After two decades, laboratory reopens for spent fuel testing
On a chilly December evening in eastern Idaho, a semi-tractor trailer truck pulls off the desert highway and up to the gate at the Department of Energy’s Materials and Fuels Complex.
The truck and the small, gray shipping container that sits on its trailer appear unremarkable. But the shipping container is sturdier than most, with extra-thick metal, a heavy door and a lid that lifts off the top. There’s also a Department of Transportation placard on its side that reads “radioactive.”
The truck pulls up to the gate, and Idaho National Laboratory employees embark on a flurry of paperwork. After some time, the truck pulls through the gate and into a narrow bay attached to the Hot Fuel Examination Facility (HFEF).
On the roof of the bay, thick metal rails, painted yellow, serve the cranes that remove the shipping container’s precious cargo: next-generation nuclear fuel rods that could eventually power the U.S. reactor fleet. The fuel rod technology could save electricity rate payers millions of dollars per year while increasing a nuclear power plant’s resilience under potential accident conditions.
But first, INL researchers must subject the fuel rods to several years’ worth of examinations and experiments to prove their performance and safety.
Powering the current fleet
Experts say maintaining the current fleet of nuclear reactors in the U.S. is essential to limiting the major impacts of climate change and meeting net-zero emissions goals by 2050.
That’s because the 93 nuclear reactors currently operating around the country provide roughly 50% of the nation’s carbon-free electricity.
To keep today’s reactors operating safely and efficiently — and to prepare for tomorrow’s advanced reactors — researchers from industry, universities and national laboratories have developed new nuclear fuels that last longer and are more resistant to accidents.
The Nuclear Regulatory Commission (NRC) requires a rigorous qualification process to make sure these fuels perform as designed. That process includes subjecting prototype fuel rods to years of real-world operating conditions in test reactors and commercial nuclear power plants. Afterwards, researchers conduct experiments and analyses on these samples to thoroughly understand the prototype’s performance characteristics.
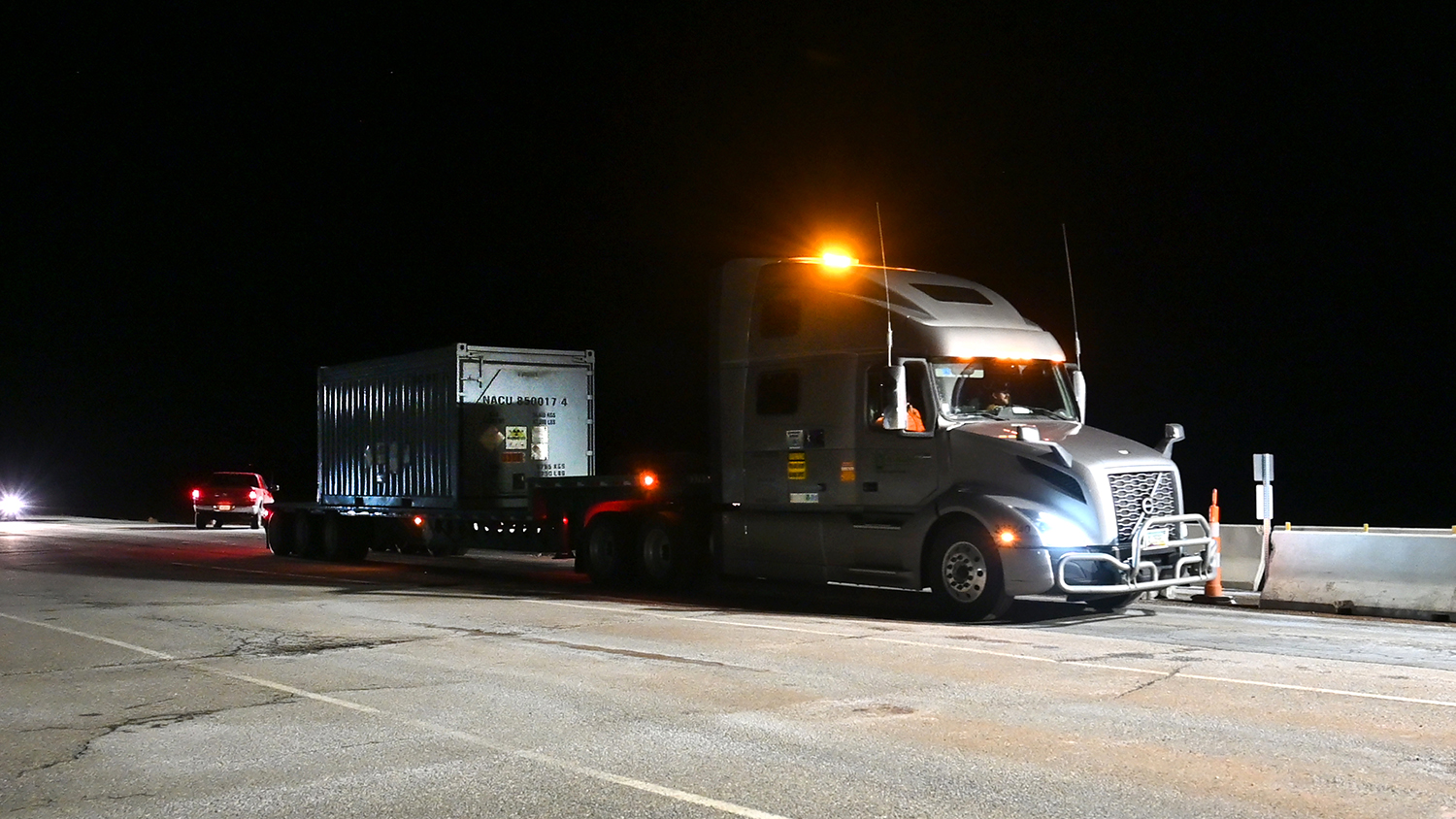
Now, for the first time in two decades, INL has received a shipment of used next-generation fuel from a nuclear power plant for post-irradiation tests and examination. In December, INL received 25 prototype fuel rods irradiated in the reactor core of a commercial nuclear plant.
The fuel rods were developed and manufactured by Westinghouse Electric Company with technical assistance from several national laboratories, including INL.
Each fuel rod is 12 feet long and the shipment includes about 100 pounds of heavy metal, mostly uranium.
“It’s exciting for INL to be open for business again to collect this kind of information,” said Josh Jarrell, an INL researcher who serves as the Department of Energy (DOE) senior technical advisor for nuclear fuels. “Bringing this material to INL will help move the nuclear industry forward and demonstrate that INL can be a partner. Similar shipments and data collection in the future will ensure our current reactor fleet is using the most advanced and economical fuels that they can.”
Accident tolerant and high burnup fuel
The fuel rod shipment consists of accident tolerant fuel and high burnup fuel. Industry has designed accident tolerant fuels that offer better safety performance during normal operations, power spikes and postulated accident scenarios. High burnup fuels have advanced materials that could increase the electricity output of existing power plants and extend operating cycles, resulting in more efficient use of uranium resources.
Accident tolerant fuels are designed with special claddings and chemistries. The advanced claddings are designed to tolerate higher temperatures than the claddings of conventional fuel rods while containing the fission products, a wide spectrum of lighter elements (some radioactive) created when a uranium atom fissions. The zirconium alloy cladding on the Westinghouse fuels is coated with a very thin chromium-based layer that protects against corrosion during normal operations and high temperature oxidation under accident conditions.
The ceramic uranium pellets inside the cladding of some accident tolerant fuels is doped with other materials that “soften” the pellet and can reduce the risk of damaging the cladding or the fuel itself while also retaining gaseous fission products.
Likewise, next-generation high burnup fuels represent the next step in an evolution that began 30 years ago, said Daniel Wachs, national technical director of DOE’s Advanced Fuels Campaign.
During that time, “the utilization of the fuel has nearly doubled from 30 gigawatt-days (of energy) per metric ton of fuel to about 50 GW-days per metric ton,” Wachs said. “We expect the same growth curve out of these technologies, but that requires a strong partnership between industry, the national labs and the NRC.”
Indeed, researchers expect this new fuel technology to increase utilization limits to as high as 75-85 gigawatt-days per metric ton or more. Operating cycles — the amount of time a plant can operate between refueling — could increase from 18 to 24 months. “That is a huge economic benefit to those plants and the ratepayers,” Wachs said. “The increased electrical output of the U.S. commercial fleet could be the effective equivalent of adding new reactors to the fleet without any new construction.”
Examinations and experiments
INL researchers will subject the prototype fuel rods to a series of tests to analyze their physical and chemical characteristics, understand how they perform under accident conditions, and determine their behavior during storage and recycling.
The examinations and experiments conducted for accident tolerant and high burnup fuels will have specific technical objectives, as the fuels rely on slightly different technologies, said Fabiola Cappia, the post irradiation examination department manager at INL. Cappia will lead the team that performs the examinations of the fuel rods from the Byron Shipment.
“For the two different fuel types, we’re looking to address different data gaps for industry,” she said. “Some of the (post irradiation examination) techniques will be applied in a similar way to all the rods and then, as we proceed through the experimental campaigns, the analyses become experiment-specific.”
Much of the work will take place at INL’s HFEF — the world’s largest inert-atmosphere hot cell — located at INL’s Materials and Fuels Complex.
The cranes in the HFEF bay will remove the lid from the shipping container, then carefully remove a cask with the fuel rods. The cranes will then lower the cask through a big yellow door in the floor and into a tunnel that leads into the hot cell. From the tunnel, the fuel rods will be raised into the hot cell and maneuvered into position for examination.
Just outside the argon-filled room, experts use remote manipulators to analyze the fuels through specially designed 4-foot-thick windows that protect them from radiation.
“We have the ability to receive full-length rods and to do post irradiation examination of the material at all scale lengths — from highly detailed to macro-scale,” Jarrell said.
First, researchers will perform non-destructive examinations on the fuel rods, including a visual inspection; gamma scanning, a technique that measures gamma activity (a residual effect of fission events) to identify any gaps, depressions or other characteristics within the fuel rod; and profilometry, a process that determines the dimensional changes to the rod that occurred during irradiation within the Byron reactor core.
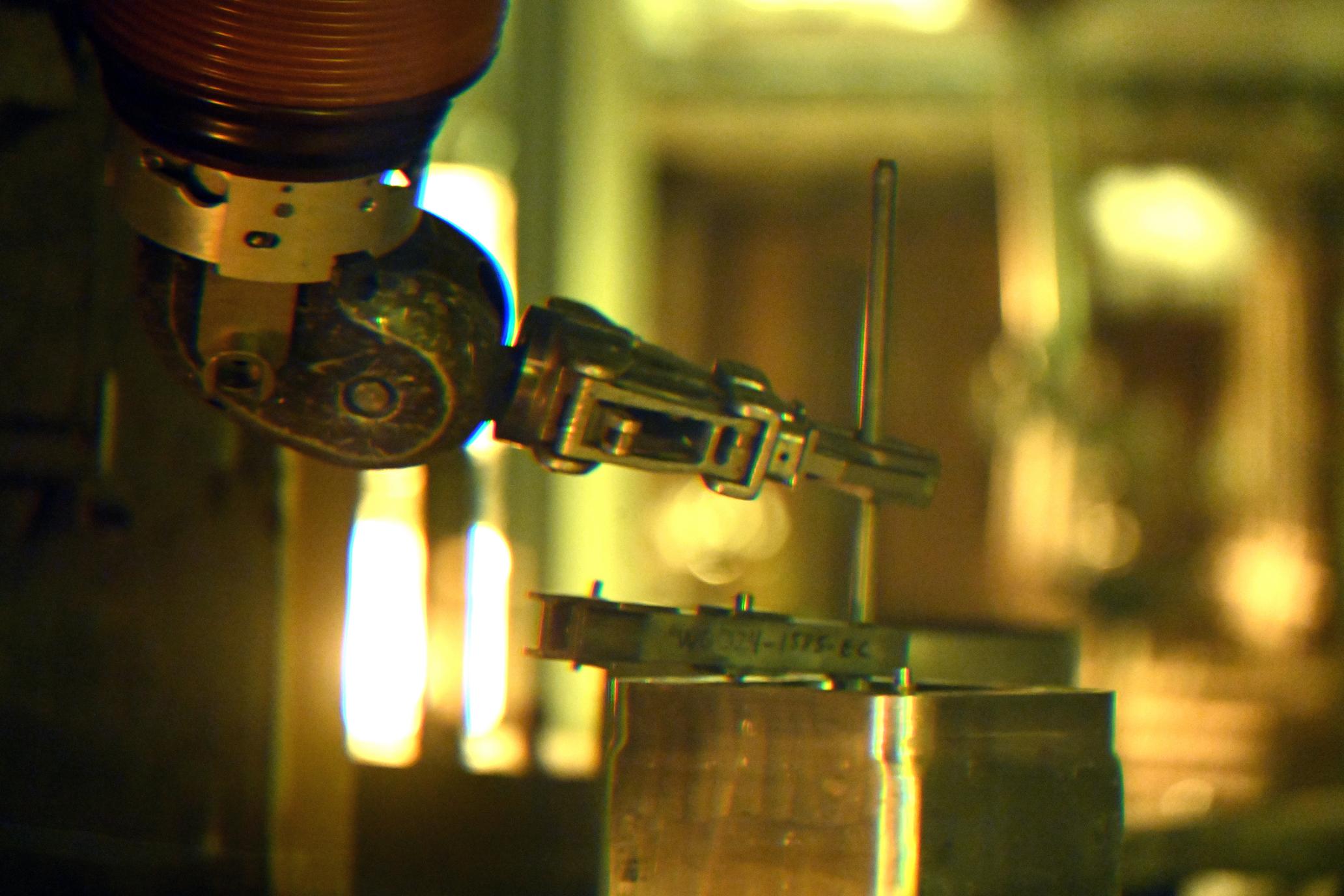
Then, experts will puncture some of the fuel rods to release and capture fission gases for analysis followed by sectioning of the rods into pieces for more detailed study.
The scientists will earmark some portions of the fuel rods for microscopy to study irradiation-induced microstructure changes to the fuel and cladding as well as detailed chemical analysis to quantify the local uranium depletion (i.e. “burnup”). Cladding samples will undergo mechanical testing and measurements to determine the amount of hydrogen the cladding picked up during irradiation, which affects its ductility, or how much it can be stretched without breaking.
Experts will also refabricate small segments into a miniature rod for safety tests in the Transient Reactor Test Facility (TREAT), also located at MFC.
Experts at TREAT have lots of experience performing safety tests on newly minted nuclear fuels over the past five years since the facility’s restart. “Now we have the opportunity to test fuels in their most vulnerable state,” said Colby Jensen, INL technical lead in charge of experimental programs at TREAT. “The fuels’ properties and performance evolve with radiation exposure in the commercial reactor core.”
In TREAT, the fuels will undergo loss-of-coolant accident testing and reactivity-initiated accident testing, which simulates a fuel experiencing a sharp increase in power in a commercial reactor core. Both classes of hypothetical accidents result in high temperatures that overheat the fuel, degrading its performance.
INL is also adding new water loops in the Advanced Test Reactor (ATR) to accommodate fuels from the shipment. ATR was designed specifically to produce high levels of neutrons to mimic in months or years the neutron damage that fuels and other nuclear materials might incur over decades in a commercial reactor.
After the safety testing in TREAT and ATR, the fuel will go back to the hot cells for more characterization.
“We want to know the fuel’s limits,” Jensen said. “The combination of ATR, TREAT and the hot cells is really special. It’s a unique opportunity to do the full suite of these kind of tests, especially on these materials.”
Fuel cycle, electrochemistry, storage
Many of the fuel rods will also provide material for experiments in fuel recycling and storage.
INL was an important contributor to the recent Joint Fuel Cycle Studies program, evaluating electrochemical recycling technologies as an option to manage used fuel. The fuel rods from the shipment will allow researchers to test those technologies — especially nonproliferation monitoring technologies — on more recent fuel types.
“While a fair amount of older spent fuel is on-site at INL, this fuel plant includes rods with much higher burnup, much more representative of modern and future burnups,” said Ken Marsden, INL’s senior technical advisor for fuel science and technology. “It is much more representative, interesting and challenging for recycling studies due to the much higher fission product and minor actinide loadings.”
Likewise, the fuel will help researchers understand how accident tolerant and high burnup fuels might behave in long-term storage. The material properties of spent fuel rods relevant to dry cask storage conditions will be measured to understand the aging behavior of stored fuel.
INL leadership
The research enabled by the commercial shipment will solidify INL’s leadership in a broad array of nuclear energy research, development and demonstration programs. The research is not only important for the NRC and INL’s domestic sponsors including DOE’s Office of Nuclear Energy, the National Nuclear Security Administration and private entities, but also international partners including regulatory bodies in Japan and Western Europe.
“I’ve been involved in this since 2014, since TREAT restart was initiated, and we’ve been talking about this shipment of materials ever since then,” Jensen said. “It’s not a lot of material, but there is so much value that comes out of it.”
“We wouldn’t be able to get across the finish line with these technologies if we couldn’t examine the rods,” said David Kamerman, a nuclear fuel research and development engineer at INL. “It’s a really big deal. There are not many places in the world that can do the work, and none of them match the capability of Idaho National Laboratory.”