INL researchers are working with industry partners on an innovative method of producing advanced nuclear fuels that improve the attractiveness of new nuclear plants as reliable, emission-free baseload energy.
As part of a DOE accelerated technology commercialization project, INL’s Dr. Isabella Van Rooyen and Dr. Clemente Parga worked with Westinghouse’s Ed Lahoda to develop an innovative process for producing uranium silicide (U3Si2) fuel for advanced reactors.
Their process was dubbed AMAFT – short for Additive Manufacturing as an Alternative Fabrication Technique – for nuclear fuel. Although the process was designed around U3Si2 fuel, it can be applied to other fuels. U3Si2 fuels hold potential as an improved advanced fuel with greater safety benefits due to its greater density and improved thermal conductivity when compared with traditional uranium dioxide (UO2)-based fuels used in most current nuclear power plants. Both of these characteristics can help improve fuel cycle economics and greater safety margin in off-normal situations.
Additive manufacturing processes, more commonly known as 3-D printing, are used to form objects by adding layer upon layer of a feedstock material. Such processes involve less waste material and can be faster than traditional fabrication techniques in which objects are formed by removing material from a larger piece of feedstock material.
“AMAFT technology uses a novel hybrid additive manufacturing process, which means we combine some traditional and some additive manufacturing processes to reduce the number of steps – and therefore the time and cost – involved in producing fuel for power reactors,” said Isabella Van Rooyen, a distinguished staff scientist in INL’s Fuel Design & Development department.
In the AMAFT process, a novel hybrid laser engineering shaping technique is used in a series of processes to create a small localized melt pool from multiple powder sources, allowing the direct formation of a pellet of dense U3Si2 fuel.
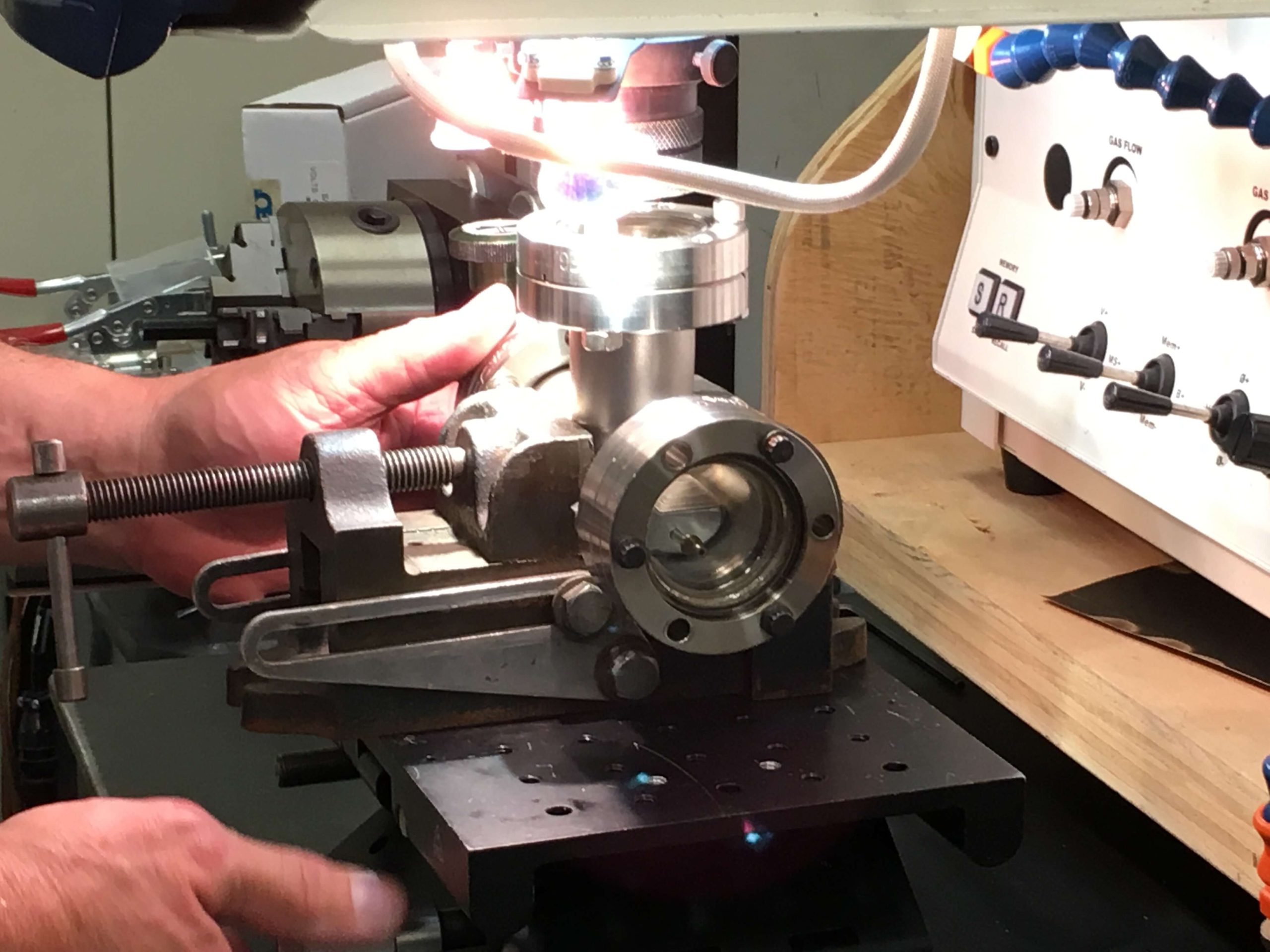
Traditional fuel manufacturing methods require several steps to convert raw uranium ore into UF6, and then again into the UO2 that will be used in the final fuel for a light-water reactor.
Van Rooyen explained that the AMAFT process can reduce steps from the traditional fabrication method that requires preprocessing of UF6 to convert it to UO2. AMAFT can start with any uranium-based feedstock, which opens up the supply chain and eliminates the conversion steps. In addition, the team is working to make AMAFT easy to scale – which is another big requirement for commercial viability.
This hybrid process, in combination with other advanced manufacturing processes, provides much greater flexibility for fabricators, including the capability to use multiple raw material sources.
Van Rooyen and Parga were joined by University of Florida Ph.D. candidate Jhonathan Rosales, who performed various characterization activities on the development products. Another set of benchtop experiments is underway on surrogate material utilizing a benchtop pulsed laser supported by INL researchers David Swank and DC Haggard.
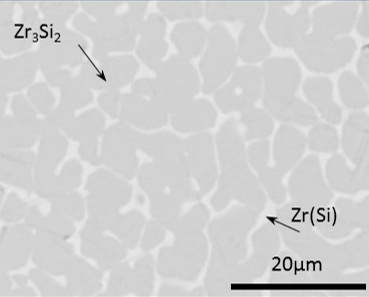
In addition to the technical development of the novel AMAFT fabrication process, the team has accelerated the commercialization process by participating in DOE’s Energy I-Corps initiative, a program intended to foster a more entrepreneurial mindset among researchers at DOE laboratories.
The Energy I-Corps program pairs DOE researchers with industry mentors as they work to refine their concept to support potential customers’ specific needs. The AMAFT Energy I-Corps team consisted of Isabella van Rooyen (principal investigator), Dr. George Griffith (entrepreneurial lead) and Ed Lahoda (industry mentor).
“It was a surprise to learn how critical partnerships would be to the overall commercialization process. We need partners to help with qualification, standards, process development and characterization,” Van Rooyen said. “Energy I-Corps was an opportunity to think outside the box from our normal everyday research mindset.”
The team’s participation in the Energy I-Corps program not only helped accelerated the AMAFT concept’s commercial readiness, but the 75 industry interviews have been helpful in the development of INL’s rapidly growing advanced manufacturing strategy.