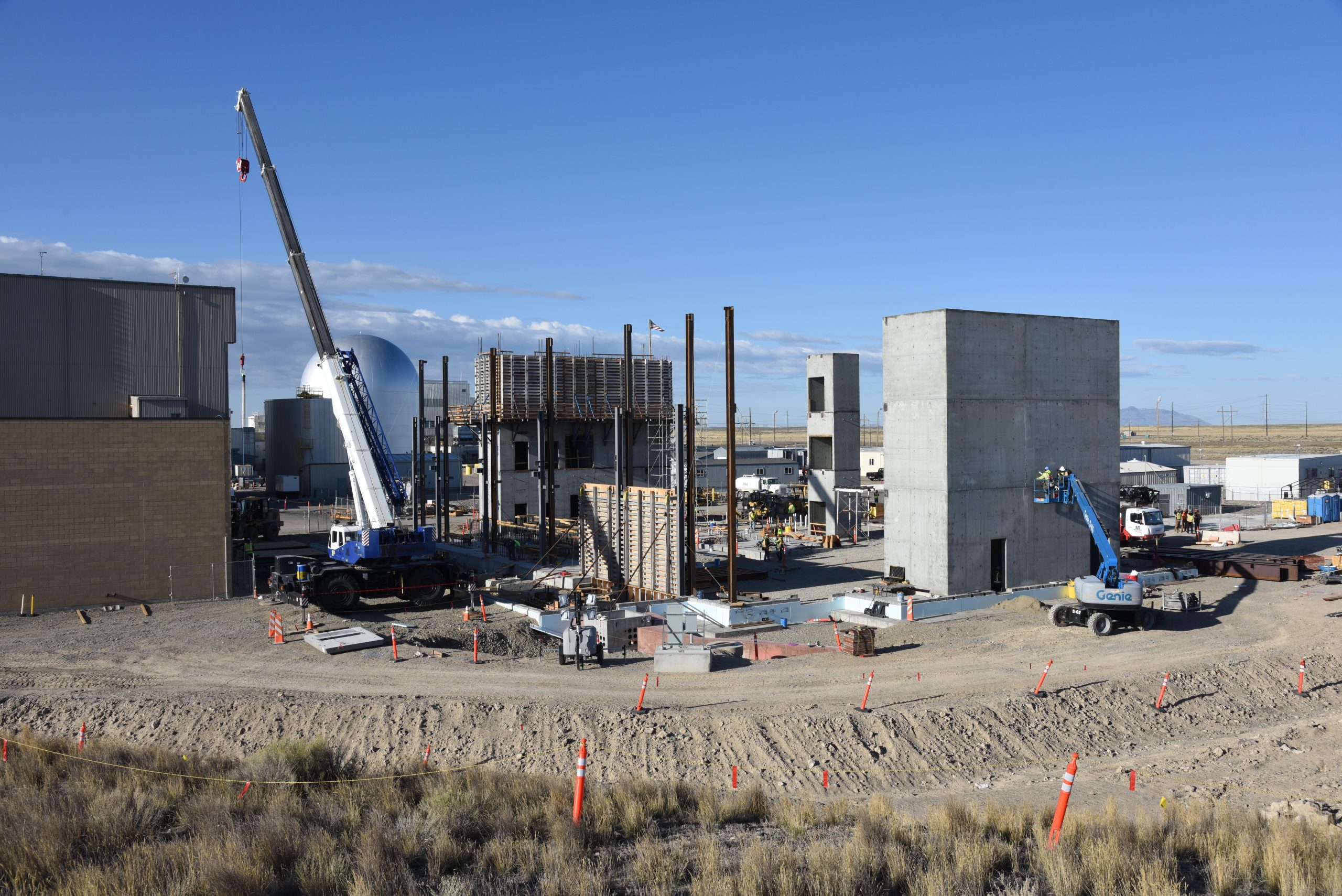
“Before it was all subjective without visuals when it comes to communicating construction progress,” Han noted.
One observer, for instance, may look at a reinforced concrete wall being built and decide it is 30% done. Someone else, on the other hand, may conclude it is 50% complete. Without objective as-built data for verification, either number could be correct or both wrong.
Also, the potential for mistakes lurks in every step that involves people transcribing and transmitting these numbers. Any inaccuracies can add to cost, put a project behind schedule, or do both.
There are also prefabricated components to consider, Han pointed out. Often, it is more efficient, cheaper and faster to make part of the building in a factory because prefabrication can take place in a controlled setting out of the weather. Fabricators can then ship the component to a project site, and the construction crew at the site finishes the component, if required, and assembles it into the building. But if the as-built facility is different than it was planned to be, then the component may not fit, costing time and money while the component is redone or modified to account for the difference.
With the data captured by INL drones, the researchers at NC State have a digital twin of the building. This digital replica of the real-world object can be used to check that components fit, the building is on schedule, and it matches the plans.
The data may also someday be used in a way that takes advantage of other research done by the group at NC State. They developed machine learning tools that use computers to analyze images to detect building materials and predict construction progress. In another application, machine learning spotted safety hazards in real time from images taken by wearable cameras. Drone imagery could be used in either application.
Benefits beyond initial construction
Accurate as-built information is also important for later upgrades and retrofits. Exact information about the thickness of a concrete wall, for instance, could make cuts into that wall more precise. Such detailed data could improve cost estimates if additions or changes are made.
What’s more, accurate as-built data is important when sites are decommissioned. Knowing with certainty what’s hidden from sight and encased in concrete or other construction materials can play a vital role in deciding how to take apart a building.
Such a digital twin can also help when operating a building. Smart buildings, for instance, use sensors, actuators and controllers to adjust hourly air exchanges and temperatures to match the number of occupants. This approach minimizes energy use while maximizing comfort. Data like that being gathered in the NC State/INL project can make a digital twin more accurate, thereby improving modeling and simulation of building operational strategies and ultimately reducing ongoing costs.
The researchers at NC State have used this technology to capture as-built data for office buildings, but the project with INL allows them to test the concept on a more complex structure. Han said the data capture part of the project should be finished by late 2021 or early 2022. Although the building under construction at INL will not be complete by then, the technique will have been applied to an actual nuclear research facility – a real-world test to demonstrate the usefulness of the approach.
The eventual cost savings of the technology could be substantial, according to Ritter. While manufacturing productivity has doubled in the last 40 or 50 years, the construction industry has gotten less efficient due to the need to meet more stringent regulations and other factors, he said. Thus, it is critical to deploy and validate methods to change that trend.
“We’ve got to do a better job. We’ve got to figure out a better way to do it,” Ritter said of complex construction projects.
The joint project between NC State and INL could prove to be one of the tools that will make this turnaround happen, benefiting the nuclear energy industry and others.